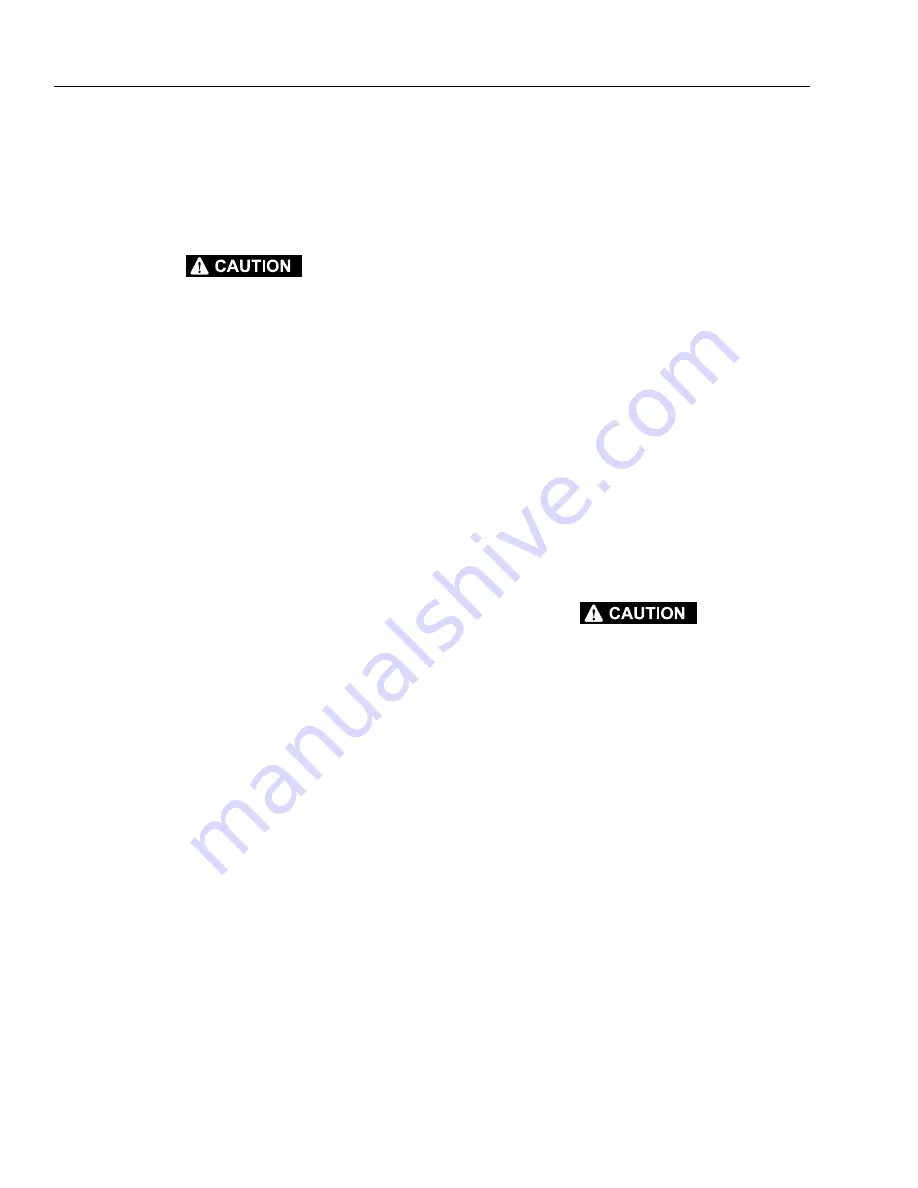
SECTION 3 - CHASSIS & TURNTABLE
3-90
3121234
3.16 SWING DRIVE BRAKE
Disassembly
1.
Remove pressure plate (3) from cover plate (16) by
removing capscrews (1) and washers (2).
PRESSURE PLATE IS UNDER SPRING TENSION OF APPROXIMATELY 2000 LBS
(907 KGF ). THE TWO CAPSCREWS MUST BE LOOSENED EVENLY TO RELIEVE
THIS FORCE. IF A HYDRAULIC PRESS IS AVAILABLE, 3000 LBS (1361 KGF) MIN-
IMUM, THE PRESSURE PLATE CAN BE HELD IN POSITION WHILE REMOVING
THE CAPSCREWS. COVER PLATE (16) MUST BE SUPPORTED AS SHOWN IN FIG-
URE 3-37.
2.
Remove case seal (4) from cover plate (16).
3.
Remove piston (6) from pressure plate (2).
4.
Remove o-ring (4), back-up ring (5), o-ring (7) and back-
up ring (8) from piston (6).
5.
Remove stack assembly, consisting of stator disc (10),
rotor disc (11) and return plate (12) from cover (16).
6.
Remove dowel pins (15), springs (13) and spring retainer
(14) from cover (16).
NOTE:
Not all models use the same number of springs or spring
pattern. Record this information for assembly purposes.
7.
Remove retaining ring (19) from cover (16).
8.
Remove shaft by pressing or using a soft mallet on the
male end of the shaft (9).
9.
Remove retaining ring (20) from cover (16) and press out
oil seal (17) and bearing (18) if required.
Assembly
NOTE:
Lubricate all rubber components from repair kit with clean
type fluid used in the system.
1.
Use an alkaline wash to clean parts before assembly.
2.
Press oil seal (17) into cover plate (16) until it is flush with
bearing shoulder. Note direction of seal.
