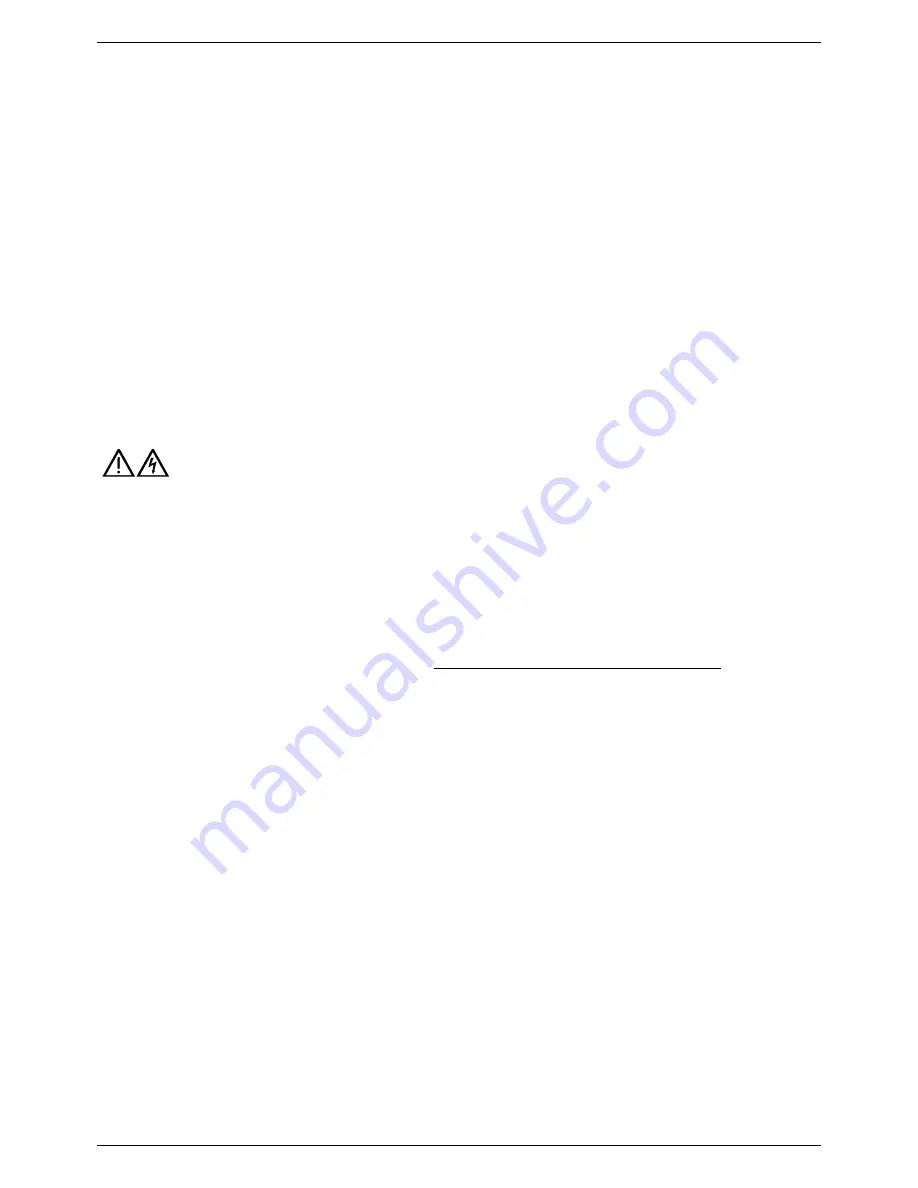
ENGLISH
963857101_G
22
22
4.8 Removal of moisture from windings
An increase of insulation resistance between phase and earth is normally obtained by removing the moisture.
Several methods can be followed for this scope:
•
Stator winding drying by internal heat source.
Heaters have to be distributed below the generator main winding stator.
•
Stator winding drying-out by self heating method.
The stator can be heated with the circulation of low voltage DC current (i.e. obtained by an industrial welding set) through the windings.
A current of about 25% of the full load current, as marked on the generator rating plate, should be used.
If both phase terminals are available, generator winding can be re-connected to adjust its internal resistance , in order to suit the direct
current supply available. A thermometer should be placed inside the stator windings.
Temperature should not be allowed to exceed 80°C.
Could be useful to cover the machine to conserve the heath.
In case it is possible have to be unclosed all the openings on frame, if available. Those openings if positioned on the top of the
generator (i.e. removing terminal box cover or removing end shields for vertical constructions) can improve moisture escape.
•
Drying of stator with oven heating
You brings the oven to 110 – 150°C maximum, the drying of winding for generators MJB 250 – 315 – 355 could continue for 4 – 10
hours depending on the starting condition insulation resistance.
If the insulation resistance doesn’t reach at least the recommended value, it’s possible that the cause is a solid contamination.
It will be in this case necessary to clear the winding once more and then repeat the drying process.
5. MAINTENANCE
All work on the electrical machine must be performed with the authorisation of the safety manager, with the machine at a
standstill, at ambient temperature and disconnected electrically from the system or the mains supply, (including the auxiliaries, such
as the anti-condensation heaters for example). All precautions to prevent the possibility of the machine being re-started
unexpectedly during the maintenance phases must be taken.
The environment in which the generator is put to work must be clean and dry.
In order to block the screws use Loctite
®
243 thread-lock, ensuring that they are not dirty with oil/grease (if necessary use Loctite
®
7063 or equivalent solvent).
ATTENTION! In the case of electrical connections, the Loctite
®
must not cover the electrical contact surfaces!
5.1 Inspection and maintenance intervals
Inspection and maintenance should take into account the importance of the plant ambient conditions (dust etc.) and operating
conditions.
As a general rule, the machine should be subjected to a first inspection after approx. 100 operating hours (in any case not
more than 1 year) and subsequent inspections when performing maintenance on prime mover.
When performing inspection check that:
- The generator operates smoothly, without noise or irregular vibrations due to bearing deterioration.
- The operating data complies with that detailed on the rating plate.
- The air inlet openings are not obstructed.
- The supply cables show no signs of deterioration and connections are firmly tight and the electrical connections are in
perfect condition (undamaged).
- Screws and nuts are firmly tightened.
- No grease leakage from supports.
For the above inspections it is not necessary to dismantle the generator, dismantling is only necessary when the bearings are cleaned
or replaced and in that occasion the following additional checks are required:
- Alignment.
- Insulation resistance.
- Tightening of all fixing bolts, screws and nuts.