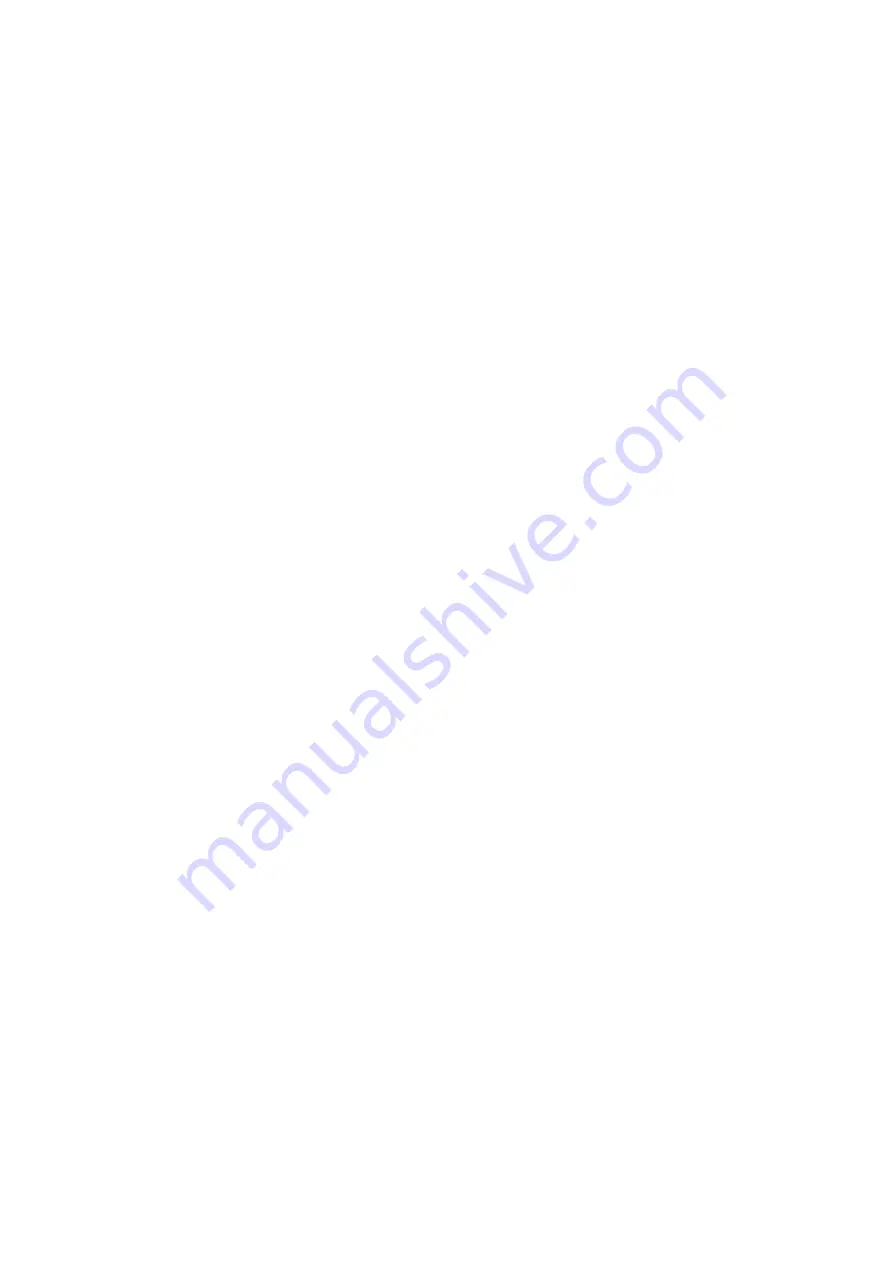
— xiv —
The device incorporates a mechanism that securely supports works
Air-suction work clamping system has been introduced to the table unit on which works are se-
cured. This allows works to be clamped without fail and to be easily placed/removed on/from the
device. Furthermore, the table is equipped with a plate surface that protects the cutter blade at the
time of performing die-cut. Moreover, a set including an roll hanger is also available.
* Depending on characteristics and size of the material, it may not be possible to fix it securely.
With its most-advanced functions, high-quality finish is promised
Start/end point correction
In the case of processing heavy-weight works, works can be easily cut out by correcting the start
and end positions for cutting.
Pressure correction
In the case of cutting heavy-weight works, works can be fully cut with no portion remained uncut
by correcting the pressure employed to lower the tool.
Circle
θ
θθ
θ
θ
correction
When cutting out a circle, the start and points of cutting sometimes fail to align in accordance with
thickness and hardness of the work used. However, an almost regular circle can be cut out by
correcting the amount of such a departure.
Eccentric correction
The curve cutting accuracy can be improved by shifting the center toward the cutting direction.
Moreover, the cutting direction and the position of the cutter at right angle can be adjusted as
desired. This enables accurate cutting without depending on the holder accuracy.
Cutting conditions for two or more tools can be entered
The twelve cutting conditions such as pressure, speed, start/end point correction, offset, etc. can be
entered separately for two or more tools.
This devices provides a throughput that is increased by 30% at the maximum as
compared with conventional models
The device increases the total throughput by 30% at the maximum by increasing both arc cutting
speed and cutter up/down speed in terms of the X/Y directions while upgrading accuracy as com-
pared with the former models.
Summary of Contents for CF2 Series
Page 48: ...1 32...
Page 120: ...3 24...
Page 138: ...4 18...
Page 176: ...A 12 C OUTPUT SAMPLES Cutting quality 1 Cutting quality 2...
Page 177: ...A 13 ASCII dump list Sample coated...
Page 178: ...A 14 Sample E corrugated Sample B corrugated...
Page 179: ...A 15 Circle cutting R 3 5 10 20 50 100 Parameter dump list R 3 R 5 R 10 R 20 R 50 R 100...
Page 185: ......
Page 186: ...D201402 1 30 16062008 MIMAKI ENGINEERING CO LTD 2008 EM FW 2 50...