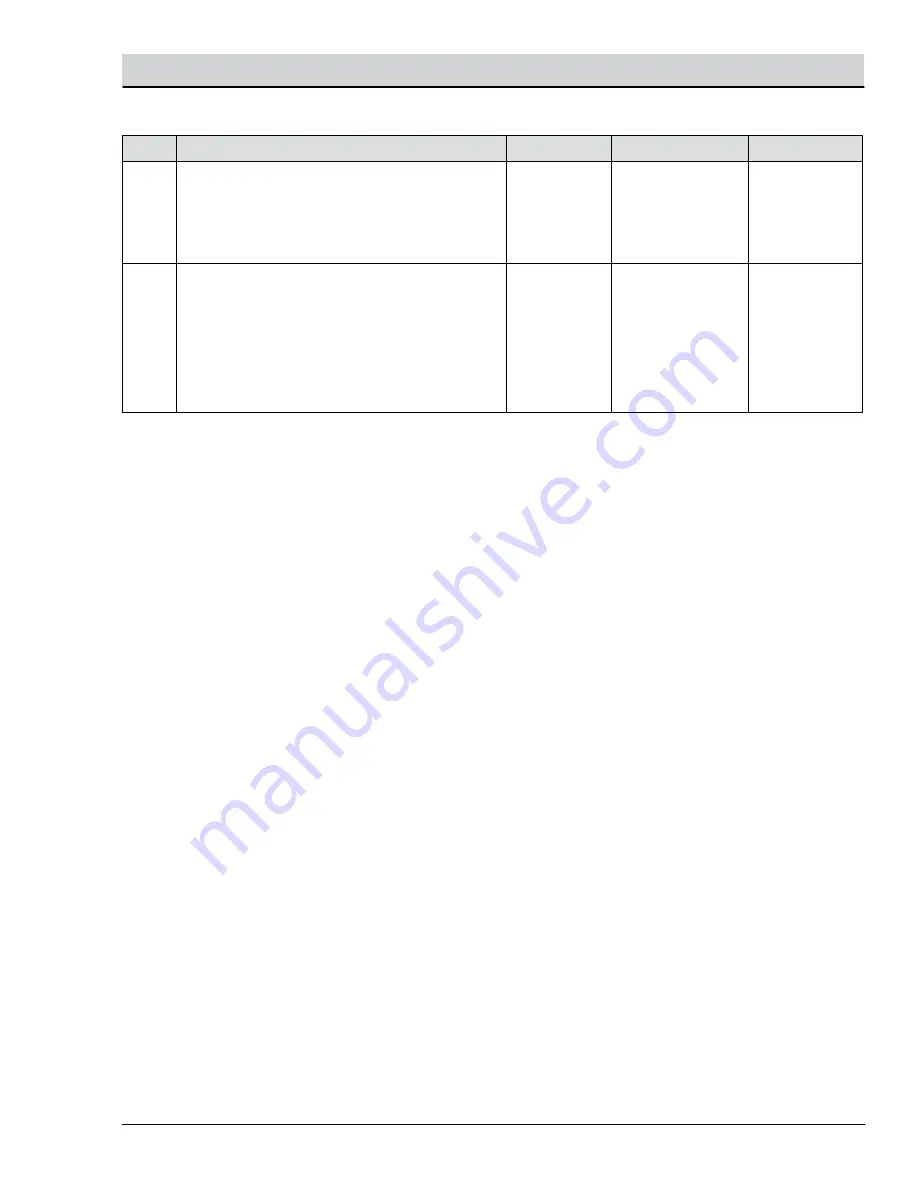
SS300 Service Information (3-2017)
63
TROUBLESHOOTING
VACUUM FAN FAILED TO TURN ON
STEP
ACTION
VALUE(S)
YES
NO
1
•
Key On
•
Enable vacuum fan
•
Is there a flashing BDI fault fault code pres
-
ent?
See “Faults” in
the TROUBLE-
SHOOTING sec-
tion of this manual
Go to Step #2
2
•
Key On
•
Enable vacuum fan
•
Test voltage applied to the vacuum fan
subsystem as shown on the electrical
schematic
•
Are the electrical circuits operating as
shown on the electrical schematic?
Go Back to Step
#1
Identify Voltage
Drop Location
and Repair or
Replace Nec-
essary Compo-
nents
Terms:
BDI = Battery Discharge Indicator