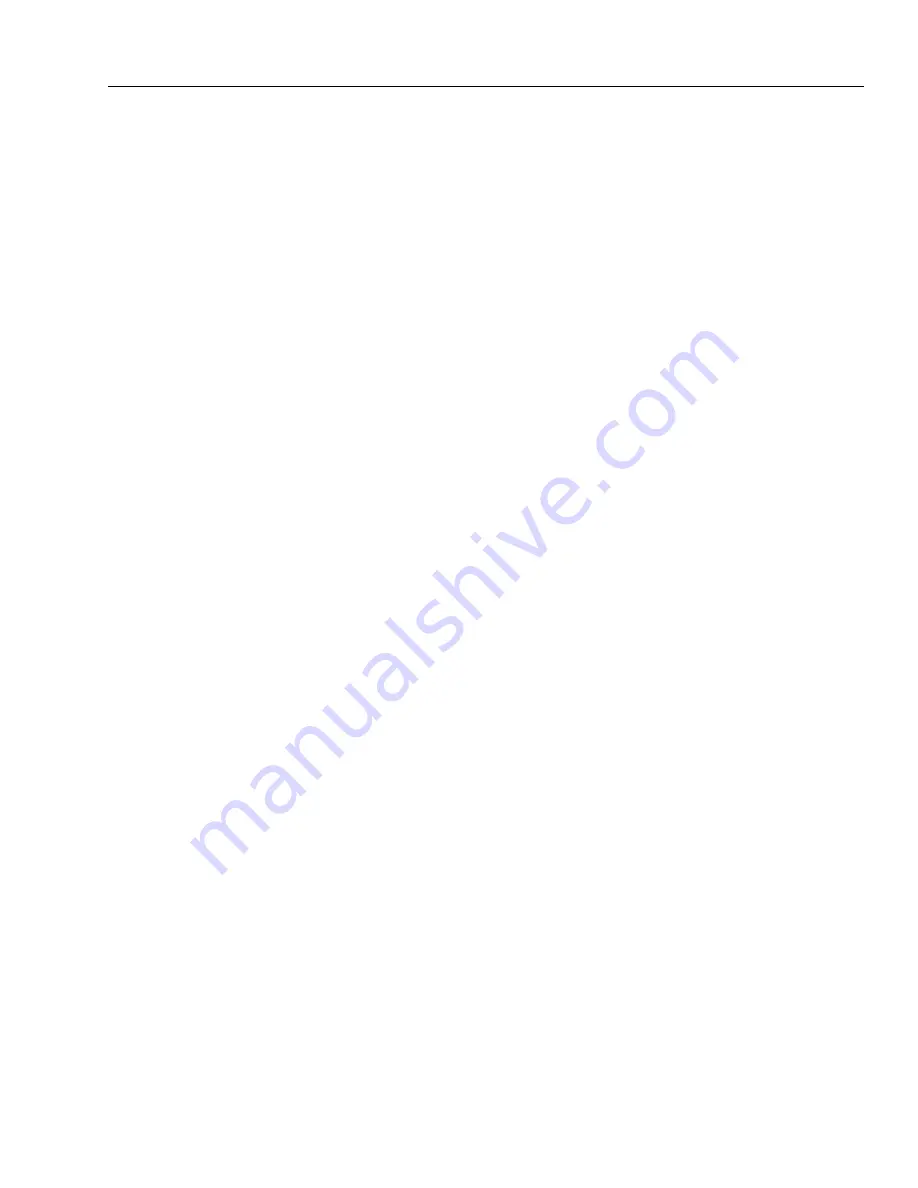
SECTION 5 - BASIC HYDRAULICS INFORMATION & SCHEMATICS
3121234
5-55
DISASSEMBLY
1.
Remove the four screws (C300) holding the control hou-
sing onto the end cap.
2.
Remove the control and discard the three interface o-
rings (C200).
3.
Remove the Pressure Compensator set screw (C102),
Pressure Compensator adjustment screw (C138), o-ring
(C136), springs (C135, C134), and seat (C133). Discard
the o-ring.
4.
Remove the plug (C103), o-ring (C103A),and Pressure
Compensator spool (C132) from the control housing;
discard the o-ring. Note orientation of the spool for reas-
sembly.
5.
Remove the plug (C107) and o-ring (C107A); discard the
o-ring.
NOTE:
For Pressure Compensator only controls, skip steps 6 and 7.
6.
Remove the Load Sense set screw (C102), Load Sense
adjustment screw (C118), o-ring (C116), backup rings
(C117), springs (C114, C115), and seat (C113); discard the
o-ring.
7.
Remove the plug (C106), o-ring (C106A), and Load Sense
spool (C112) from the control housing; discard the o-
ring. Note orientation of the spool for reassembly.
INSPECTION
1.
Inspect the adjustment screws for wear at the tips and
where they contact the springs; replace as necessary.
2.
Inspect the springs and spring guides for wear or dam-
age; replace as necessary.
3.
Carefully inspect the spools. Ensure the sealing lands are
free of nicks and scratches. Check the ends that contact
the spring guides for wear. Replace spools as necessary.
4.
Inspect the control housing for damage. Check the
spool bores for excessive wear.
5.
