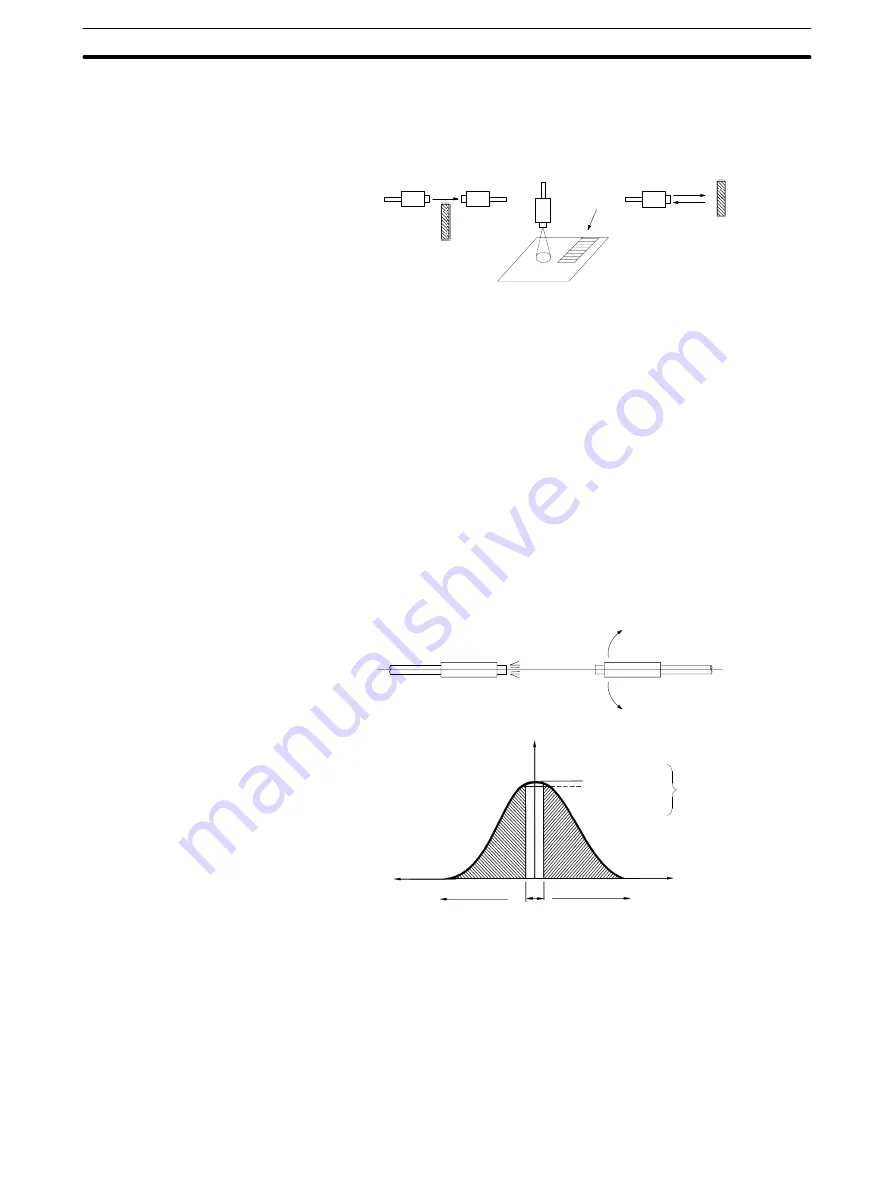
147
4. Move the object and press the teaching button. If teaching is successful, the
teaching indicator will turn from orange to green. If teaching is unsuccessful,
the teaching indicator (orange) will flash, in which case change the position
of the object and the sensing distance that have been set and repeat from
step 3.
Light is received.
Mark
Base
5. Set the mode selector to RUN to complete the sensitivity setting on the E3X-
MA11.
Light Axis Adjustment with Flashing Function
•
This function enables the user to easily adjust the light axis of a thru-beam fiber
with the light source flashing.
•
If the light projection fiber head axis and the light reception fiber head axis do
not agree with each other, and the amount of light received becomes 90% of
the peak value or less, the flashing function of the E3X-MA11 will operate. The
E3X-MA11 retains the peak value when the mode selector is set to SET so that
the axes of the fiber heads can be easily adjusted to agree with each other.
When the axes agree, the tip of the fiber for light emission will be lit.
•
If a Remote Console is connected to the Sensor Unit, the buzzer of the Remote
Console will beep intermittently when the flashing function starts operating.
The buzzer will stop beeping when the axes agree and the tip of the fiber for
light emission is lit.
•
Teaching is possible by pressing the teaching button while the flashing function
is operating.
Optical
input
The peak of
light reception
90% of the
peak value
Lit in
this
range.
Angle of
the head
(
θ
)
Flashing
Lit
Flashing
Fiber for light emission
Fiber for light
reception
θ
4-1-2 E3C-MA11 Photoelectric Module
Sensitivity Adjustment
There are three sensitivity adjustment methods. Choose the most optimum
method according to the application.
Maximum Sensitivity Setting
1, 2, 3...
1. Set the mode selector to SET. When using a thru-beam fiber sensor, adjust
the optical axis using the flashing function of the thru-beam fiber sensor.
2. Press the teaching button for 3 s minimum. The teaching indicator will turn
from orange to green in 3 s.
Operation without CQM1-TU001 Remote Console
Section 4-1
Summary of Contents for CQM1H - 08-2005
Page 1: ...Cat No W238 E1 8 Dedicated I O Units CQM1H CQM1 series OPERATION MANUAL SYSMAC ...
Page 2: ......
Page 3: ...CQM1H CQM1Series Dedicated I O Units Operation Manual Revised August 2000 ...
Page 4: ......
Page 6: ......
Page 12: ......
Page 21: ...1 PART I B7A Interface Unit CQM1 B7A02 CQM1 B7A03 CQM1 B7A12 CQM1 B7A13 CQM1 B7A21 ...
Page 22: ......
Page 42: ......
Page 45: ...25 PART II G730 Interface Unit CQM1 G7M21 CQM1 G7N01 CQM1 G7N11 ...
Page 46: ......
Page 62: ......
Page 72: ......
Page 74: ...Appendix A Specifications 54 Dimensions Common for Master and Expansion Master Unit mm ...
Page 78: ......
Page 79: ...59 PART III I O Link Unit CQM1 LK501 ...
Page 80: ......
Page 88: ......
Page 92: ......
Page 93: ...73 PART IV Analog Input Unit and Analog Power Supply Units CQM1 AD041 CQM1 IPS01 CQM1 IPS02 ...
Page 94: ......
Page 118: ......
Page 120: ......
Page 121: ...101 PART V Analog Output Unit and Analog Power Supply Units CQM1 DA021 CQM1 IPS01 CQM1 IPS02 ...
Page 122: ......
Page 126: ......
Page 140: ......
Page 142: ......
Page 144: ......
Page 156: ......
Page 172: ......
Page 186: ......
Page 187: ...167 PART VII Linear Sensor Interface Units CQM1 LSE01 CQM1 LSE02 ...
Page 188: ......
Page 192: ......
Page 204: ......
Page 218: ......
Page 238: ......
Page 242: ......
Page 246: ......
Page 248: ......
Page 250: ......