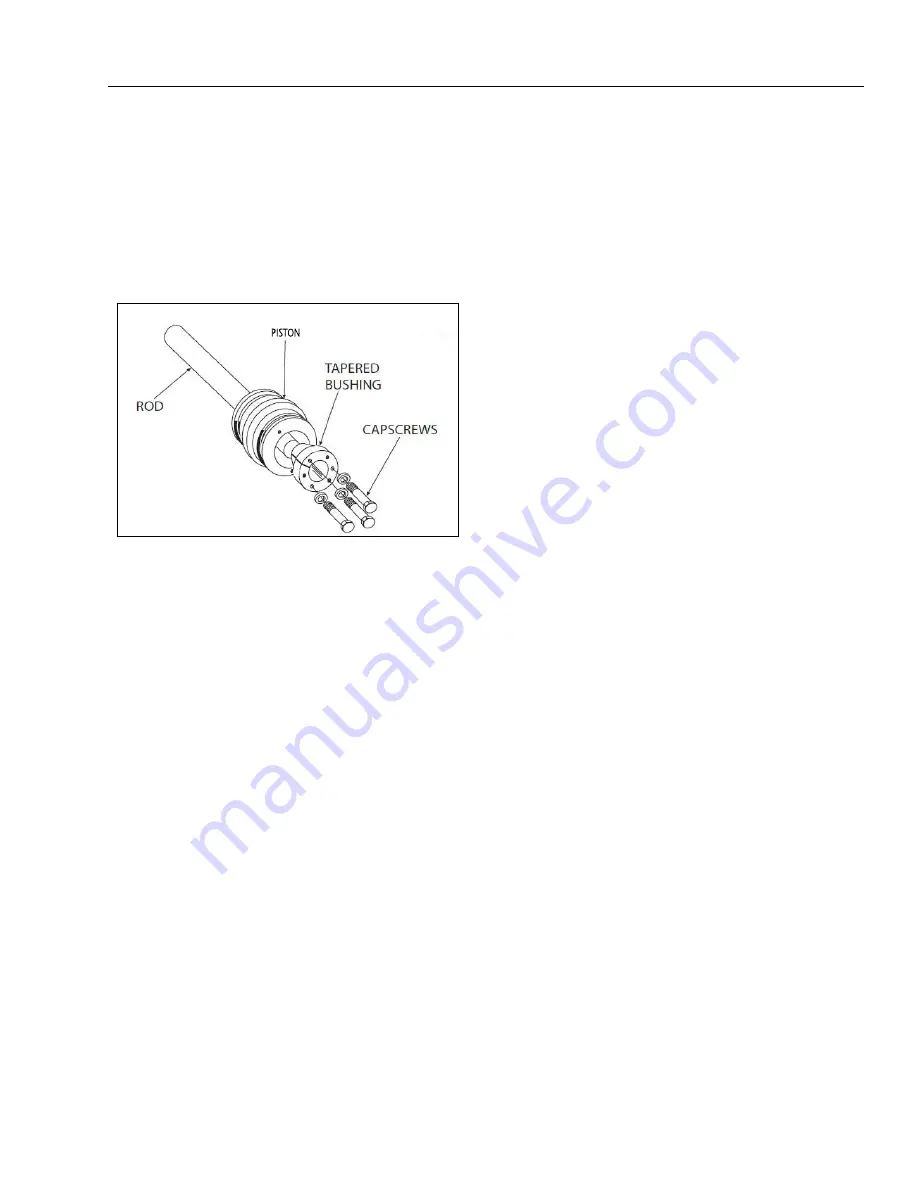
SECTION 5 - BASIC HYDRAULICS INFORMATION & SCHEMATICS
3121234
5-11
8.
Using suitable protection, clamp the cylinder rod in a
vise or similar holding fixture as close to the piston as
possible.
9.
Remove capscrews from drilled holes.
10.
Insert the capscrews in the threaded holes in the outer
piece of the tapered bushing. Progressively tighten the
capscrews until the bushing is loosen on the piston.
11.
Remove the bushing from the piston.
12.
Screw the piston counterclockwise by hand and remove
the piston from cylinder rod.
13.
Remove and discard the piston o-rings, hydrolock seals,
guidelock rings, and backup rings.
14.
Remove setscrew and piston spacer from the rod.
15.
Remove the rod from the holding fixture. Remove the
cylinder head gland. Discard the o-rings, backup rings,
rod seals, wear rings, and wiper seals.
CLEANING AND INSPECTION
1.
Clean all parts thoroughly in an approved cleaning sol-
vent.
2.
Inspect the cylinder rod for scoring, tapering, ovality or
other damage. If necessary, dress rod with Scotch Brite
or equivalent. Replace rod if necessary.
3.
Inspect threaded portion of rod for excessive damage.
Dress threads as necessary.
