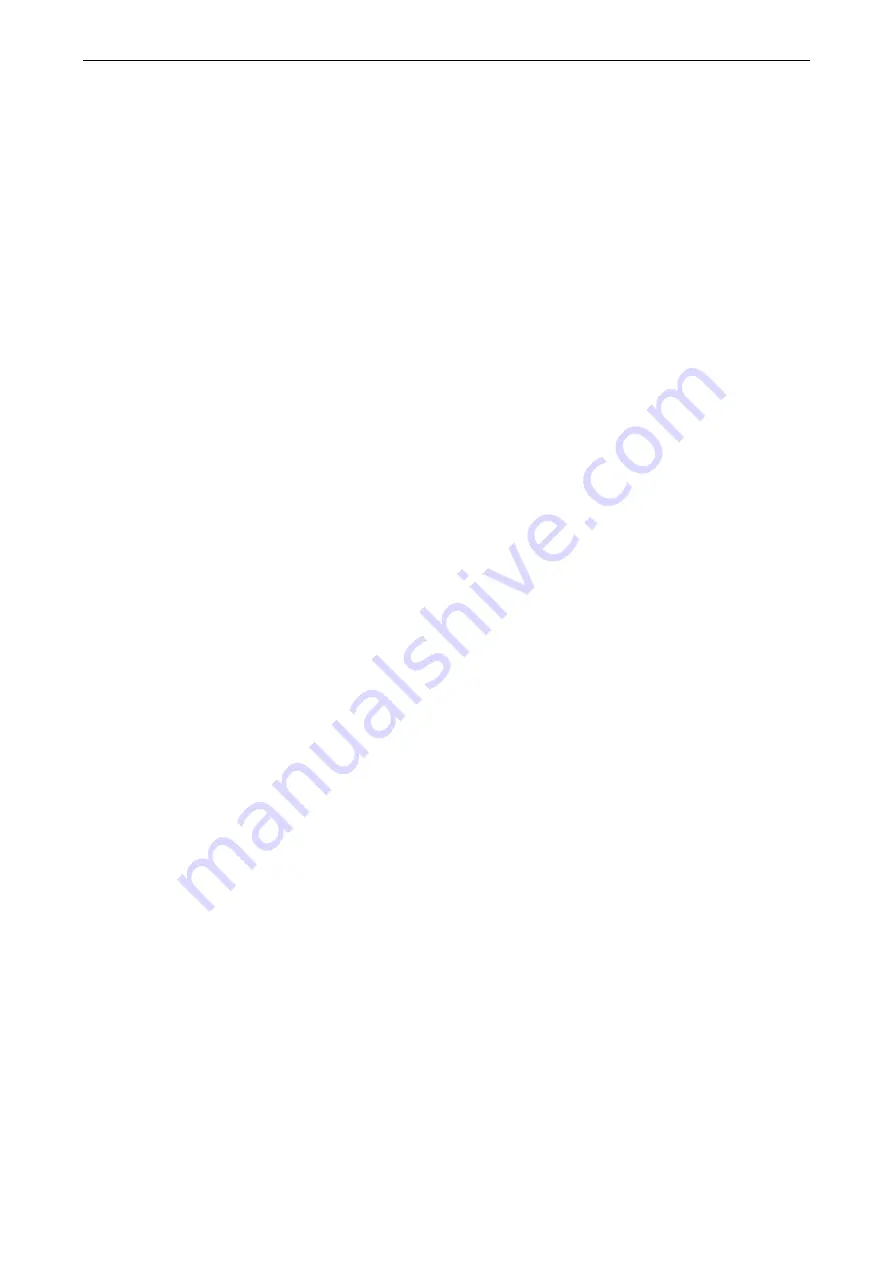
ioLogik E2200 Series
Introduction
1-9
ioLogik E2242 Specifications
Inputs and Outputs
Analog Inputs:
4 channels
Configurable DIOs:
12 channels
Analog Input
Type:
Differential input
Resolution:
16 bits
I/O Mode:
Voltage / Current
Input Range:
±150 mV, 0 to 150 mV, ±500 mV, 0 to 500 mV, ±5 V, 0 to 5 V, ±10 V, 0 to 10 V, 0 to 20 mA,
4 to 20 mA
Accuracy:
±0.1% FSR @ 25°C
±0.3% FSR @ -10 and 60°C
±0.5% FSR @ -40 and 75°C
Sampling Rate:
All channels:
• 32 samples/sec
Per channel:
• 8 samples/sec
Single channel:
• 100 samples/sec
Input Impedance:
200K ohms (min.)
Built-in Resistor for Current Input:
120 ohms
Digital Input
Sensor Type:
Wet Contact (NPN or PNP) and Dry Contact
I/O Mode:
DI or event counter
Dry Contact:
• On: short to GND
• Off: Open
Wet Contact(DI to GND):
• On: 0 to 3 VDC
• Off: 10 to 30 VDC
Common Type:
6 points per COM
Isolation:
3K VDC or 2K Vrms
Counter Frequency:
900 Hz, power off storage
Digital Filtering Time Interval:
Software selectable
Digital Output
Type:
Sink
I/O Mode:
DO or Pulse Output
Pulse Output Frequency:
1 kHz
Over-voltage Protection:
45 VDC
Over-current Protection:
2.6 A (4 channels @ 650 mA)
Over-temperature Shutdown:
175°C (min.)
Current Rating:
200 mA per channel
Isolation:
3K VDC or 2K Vrms
Power Requirements
Power Consumption:
178 mA @ 24 VDC
MTBF
(mean time between failure)
Time:
204,391 hrs
Database:
Telcordia (Bellcore)
Summary of Contents for ioLogik E2210
Page 138: ...ioLogik E2200 Series Cable Wiring D 4 Digital Output Sink Type...
Page 139: ...ioLogik E2200 Series Cable Wiring D 5 RTD Input Wiring Structure 2 wire 3 wire...
Page 140: ...ioLogik E2200 Series Cable Wiring D 6 Thermocouple Input Wiring Structure 2 wire...
Page 144: ...ioLogik E2200 Series Input and Output Terminal E 4 ioLogik E2262 I O left to right...