3.
Press bearing (18) into position until it bottoms out on
borestep.
4.
Install retaining ring (20) in cover plate (16).
5.
Press shaft (9) into bearing (18) until it bottoms on the
shoulder. Bearing (18) inner race must be supported
during this operation.
6.
Install retaining ring (19) on shaft (10).
7.
Insert dowel pins (15), spring retainer (14) and springs
(13) in cover (16).
NOTE:
Be sure to use the same number of springs and the same
spring pattern as recorded during disassembly.
8.
Position plate (12) on spring (13).
NOTE:
Discs (11 & 12) and return plate (13) must remain dry
during installation. No oil residue must be allowed to con-
taminate disc surfaces.
9.
Install rotor disc (11) and stator disc (10).
10.
Install o-ring (4), back-up ring (5), o-ring (7) and back-up
ring (8)on piston (6). Note order of o-rings and back-up
rings. Insert piston (6) into pressure plate (2).
NOTE:
Be careful not to shear o-rings or backup rings. Be careful
not to scratch or mar piston.
11.
Install new case seal (3) in cover plate (16).
12.
Position pressure plate (2) on cover plate (16) aligning
dowel pins (15) with holes in pressure plate.
13.
Install washer head cap screws (1) and tighten evenly to
draw pressure plate (2) to cover (16). Torque washer
head cap screws 55 ft. lbs. (74.6 Nm).
NOTE:
A hydraulic press will simplify installation of pressure plate
on cover. Clamp pressure plate in position while
tighten¦ing the capscrews. Cover plate (16) must be sup-
ported as indicated in Figure 3-37.
IF HYDROSTATIC BENCH TESTING IS PERFORMED ON THE BRAKE ASSEMBLY,
RELEASE PRESSURE MUST NOT EXCEED 137.9 BARS (2000 PSI) UNLESS TWO
ADDITIONAL BOLTS ARE USED FOR SUPPLEMENTAL CLAMPING.
Summary of Contents for 680S
Page 2: ......
Page 52: ...SECTION 2 GENERAL 2 14 3121234 NOTES...
Page 55: ...SECTION 3 CHASSIS TURNTABLE 3121234 3 3 This page left blank intentionally...
Page 89: ...SECTION 3 CHASSIS TURNTABLE 3121234 3 37 Figure 3 28 Assembly Tools Seal Pressing...
Page 139: ...SECTION 3 CHASSIS TURNTABLE 3121234 3 87 Figure 3 62 Swing Hub Prior to SN 0300134352...
Page 143: ...SECTION 3 CHASSIS TURNTABLE 3121234 3 91 Figure 3 64 Swing Brake...
Page 205: ...SECTION 3 CHASSIS TURNTABLE 3121234 3 153 This page left blank intentionally...
Page 208: ...SECTION 3 CHASSIS TURNTABLE 3 156 3121234 Figure 3 91 Generator Electrical Circuit Diagram...
Page 224: ...SECTION 3 CHASSIS TURNTABLE 3 172 3121234 Figure 3 103 EMR 2 Engine Side Equipment...
Page 225: ...SECTION 3 CHASSIS TURNTABLE 3121234 3 173 Figure 3 104 Deutz EMR 2 Troubleshooting Flow Chart...
Page 229: ...SECTION 3 CHASSIS TURNTABLE 3121234 3 177 Figure 3 108 EMR 2 Engine Plug Pin Identification...
Page 230: ...SECTION 3 CHASSIS TURNTABLE 3 178 3121234 Figure 3 109 EMR 2 Vehicle Plug Pin Identification...
Page 231: ...SECTION 3 CHASSIS TURNTABLE 3121234 3 179 Figure 3 110 EMR2 Fault Codes Sheet 1 of 5...
Page 232: ...SECTION 3 CHASSIS TURNTABLE 3 180 3121234 Figure 3 111 EMR2 Fault Codes Sheet 2 of 5...
Page 233: ...SECTION 3 CHASSIS TURNTABLE 3121234 3 181 Figure 3 112 EMR2 Fault Codes Sheet 3 of 5...
Page 234: ...SECTION 3 CHASSIS TURNTABLE 3 182 3121234 Figure 3 113 EMR2 Fault Codes Sheet 4 of 5...
Page 235: ...SECTION 3 CHASSIS TURNTABLE 3121234 3 183 Figure 3 114 EMR2 Fault Codes Sheet 5 of 5...
Page 264: ...SECTION 3 CHASSIS TURNTABLE 3 212 3121234 NOTES...
Page 285: ...SECTION 4 BOOM PLATFORM 3121234 4 21 This page left blank intentionally...
Page 333: ...SECTION 4 BOOM PLATFORM 3121234 4 69 Figure 4 25 Load Sensing Device...
Page 336: ...SECTION 4 BOOM PLATFORM 4 72 3121234 NOTES...
Page 416: ...SECTION 5 BASIC HYDRAULICS INFORMATION SCHEMATICS 5 80 3121234 NOTES...
Page 423: ...SECTION 6 JLG CONTROL SYSTEM 3121234 6 7 Figure 6 2 ADE Block Diagram...
Page 480: ...SECTION 6 JLG CONTROL SYSTEM 6 64 3121234 NOTES...
Page 528: ...SECTION 7 BASIC ELECTRICAL INFORMATION SCHEMATICS 7 48 3121234 NOTES...
Page 529: ......