4.
Inspect inner surface of cylinder barrel tube for scoring
or other damage. Check inside diameter for tapering or
ovality. Replace if necessary.
5.
Inspect piston surface for damage and scoring and for
distortion. Dress piston surface or replace piston as nec-
essary.
6.
Inspect threaded portion of piston for damage. Dress
threads as necessary.
7.
Inspect seal and o-ring grooves in piston for burrs and
sharp edges. Dress applicable surfaces as necessary.
8.
Inspect cylinder head inside diameter for scoring, taper-
ing, ovality or other damage. Replace if necessary.
9.
Inspect seal and o-ring grooves in head for burrs and
sharp edges. Dress applicable surfaces as necessary.
10.
Inspect cylinder head outside diameter for scoring,
tapering, ovality or other damage. Replace if necessary.
11.
If applicable, inspect rod and barrel bearings for signs of
correct excessive wear or damage. Replace if necessary.
a.
Thoroughly clean hole, (steel bushing) of burrs, dirt
etc. to facilitate bearing installation.
b.
Inspect steel bushing for wear or other damage. If
steel bushing is worn or damaged, rod/barrel must
be replaced.
c.
Lubricate inner side of steel bushing prior to bear-
ing installation.
d.
Using an arbor of the correct size, carefully press the
bearing into steel bushing.
Figure 5-19. Tapered Bushing Removal
Summary of Contents for 680S
Page 2: ......
Page 52: ...SECTION 2 GENERAL 2 14 3121234 NOTES...
Page 55: ...SECTION 3 CHASSIS TURNTABLE 3121234 3 3 This page left blank intentionally...
Page 89: ...SECTION 3 CHASSIS TURNTABLE 3121234 3 37 Figure 3 28 Assembly Tools Seal Pressing...
Page 139: ...SECTION 3 CHASSIS TURNTABLE 3121234 3 87 Figure 3 62 Swing Hub Prior to SN 0300134352...
Page 143: ...SECTION 3 CHASSIS TURNTABLE 3121234 3 91 Figure 3 64 Swing Brake...
Page 205: ...SECTION 3 CHASSIS TURNTABLE 3121234 3 153 This page left blank intentionally...
Page 208: ...SECTION 3 CHASSIS TURNTABLE 3 156 3121234 Figure 3 91 Generator Electrical Circuit Diagram...
Page 224: ...SECTION 3 CHASSIS TURNTABLE 3 172 3121234 Figure 3 103 EMR 2 Engine Side Equipment...
Page 225: ...SECTION 3 CHASSIS TURNTABLE 3121234 3 173 Figure 3 104 Deutz EMR 2 Troubleshooting Flow Chart...
Page 229: ...SECTION 3 CHASSIS TURNTABLE 3121234 3 177 Figure 3 108 EMR 2 Engine Plug Pin Identification...
Page 230: ...SECTION 3 CHASSIS TURNTABLE 3 178 3121234 Figure 3 109 EMR 2 Vehicle Plug Pin Identification...
Page 231: ...SECTION 3 CHASSIS TURNTABLE 3121234 3 179 Figure 3 110 EMR2 Fault Codes Sheet 1 of 5...
Page 232: ...SECTION 3 CHASSIS TURNTABLE 3 180 3121234 Figure 3 111 EMR2 Fault Codes Sheet 2 of 5...
Page 233: ...SECTION 3 CHASSIS TURNTABLE 3121234 3 181 Figure 3 112 EMR2 Fault Codes Sheet 3 of 5...
Page 234: ...SECTION 3 CHASSIS TURNTABLE 3 182 3121234 Figure 3 113 EMR2 Fault Codes Sheet 4 of 5...
Page 235: ...SECTION 3 CHASSIS TURNTABLE 3121234 3 183 Figure 3 114 EMR2 Fault Codes Sheet 5 of 5...
Page 264: ...SECTION 3 CHASSIS TURNTABLE 3 212 3121234 NOTES...
Page 285: ...SECTION 4 BOOM PLATFORM 3121234 4 21 This page left blank intentionally...
Page 333: ...SECTION 4 BOOM PLATFORM 3121234 4 69 Figure 4 25 Load Sensing Device...
Page 336: ...SECTION 4 BOOM PLATFORM 4 72 3121234 NOTES...
Page 416: ...SECTION 5 BASIC HYDRAULICS INFORMATION SCHEMATICS 5 80 3121234 NOTES...
Page 423: ...SECTION 6 JLG CONTROL SYSTEM 3121234 6 7 Figure 6 2 ADE Block Diagram...
Page 480: ...SECTION 6 JLG CONTROL SYSTEM 6 64 3121234 NOTES...
Page 528: ...SECTION 7 BASIC ELECTRICAL INFORMATION SCHEMATICS 7 48 3121234 NOTES...
Page 529: ......