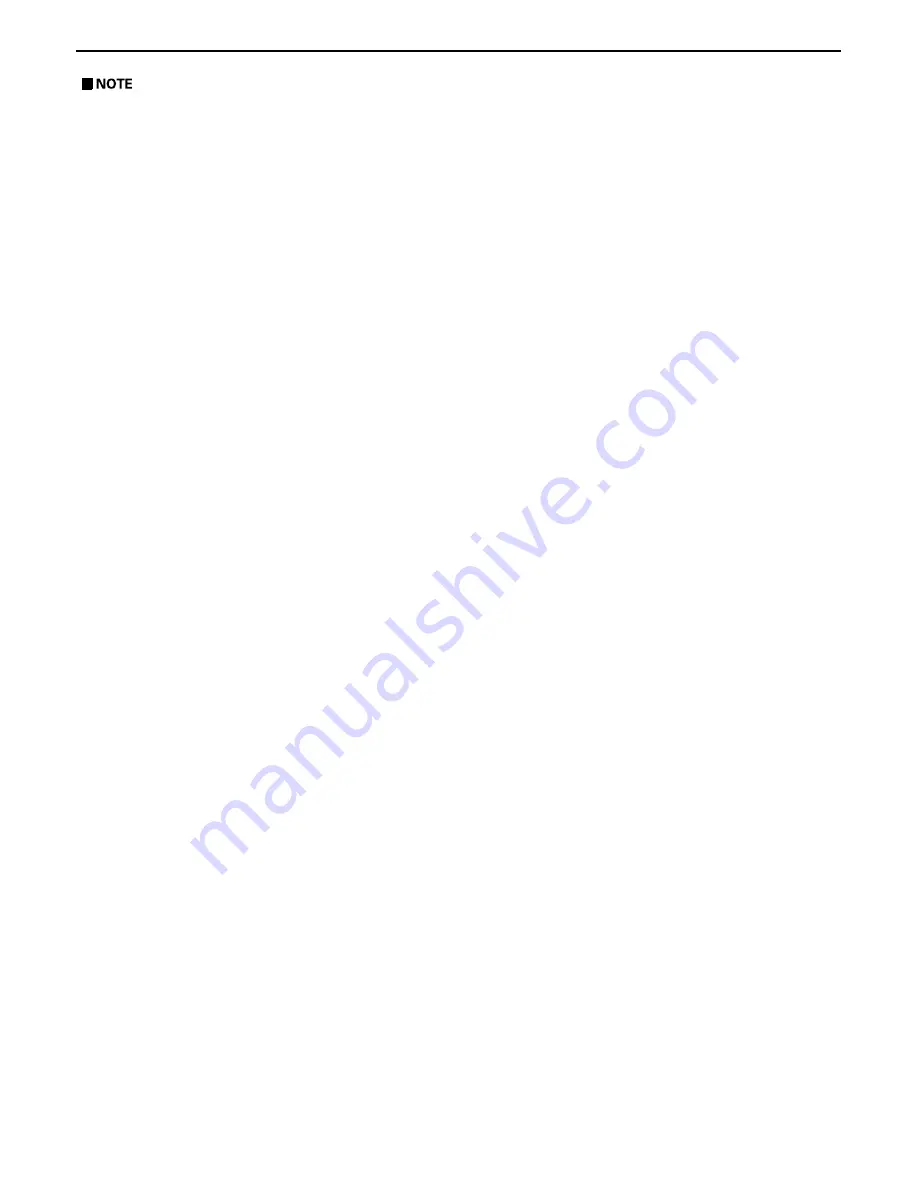
ME8200DTN, WSM
GENERAL
NG-3
A
Engine Oil : Oil used in the engine should have an American Petroleum Institute (API) service
classification and Proper SAE Engine Oil according to the ambient temperature as shown above.
Do not mix different brands together.
A
Transmission Oil : The oil used to lubricate the transmission is also used as hydraulic fluid. To insure
proper operation of the hydraulic system and complete lubrication of the transmission, it is important
that a multi-grade transmission fluid be used in this system. We recommend the use of KUBOTA SUPER
UDT fluid for optimum protection and performance.
Do not mix different brands together.
A
Indicated capacity of water and oil are manufacture's estimate.
0000003594E
KiSC issued 04, 2006 A
Summary of Contents for ME8200DTN
Page 1: ...WORKSHOP MANUAL TRACTOR ME8200DTN SUPPLEMENT KiSC issued 04 2006 A...
Page 7: ...ME8200DTN WSM SAFETY INSTRUCTIONS N5 0000003126E KiSC issued 04 2006 A...
Page 8: ...ME8200DTN WSM SAFETY INSTRUCTIONS N6 0000003588E KiSC issued 04 2006 A...
Page 9: ...ME8200DTN WSM SAFETY INSTRUCTIONS N7 0000003589E KiSC issued 04 2006 A...
Page 11: ...ME8200DTN WSM DIMENSIONS N9 DIMENSIONS 0000003590E KiSC issued 04 2006 A...
Page 12: ...NG GENERAL KiSC issued 04 2006 A...
Page 33: ...N1 ENGINE KiSC issued 04 2006 A...
Page 42: ...N2 CLUTCH KiSC issued 04 2006 A...
Page 43: ...CONTENTS 1 TRAVELLING CLUTCH N2 M1 KiSC issued 04 2006 A...
Page 57: ...N3 TRANSMISSION KiSC issued 04 2006 A...
Page 102: ...N4 REAR AXLE KiSC issued 04 2006 A...
Page 103: ...CONTENTS 1 STRUCTURE N4 M1 KiSC issued 04 2006 A...
Page 113: ...N5 BRAKES KiSC issued 04 2006 A...
Page 114: ...CONTENTS 1 STRUCTURE N5 M1 KiSC issued 04 2006 A...
Page 124: ...N6 FRONT AXLE KiSC issued 04 2006 A...
Page 125: ...CONTENTS 1 STRUCTURE N6 M1 KiSC issued 04 2006 A...
Page 144: ...N7 STEERING KiSC issued 04 2006 A...
Page 150: ...N8 HYDRAULIC SYSTEM KiSC issued 04 2006 A...
Page 179: ...N9 ELECTRICAL SYSTEM KiSC issued 04 2006 A...
Page 180: ...CONTENTS 1 WIRING DIAGRAM N9 M1 2 COLOR OF WIRING N9 M2 KiSC issued 04 2006 A...