Clean all parts and lubricate spools, springs, guides and
new o-rings with clean hydraulic fluid.
REASSEMBLY
1.
Install the Pressure Compensator spool, spherical end
first, into the Pressure Compensator bore. The Pressure
Compensator spool is the shorter of the two. Using a
new o-ring, install the plug (C103). Torque to 8-10 ft. lbs.
(11-14 Nm).
2.
Place the two Pressure Compensator springs onto the
spring guide and install into the Pressure Compensator
bore. Place a new o-ring onto the Pressure Compensator
adjustment screw and thread it into the Pressure Com-
pensator bore until flush, then make another full turn.
Install and torque the set screw to 6-8 ft. lbs. (7-11 Nm).
NOTE:
For Pressure Compensator only controls, skip steps 3 and 4.
3.
Install the Load Sense spool, spherical end first, into the
Load Sense bore. The Load Sense spool is the longer of
the two. Using a new o-ring, install the plug (C106).
Torque to 8-10 ft. lbs. (11-14 Nm).
4.
Place the two Load Sense springs onto the spring guide
and install into the Load Sense bore. Place a new o-ring
and backup rings onto the Load Sense adjustment sc-
rew and thread it into the Load Sense bore until flush,
then make another full turn. Install and torque the set
screw to 6-8 ft. lbs. (7-11 Nm).
5.
Using a new o-ring, install the plug (C107). Torque to
8-10 ft. lbs. (11-14 Nm).
6.
Using petroleum jelly to retain them, install the three
interface o-rings (C200) in the recesses on the control
housing.
7.
Install the control assembly onto the endcap using the
four screws (C300). Torque to 11-13 ft. lbs. (15-18 Nm).
Torque screws in a criss-cross pattern and re-torque the
first screw to ensure proper torque retention.
Summary of Contents for 680S
Page 2: ......
Page 52: ...SECTION 2 GENERAL 2 14 3121234 NOTES...
Page 55: ...SECTION 3 CHASSIS TURNTABLE 3121234 3 3 This page left blank intentionally...
Page 89: ...SECTION 3 CHASSIS TURNTABLE 3121234 3 37 Figure 3 28 Assembly Tools Seal Pressing...
Page 139: ...SECTION 3 CHASSIS TURNTABLE 3121234 3 87 Figure 3 62 Swing Hub Prior to SN 0300134352...
Page 143: ...SECTION 3 CHASSIS TURNTABLE 3121234 3 91 Figure 3 64 Swing Brake...
Page 205: ...SECTION 3 CHASSIS TURNTABLE 3121234 3 153 This page left blank intentionally...
Page 208: ...SECTION 3 CHASSIS TURNTABLE 3 156 3121234 Figure 3 91 Generator Electrical Circuit Diagram...
Page 224: ...SECTION 3 CHASSIS TURNTABLE 3 172 3121234 Figure 3 103 EMR 2 Engine Side Equipment...
Page 225: ...SECTION 3 CHASSIS TURNTABLE 3121234 3 173 Figure 3 104 Deutz EMR 2 Troubleshooting Flow Chart...
Page 229: ...SECTION 3 CHASSIS TURNTABLE 3121234 3 177 Figure 3 108 EMR 2 Engine Plug Pin Identification...
Page 230: ...SECTION 3 CHASSIS TURNTABLE 3 178 3121234 Figure 3 109 EMR 2 Vehicle Plug Pin Identification...
Page 231: ...SECTION 3 CHASSIS TURNTABLE 3121234 3 179 Figure 3 110 EMR2 Fault Codes Sheet 1 of 5...
Page 232: ...SECTION 3 CHASSIS TURNTABLE 3 180 3121234 Figure 3 111 EMR2 Fault Codes Sheet 2 of 5...
Page 233: ...SECTION 3 CHASSIS TURNTABLE 3121234 3 181 Figure 3 112 EMR2 Fault Codes Sheet 3 of 5...
Page 234: ...SECTION 3 CHASSIS TURNTABLE 3 182 3121234 Figure 3 113 EMR2 Fault Codes Sheet 4 of 5...
Page 235: ...SECTION 3 CHASSIS TURNTABLE 3121234 3 183 Figure 3 114 EMR2 Fault Codes Sheet 5 of 5...
Page 264: ...SECTION 3 CHASSIS TURNTABLE 3 212 3121234 NOTES...
Page 285: ...SECTION 4 BOOM PLATFORM 3121234 4 21 This page left blank intentionally...
Page 333: ...SECTION 4 BOOM PLATFORM 3121234 4 69 Figure 4 25 Load Sensing Device...
Page 336: ...SECTION 4 BOOM PLATFORM 4 72 3121234 NOTES...
Page 416: ...SECTION 5 BASIC HYDRAULICS INFORMATION SCHEMATICS 5 80 3121234 NOTES...
Page 423: ...SECTION 6 JLG CONTROL SYSTEM 3121234 6 7 Figure 6 2 ADE Block Diagram...
Page 480: ...SECTION 6 JLG CONTROL SYSTEM 6 64 3121234 NOTES...
Page 528: ...SECTION 7 BASIC ELECTRICAL INFORMATION SCHEMATICS 7 48 3121234 NOTES...
Page 529: ......