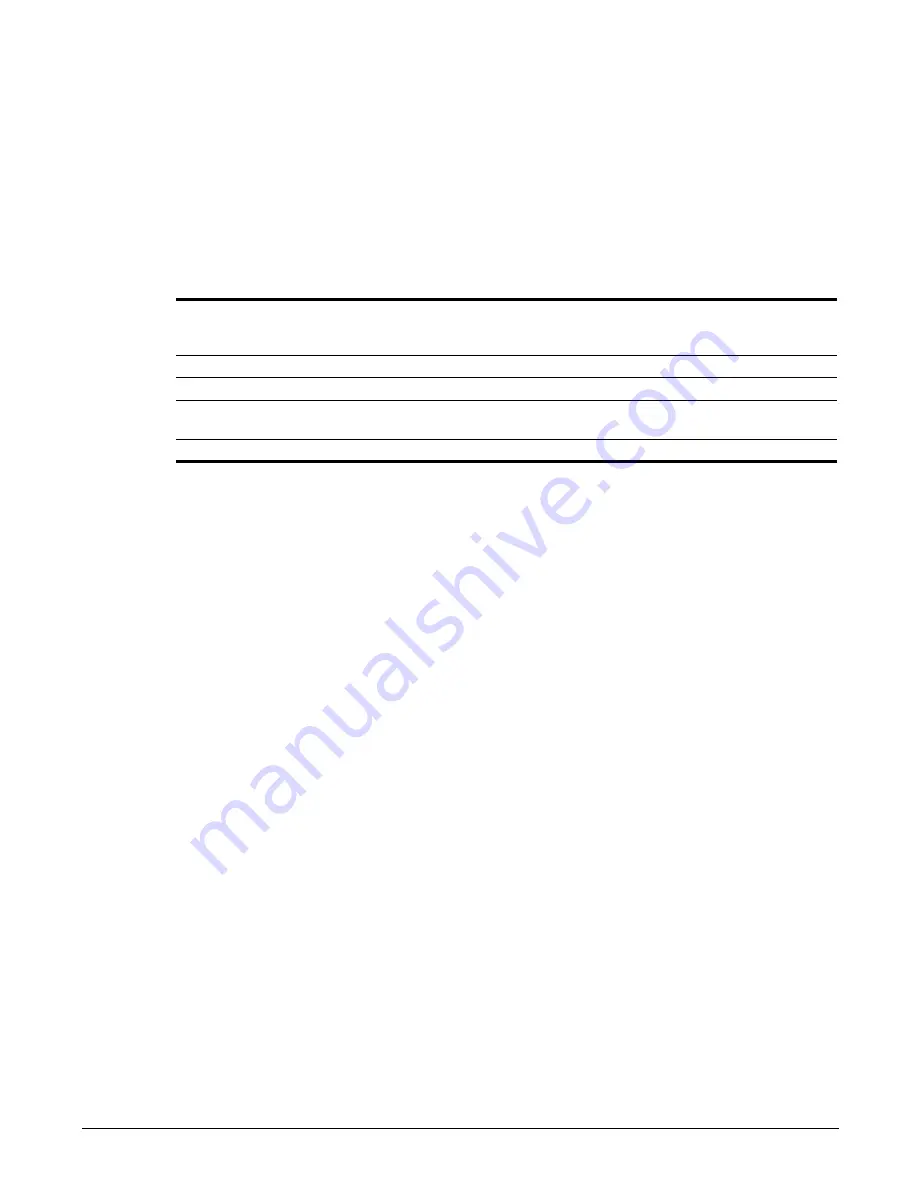
IMPULSE®•G+ & VG+ Series 4 Instruction Manual - February 2017
3-24
Wiring the Encoder Circuit
A shaft-mounted encoder is required to provide speed and shaft position feedback to
IMPULSE
®
•VG+ Series 4. Without an encoder, a flux vector control cannot operate properly.
Before you wire the encoder circuit, refer to the specification tables 3-10 and 3-11 on page 3-25 and
“Suggested Circuit Protection Specifications and Wire Size” on page 3-6.
