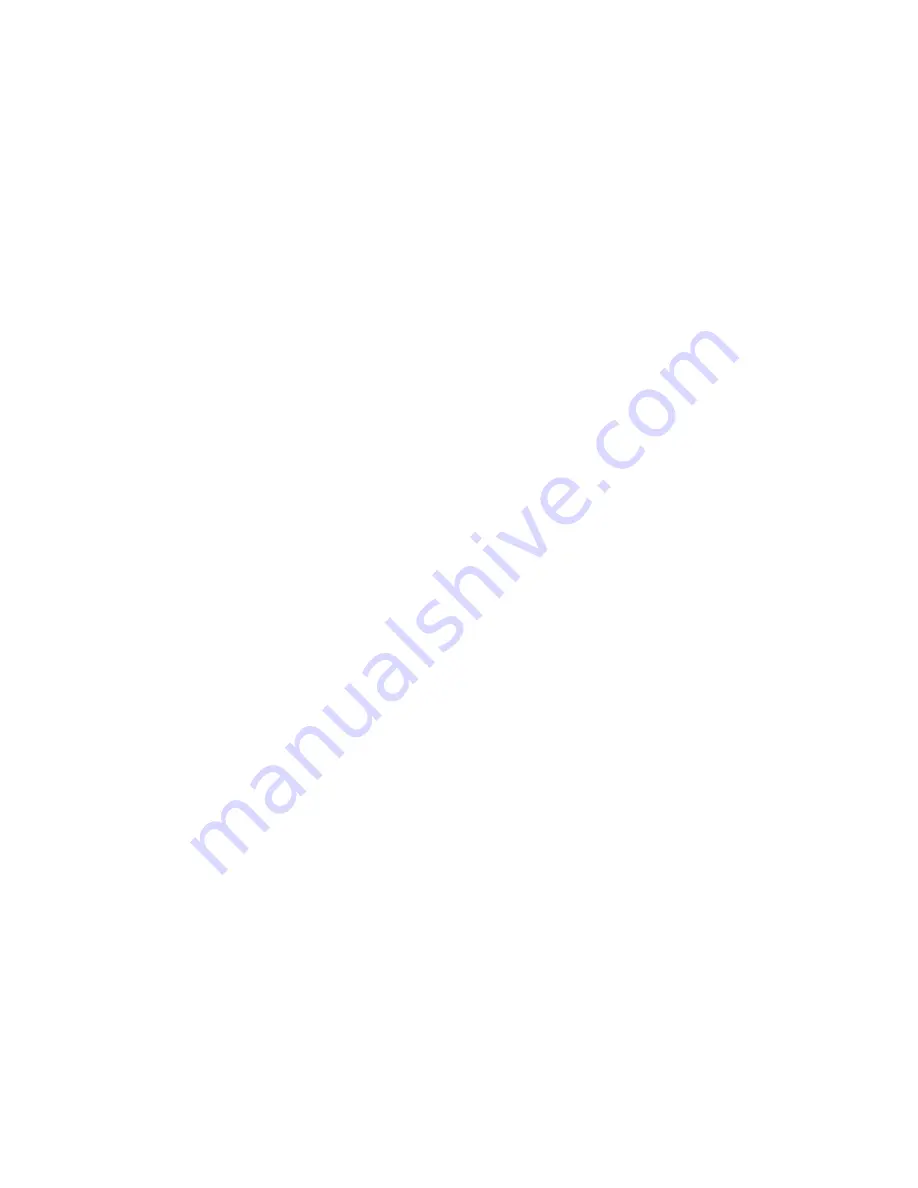
OM0295
Rev 2 September 2020
Page 60 of 103
7.7 Airflow Smoke Pattern Test
The airflow smoke pattern test is performed using a smoke source (i.e. smoke tubes) in and around the cabinet workzone
and access opening to determine a visual representation of the cabinet’s containment performance. To perform the test,
the smoke source should be passed through the following areas:
1.
A smoke source shall be passed from one end of the cabinet to the other, along the center line of the work surface,
at a height of 4 inches (102mm) above the top of the access opening.
2.
A smoke source shall be passed from one end of the cabinet to the other, 1 inch (25mm) just inside the view
screen, at a height 6 inches (152mm) above the top of the access opening.
3.
Pass a smoke source along the edges of the entire perimeter of the work opening approximately 1.5 inches
(38mm) outside the cabinet, with particular attention paid to corners and vertical edges.
4.
Pass a smoke source 2 inches (51mm) from the sides up inside of the window at the side channel seals, and along
inside of the cabinet along the top of the work area or immediately below the wiper gasket.
The criteria used to evaluate the smoke patterns is the following:
1.
The smoke inside the cabinet shall show smooth downward flow with no dead spots or reflux.
2.
No smoke shall escape from inside the cabinet.
3.
No smoke refluxes out of the cabinet once drawn in, nor does smoke billow over the worksurface or penetrate
onto it.
4.
No smoke shall escape from the cabinet.
7.8 Site Installation Assessment Tests
These tests are performed to verify the sash position, airflow or pressure setpoint where an audible and/or visual alarm will
activate to signify unfavorable operating conditions within the Biosafety cabinet and/or the remote exhaust blower.
7.8.1
Sash Alarm
Step 1: With sash alarm switch enabled, raise the sliding sash 1inch (2.5cm) above the manufacturer’s
designated sash height for normal operation. Verify that the audible/visual alarm activates/sounds.
Step 2: Return the sash to its normal operating height.
7.8.2
Airflow or Pressure Alarm (Verified During Exhaust Airflow Calibration)
Step 1: Using the primary or secondary inflow test method, lower the exhaust airflow to reduce the total
flow by 20% from the certified testing value.
Step 2: Verify that the alarm activates when the total flow has dropped to this point.
Step 3: Adjust alarm setpoint as necessary.
Summary of Contents for LabGard NU-560-400
Page 7: ...OM0295 Rev 2 September 2020 Page 7 of 103...
Page 9: ...OM0295 Rev 2 September 2020 Page 9 of 103...
Page 10: ...OM0295 Rev 2 September 2020 Page 10 of 103...
Page 16: ...OM0295 Rev 2 September 2020 Page 16 of 103...
Page 17: ...OM0295 Rev 2 September 2020 Page 17 of 103...
Page 32: ...OM0295 Rev 2 September 2020 Page 32 of 103 Set New Password Retype New Password...
Page 43: ...OM0295 Rev 2 September 2020 Page 43 of 103...
Page 48: ...OM0295 Rev 2 September 2020 Page 48 of 103...
Page 80: ...OM0295 Rev 2 September 2020 Page 80 of 103...
Page 96: ...OM0295 Rev 2 September 2020 Page 96 of 103...
Page 97: ...OM0295 Rev 2 September 2020 Page 97 of 103...
Page 98: ...OM0295 Rev 2 September 2020 Page 98 of 103...
Page 99: ...OM0295 Rev 2 September 2020 Page 99 of 103...
Page 100: ...OM0295 Rev 2 September 2020 Page 100 of 103...
Page 101: ...OM0295 Rev 2 September 2020 Page 101 of 103...