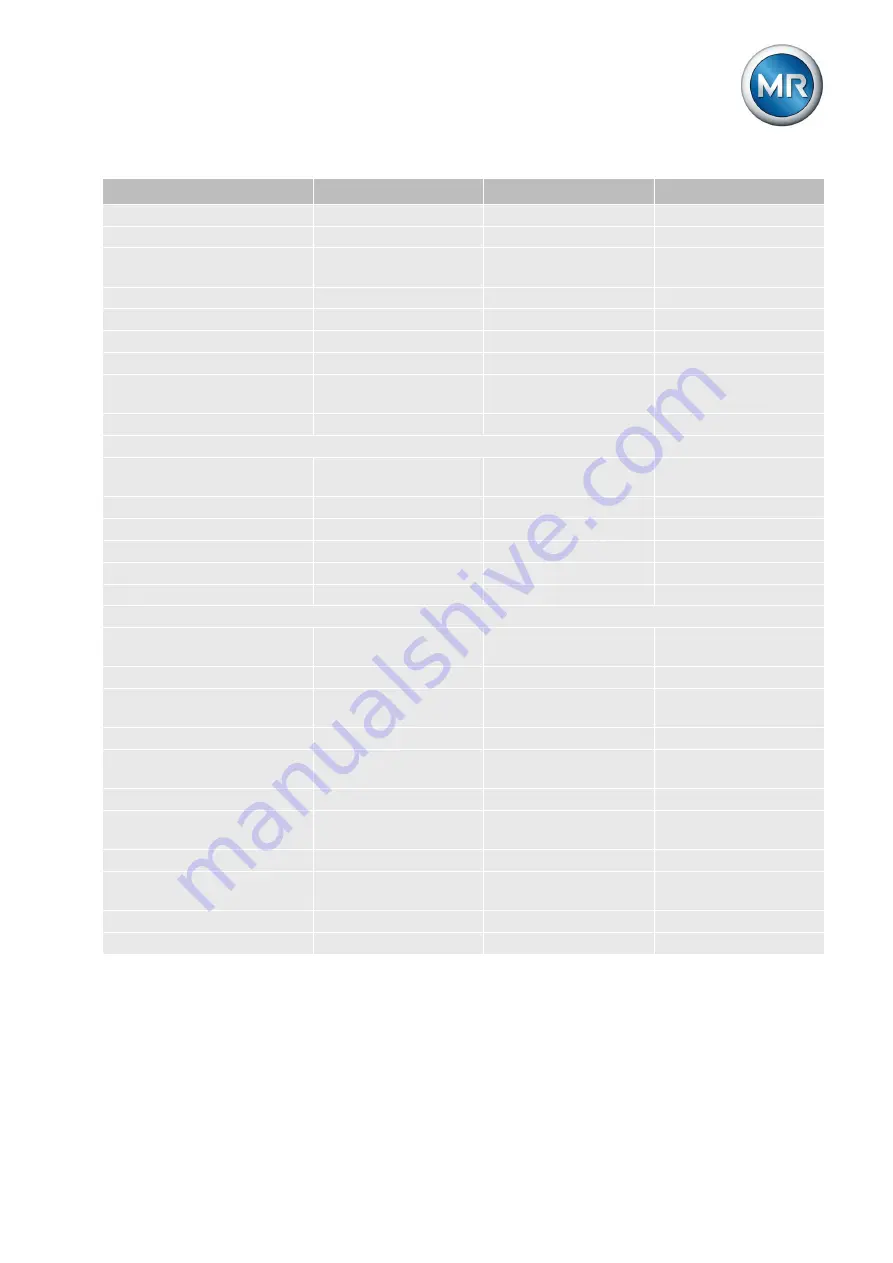
12 Overview of parameters
Maschinenfabrik Reinhausen 2014
157
222/08 EN
TAPCON® 240
Parameter
Setting range
Factory setting
Current setting
Output 3 upper value
-9999...9999
0
Output 3 lower value
-9999...9999
0
Output 3 upper
1 mA; 10 mA; 20 mA;
10 V
20 mA
Output 3 lower
+4 mA
Output 4 measured value
Off
Output 4 upper value
-9999...9999
0
Output 4 lower value
-9999...9999
0
Output 4 upper
1 mA; 10 mA; 20 mA;
10 V
20 mA
Output 4 lower
+4 mA
Configuration > Memory
Event memory
256 k; 512 k; 1024 k,
2048 k
256 k
Average value interval
1 s
U< threshold
60...100 %
90 %
U< memory
34...160 V
90.0 V
U> threshold
100...140 %
110 %
U> memory
34...160 V
110.0 V
Configuration > Communication interface
Comm. port CIC1
RS232; RS485; Ether-
net; OF
RS232
Baud rate comm. CIC1
9.6...57.6 kilobaud
9.6 kilobaud
Network address CIC1
0.0.0.0...25525525525
5
0.0.0.0
TCP port CIC1
0...9999
-
Fiber-optic cable light On/Off
CIC1
On; Off
Off
Local SCADA Address CIC1
0…9999
1
SCADA Master Address
CIC1
0…9999
3
Unsolicited messages CIC1
On; Off
Off
Repeatedly unsolicited mes-
sages CIC1
0…100
3
Appl. conf. timeout CIC1
1…60 s
5 s
Transmission delay CIC1
0…254
4 ms
Table 45: Overview of parameters
Summary of Contents for tapcon 240
Page 1: ...Voltage Regulator TAPCON 240 Operating Instructions 222 08 EN ...
Page 173: ......