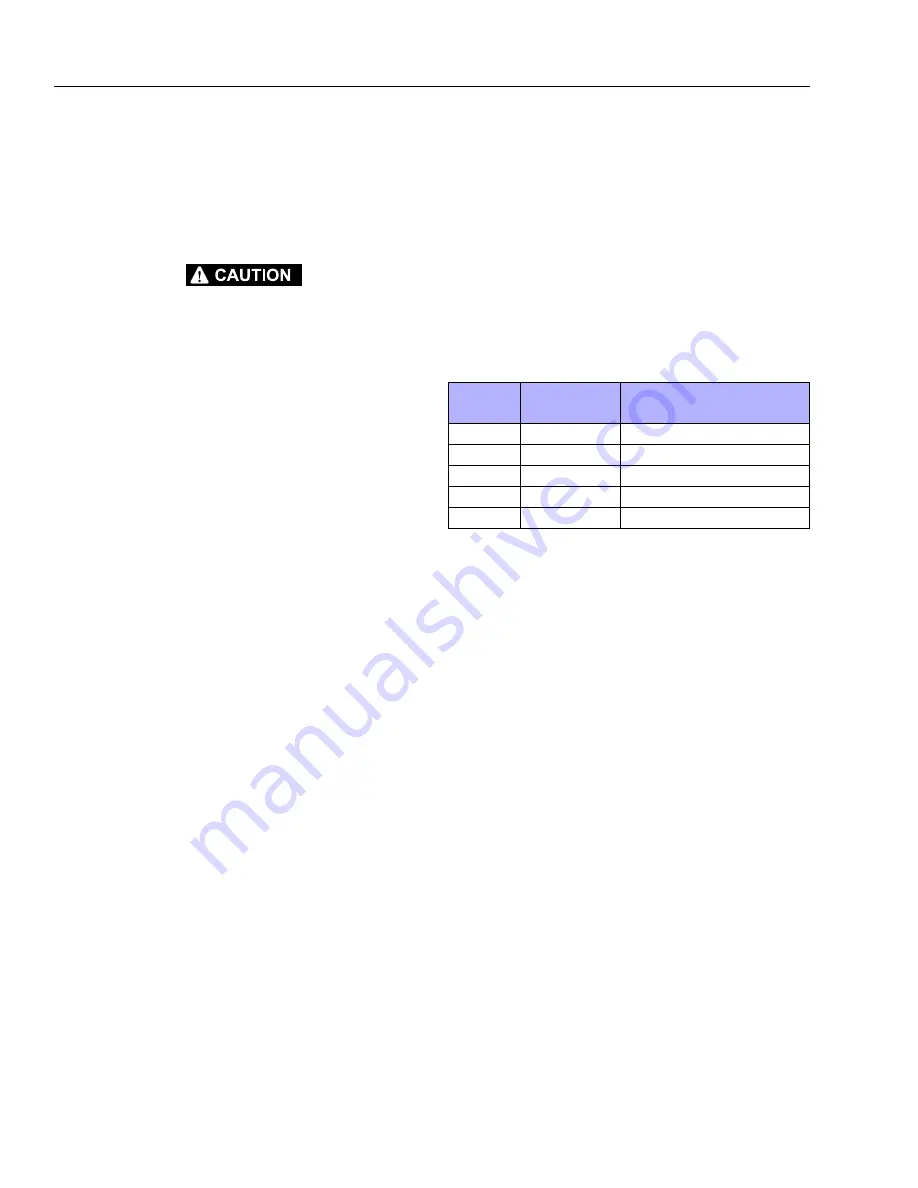
SECTION 3 - CHASSIS & TURNTABLE
3-26
3121234
Housing-Spindle Sub-Assembly
NOTE:
Refer to Figure 3-18., Housing-Spindle Assembly.
NOTE:
Spray a light film of oil on all component parts during
assembly.
SAFETY GLASSES MUST BE WORN DURING THE ENTIRE HOUSING-SPINDLE
SUBASSEMBLY.
1.
Press Bearing Cup (1C), position A, into Housing (1E)
using appropriate pressing tool (See back of manual).
2.
Turn Housing (1E) over and place into pressing base.
Press nine Studs (1H) into Housing (1E).
NOTE:
Use enough pressure to press in studs. Don t use excessively
high pressure to press in studs or Housing may crack. Make
sure head of stud contacts face of flange on Housing.
NOTE:
Spray a generous amount of oil on bearings during instal-
lation.
3.
Press Bearing Cup (1C), position "B", into Housing (1E)
using “B” Bearing Cone pressing tool (see back of man-
ual).
4.
Place Bearing Cone (1D), into Bearing Cup (1C), position
"B".
5.
Grease Seal (1B) lip and press seal into Housing (1E)
using seal pressing tool (see back of manual) until seal is
flush with end of Housing.
6.
Turn Housing (1E) over and lower onto Spindle (1A).
7.
Install Bearing Cone (1D) into Bearing Cup (1C), position
"A". and lightly press on Bearing Cup using the “A” Bear-
ing Cone pressing tool (see back of manual) while rotat-
ing Housing (1E) in both directions to seat bearings.
