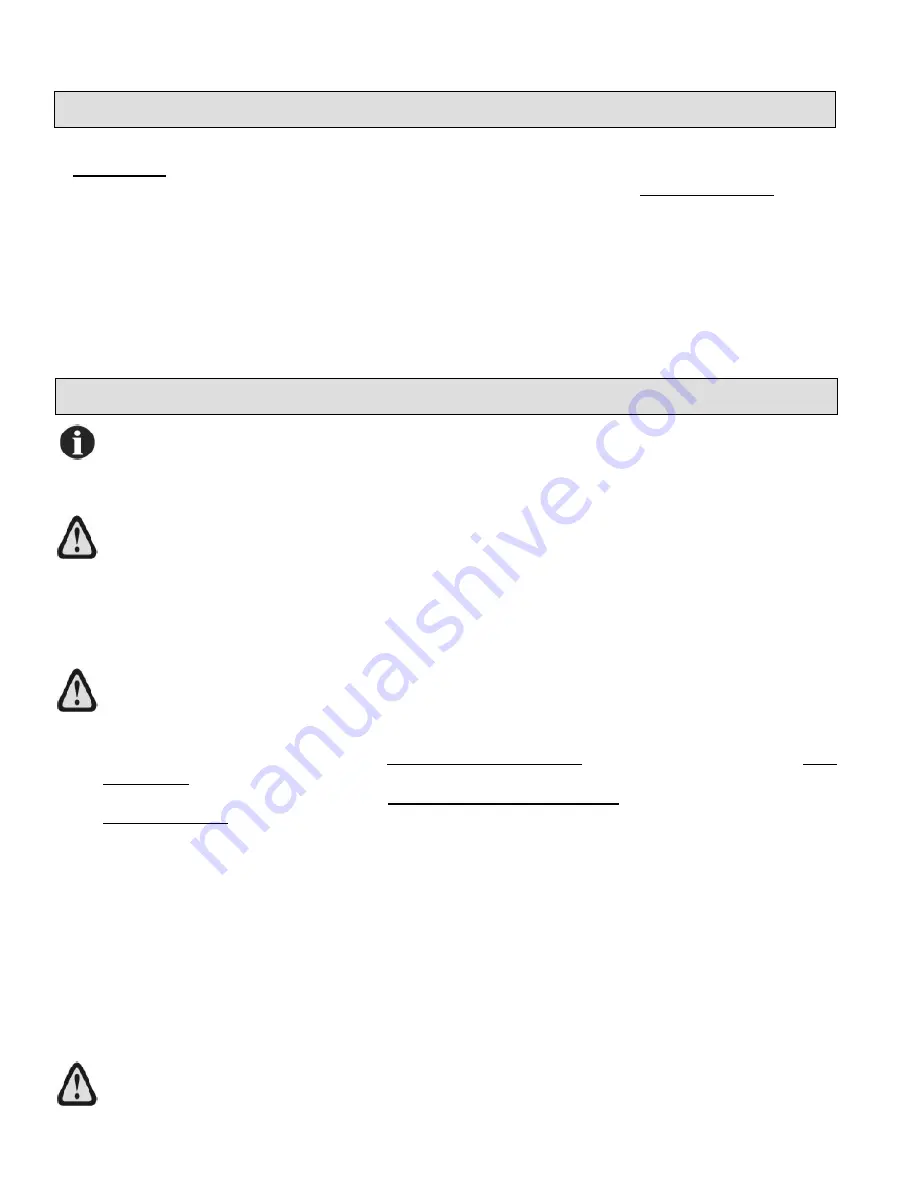
- 43 -
Wiring Harnesses can be split into two categories:
Power Cables
and
Motor/Actuator Harnesses.
In the case
of power cables, there are several unique cables available in order to interface with the various base electronics
(controllers) utilized by the different wheelchair base manufacturers. The number of actuator harnesses required
for any particular power positioning system is determined by the number of motor functions available.
i) Power Cables
- draw power from the wheelchair base in order to operate the power positioning system.
The power cable is the first link in the series of wiring harnesses and typically draws power from the wheelchair
batteries via the base controller (electronics). The final wiring configuration will vary depending on the type of
PPS electronics and the type of wheelchair base.
ii) Motor/Actuator Harnesses
- distribute the power to the individual motors on the Power Positioning
System. The number of actuator harnesses is in direct correlation with the number of motor functions available.
IMPORTANT!
Programming of the
Tipsy Angle Sensor
(via the M270 Remote Attendant Control)
may only be performed by a Qualified Technician. Program access into the M270 is password protected.
If you have questions or concerns regarding your existing program settings, or any of the available
program options, please contact your local Dealer or Service Provider for assistance.
WARNING! Risk of Death or Serious Injury
• The angle at which the limit switches/lockouts are set is
critical
to the safe operation of the power
positioning system. Improper set-up may result in serious injury or death.
• Motion Concepts will not be liable for any injuries or damage sustained when adjustments are made
beyond the factory recommended settings.
• To ensure proper set-up, adjustments to safety lockouts and limits must ONLY be performed by a
Qualified Technician.
WARNING! Risk of Death or Serious Injury
Operating the wheelchair with the seat back angle position beyond the recommended
drive lock-out (DLO) angle can cause instability resulting in death or serious injury from the
wheelchair tipping over.
• For wheelchair systems programmed WITH reduced drive speed, the maximum recommended DLO
angle is 30° (refer to
Section 4.3.1
)
• For wheelchair systems programmed WITHOUT reduced drive speed, the maximum recommended
DLO angle is 25° (refer to
Section 4.3.1
)
•
NEVER operate the wheelchair or elevate/lower the seat while in any back angle position that exceeds
the maximum recommended DLO angle.
•
If the drive lock-out does not stop the wheelchair from operating, or does not stop the seat from elevating
when the tilt/recline back angle exceeds the recommended DLO angle, STOP operation of the wheelchair
IMMEDIATELY. Return the seat to the HOME position for safe operation. DO NOT attempt to adjust
the drive lock-out. Contact your Dealer/Service Provider IMMEDIATELY to arrange service.
The wheelchair user MUST have a clear line of sight to drive safely.
•
Upon initial chair delivery, tilt and recline the seat back to the farthest driving position (IMMEDIATELY
before drive lock-out engages) and ensure there is a clear line of sight present in which to drive the
wheelchair. If a clear line of sight is not present, have the back angle repositioned or have the lockout
angle readjusted until a clear line of sight is achieved for safe driving.
WARNING! Risk of compromised wheelchair stability and serious personal injury.
• When operating/driving the wheelchair in a tilted and/or reclined and/or elevated position, ensure
the wheelchair is on a smooth level surface (even at reduced speed).
4.2 Wiring Harnesses
4.3 Safety Lockouts and Limit Switches
4.0
4.0
ELECTRONICS
ELECTRONICS
Summary of Contents for ULTRA-LOW MAXX UPFRONT MPPS
Page 99: ......