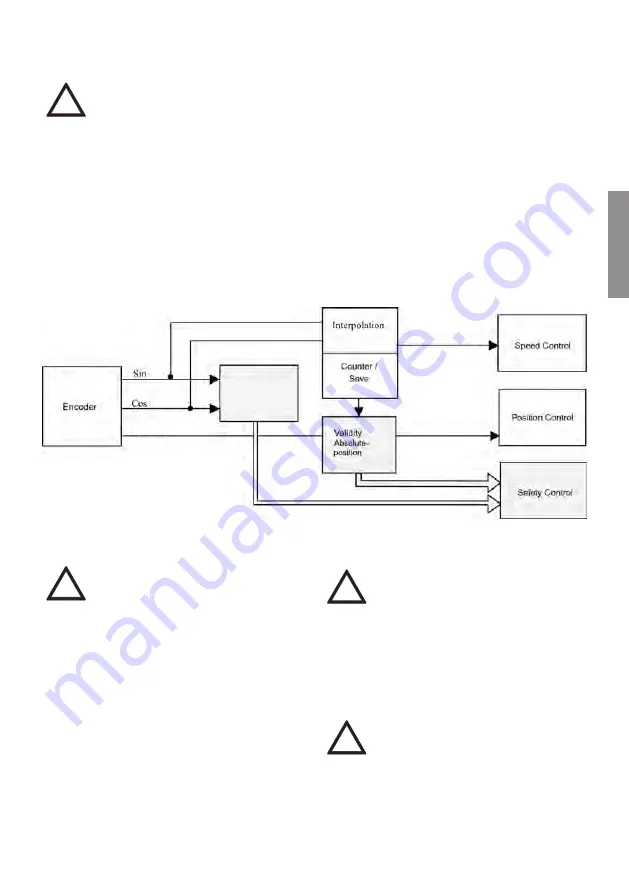
english
5
3.2. Safety Concept
Incremental encoder funcion
In order to achieve safe incremental
information with the encoder, the con-
troller must monitor the validity of the
analogue, 90° phase-shifted
sine/cosine signals with the help of
the function
sin²(x)+cos²(x) = 1.
!
The risk of mechanical faults (as might occur, for
example, if the rigid torque stop with torque pin
were to break or the encoder to fall off the motor
shaft) is eliminated as a result of the mechanical
over-dimensioning of the components of our
safety encoders.
The encoder is safe only when used in conjunc-
tion with a safe controller that can monitor the
functions mentioned.
The encoder does not prevent from switching
the plant on again after a malfunction; if this
function is necessary, it is to be ensured by the
control.
Validity
sin
2
(x)+cos
2
(x)= 1
Absolute
When switching the plant on and off
Prior to the plant being shut down the
absolute position value is saved by
the controller. When the plant is
switched back on, the controller com-
pares the saved value with the newly
measured absolute value that has
been made after power on.
If both these values are identical, then
the position is safe.
If the position values are not identical,
then the position is not safe and the
position must be verified again.
During plant operation
The indicated position is verified by a
comparison of the digital position data
with the sine/cosine signals that are
also constantly being counted and
compared by the controller.
!
!
Safe absolute encoder function
In order to obtain safe information
with the encoder regarding the
absolute position, the controller
counts the incremental pulses and
compares the result with the absolute
positions also provided by the
encoder.
!