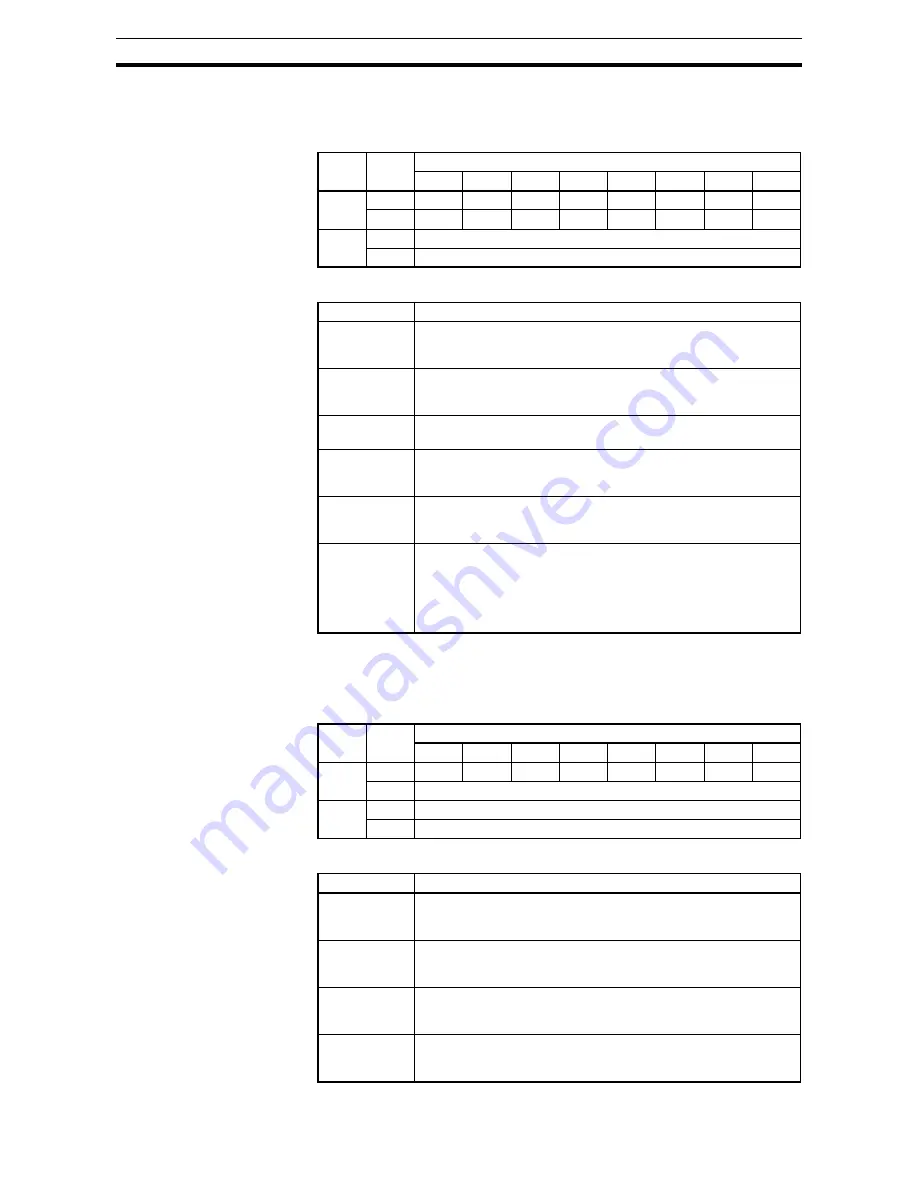
44
Extended Speed Control IO (21/71)
APPENDIX B
B-2
Extended Speed Control IO (21/71)
Assembly ID 21: Extended
Speed Control Output
Note
For safety reasons, the FWD, REV and RST command operation requires a
rising edge (0 to 1 transition) after power on and fault/trip reset.
Assembly ID 71: Extended
Speed Control Input
Table B-5
Extended Speed Control Output - Assembly 21 Allocation
Word
Byte
Bit Allocation
Bit 7
Bit 6
Bit 5
Bit 4
Bit 3
Bit 2
Bit 1
Bit 0
n
0
-
REF
CTR
-
-
RST
REV
FWD
1
-
-
-
-
-
-
-
-
n + 1
2
Rotational Speed Reference (Low Byte)
3
Rotational Speed Reference (High Byte)
Table B-6
Extended Speed Control Output - Assembly 21 Description
Name
Description
FWD
Forward run command
0: Stop
1: Forward run
REV
Reverse run command
0: Stop
1: Reverse run
RST
Fault reset
Reset fault / trip condition on transition from 0 to 1
CTR
NetCtrl run command selection
0: Setting of inverter parameter A002
1: Network controlled
REF
NetRef speed reference selection
0: Setting of inverter parameter A001
1: Network controlled
Rotational
Speed Refer-
ence
Reference rotational speed. Unit: [RPM]/[0.1 Hz]/[0.01 Hz].
If Motor poles setting for RPM (inverter parameter P049 is set to
zero, the Unit depends on the inverter mode (d060):
d060 = 2 (High Frequency mode): Unit is [0.1 Hz]
d060 != 2 (High Frequency mode): Unit is [0.01 Hz]
Table B-7
Extended Speed Control Input - Assembly 71 Allocation
Word
Byte
Bit Allocation
Bit 7
Bit 6
Bit 5
Bit 4
Bit 3
Bit 2
Bit 1
Bit 0
n
0
ARF
RFN
CFN
RDY
DRR
DFR
WR
FLT
1
Drive status
n + 1
2
Rotational Speed Monitor (Low Byte)
3
Rotational Speed Monitor (High Byte)
Table B-8
Extended Speed Control Input - Assembly 71 Description
Name
Description
FLT
Fault
0: Normal
1: Fault/trip
WR
Warning
0: Normal
1: Warning
DFR
During forward run
0: Stop/reverse
1: During forward run
DRR
During reverse run
0: Stop/forward
1: During reverse run
Summary of Contents for 3G3AX-MX2-DRT-E
Page 6: ...vi...
Page 14: ...xiv Compliance with EC Directives...
Page 20: ...6 Introduction to DeviceNet Section 1 3...
Page 46: ...32 Monitoring additional Inverter status using COS Section 4 9...
Page 56: ...42 APPENDIX A...
Page 68: ...54 Extended Speed and Acceleration Control IO 110 111 APPENDIX B...
Page 84: ...70 AC DC Drive Object Class 0x2A APPENDIX D...