8.
Place Bearing Spacer (1F) on top of Bearing Cone (1D).
9.
Using retaining ring pliers, install Retaining Ring (1G)
into Spindle (1A) groove. Make sure ring is completely
seated in groove.
NOTE:
Extra bearing pre-load caused by pressing “A” Bearing
Cone (1D) must be removed. This should be done by plac-
ing a flat piece of steel or a pressing tool on the end of the
spindle, and then lightly striking the tool with a piece of
barstock. This should be adequate to remove any addi-
tional bearing pre-load.
DW2B Integral Brake Check
1.
Using appropriate fittings, connect hydraulic line from
hand pump to brake port.
2.
Check to see that brake is set by trying to rotate Input
Shaft (7). This can be accomplished by installing an
appropriate tool (any tool that can locate on the splines
of the Input Coupling (9), such as a mating splined shaft)
into Input Coupling (9).
3.
Bleed brake. Increase hydraulic pressure gradually while
trying to rotate the input until brake just starts to
release. Note this pressure. Make sure the pressure falls
into the appropriate range below.
4.
Increase pressure to 3,000 psi and hold for 30 seconds to
check for leaks. Repair leaks if necessary.
NOTE:
Make sure that brake re-engages when pressure is
released.
NOTE:
When done, make sure Input Coupling (9) is centered in
Spindle (1A) to make installation of motor possible without
release of brake.
BRAKE
CODE
BRAKE P/N
JUST RELEASE
PRESSURE RANGE (psi)
A
902337
185-230
B
902341
155-192
C
902342
125-155
D
902343
93-115
E
902345
132-172
Summary of Contents for 680S
Page 2: ......
Page 52: ...SECTION 2 GENERAL 2 14 3121234 NOTES...
Page 55: ...SECTION 3 CHASSIS TURNTABLE 3121234 3 3 This page left blank intentionally...
Page 89: ...SECTION 3 CHASSIS TURNTABLE 3121234 3 37 Figure 3 28 Assembly Tools Seal Pressing...
Page 139: ...SECTION 3 CHASSIS TURNTABLE 3121234 3 87 Figure 3 62 Swing Hub Prior to SN 0300134352...
Page 143: ...SECTION 3 CHASSIS TURNTABLE 3121234 3 91 Figure 3 64 Swing Brake...
Page 205: ...SECTION 3 CHASSIS TURNTABLE 3121234 3 153 This page left blank intentionally...
Page 208: ...SECTION 3 CHASSIS TURNTABLE 3 156 3121234 Figure 3 91 Generator Electrical Circuit Diagram...
Page 224: ...SECTION 3 CHASSIS TURNTABLE 3 172 3121234 Figure 3 103 EMR 2 Engine Side Equipment...
Page 225: ...SECTION 3 CHASSIS TURNTABLE 3121234 3 173 Figure 3 104 Deutz EMR 2 Troubleshooting Flow Chart...
Page 229: ...SECTION 3 CHASSIS TURNTABLE 3121234 3 177 Figure 3 108 EMR 2 Engine Plug Pin Identification...
Page 230: ...SECTION 3 CHASSIS TURNTABLE 3 178 3121234 Figure 3 109 EMR 2 Vehicle Plug Pin Identification...
Page 231: ...SECTION 3 CHASSIS TURNTABLE 3121234 3 179 Figure 3 110 EMR2 Fault Codes Sheet 1 of 5...
Page 232: ...SECTION 3 CHASSIS TURNTABLE 3 180 3121234 Figure 3 111 EMR2 Fault Codes Sheet 2 of 5...
Page 233: ...SECTION 3 CHASSIS TURNTABLE 3121234 3 181 Figure 3 112 EMR2 Fault Codes Sheet 3 of 5...
Page 234: ...SECTION 3 CHASSIS TURNTABLE 3 182 3121234 Figure 3 113 EMR2 Fault Codes Sheet 4 of 5...
Page 235: ...SECTION 3 CHASSIS TURNTABLE 3121234 3 183 Figure 3 114 EMR2 Fault Codes Sheet 5 of 5...
Page 264: ...SECTION 3 CHASSIS TURNTABLE 3 212 3121234 NOTES...
Page 285: ...SECTION 4 BOOM PLATFORM 3121234 4 21 This page left blank intentionally...
Page 333: ...SECTION 4 BOOM PLATFORM 3121234 4 69 Figure 4 25 Load Sensing Device...
Page 336: ...SECTION 4 BOOM PLATFORM 4 72 3121234 NOTES...
Page 416: ...SECTION 5 BASIC HYDRAULICS INFORMATION SCHEMATICS 5 80 3121234 NOTES...
Page 423: ...SECTION 6 JLG CONTROL SYSTEM 3121234 6 7 Figure 6 2 ADE Block Diagram...
Page 480: ...SECTION 6 JLG CONTROL SYSTEM 6 64 3121234 NOTES...
Page 528: ...SECTION 7 BASIC ELECTRICAL INFORMATION SCHEMATICS 7 48 3121234 NOTES...
Page 529: ......