Encoder Circuit Wiring Procedures
Table 3-9: Encoder Specifications
To wire the encoder circuit for IMPULSE
®
•VG+ Series 4 (assuming the cover and keypad are
detached):
1. Direct-couple the encoder to the motor shaft, using a zero-backlash-type coupling.
NOTE:
Do not connect the encoder to the motor with roller chain or gear drive. If unable to
direct-couple the encoder, use a timing belt to drive the encoder. (Contact Magnetek
for encoder kits.) Also, do not connect the encoder to the low-speed shaft of a speed
reducer.
2. Connect the encoder to the PG-X3 Encoder Interface Card. Refer to Figure 3-17: “PG-X3
Encoder Card Wiring” on page 3-25.
NOTE:
Use twisted-pair, shielded cable W100W impedance (Magnetek R-20/6, R-22/6,
Belden 9730, or Brand Rex T-11651). Strip the encoder wires .25 in. (5.5 mm). Keep
the wiring length less than 300 feet (for cable lengths greater than 300 feet, contact
Magnetek for information on available fiber optic cable).
3. Ground the shielded cable to Terminal FE of the PG-X3 Encoder Interface Card (ground only
one end of the shielded cable).
NOTE:
For LakeShore encoders, the shield connection is not considered “Ground.” The
shield should be grounded.
4. Whenever possible, the encoder cable should be wired in a continuous run between the motor
and drive. If it cannot be a direct run, the splice should be in its own junction box and isolated
from the power wires.
Power supply
+12 VDC (+5 VDC by CN3 jumper); if current demand is greater than 200 mA
(consult factory if inrush currents exceed 200 mA), an auxiliary power supply must
equipped - contact Magnetek to purchase
Output Type
Quadrature (A and B channels; Z is not required)
Type of output circuit
High-speed, differential line drive (open collector interface is optional).
Maximum Input
Frequency
300 kHz
Mounting method
Encoder must be direct-coupled to motor shaft, using a zero-backlash-type coupling.
Summary of Contents for Impulse G+ series 4
Page 2: ......
Page 6: ...IMPULSE G VG Series 4 Instruction Manual February 2017 iv This page intentionally left blank...
Page 12: ...IMPULSE G VG Series 4 Instruction Manual February 2017 This page intentionally left blank...
Page 13: ...C h a p t e r 1 Introduction...
Page 14: ...IMPULSE G VG Series 4 Instruction Manual February 2017 1 2 This page intentionally left blank...
Page 26: ...IMPULSE G VG Series 4 Instruction Manual February 2017 1 14 This page intentionally left blank...
Page 27: ...C h a p t e r 2 Installation...
Page 28: ...IMPULSE G VG Series 4 Instruction Manual February 2017 2 2 This page intentionally left blank...
Page 40: ...IMPULSE G VG Series 4 Instruction Manual February 2017 2 14 This page intentionally left blank...
Page 41: ...C h a p t e r 3 Wiring...
Page 42: ...IMPULSE G VG Series 4 Instruction Manual February 2017 3 2 This page intentionally left blank...
Page 66: ...IMPULSE G VG Series 4 Instruction Manual February 2017 3 26 This page intentionally left blank...
Page 67: ...C h a p t e r 4 Getting Started...
Page 68: ...IMPULSE G VG Series 4 Instruction Manual February 2017 4 2 This page intentionally left blank...
Page 87: ...C h a p t e r 5 Programming Advanced Features...
Page 88: ...IMPULSE G VG Series 4 Instruction Manual February 2017 5 2 This page intentionally left blank...
Page 223: ...C h a p t e r 6 Troubleshooting...
Page 224: ...IMPULSE G VG Series 4 Instruction Manual February 2017 6 2 This page intentionally left blank...
Page 255: ...a p p e n d i x A IMPULSE G VG Series 4 Parameter Listing...
Page 256: ...IMPULSE G VG Series 4 Instruction Manual February 2017 A 2 This page intentionally left blank...