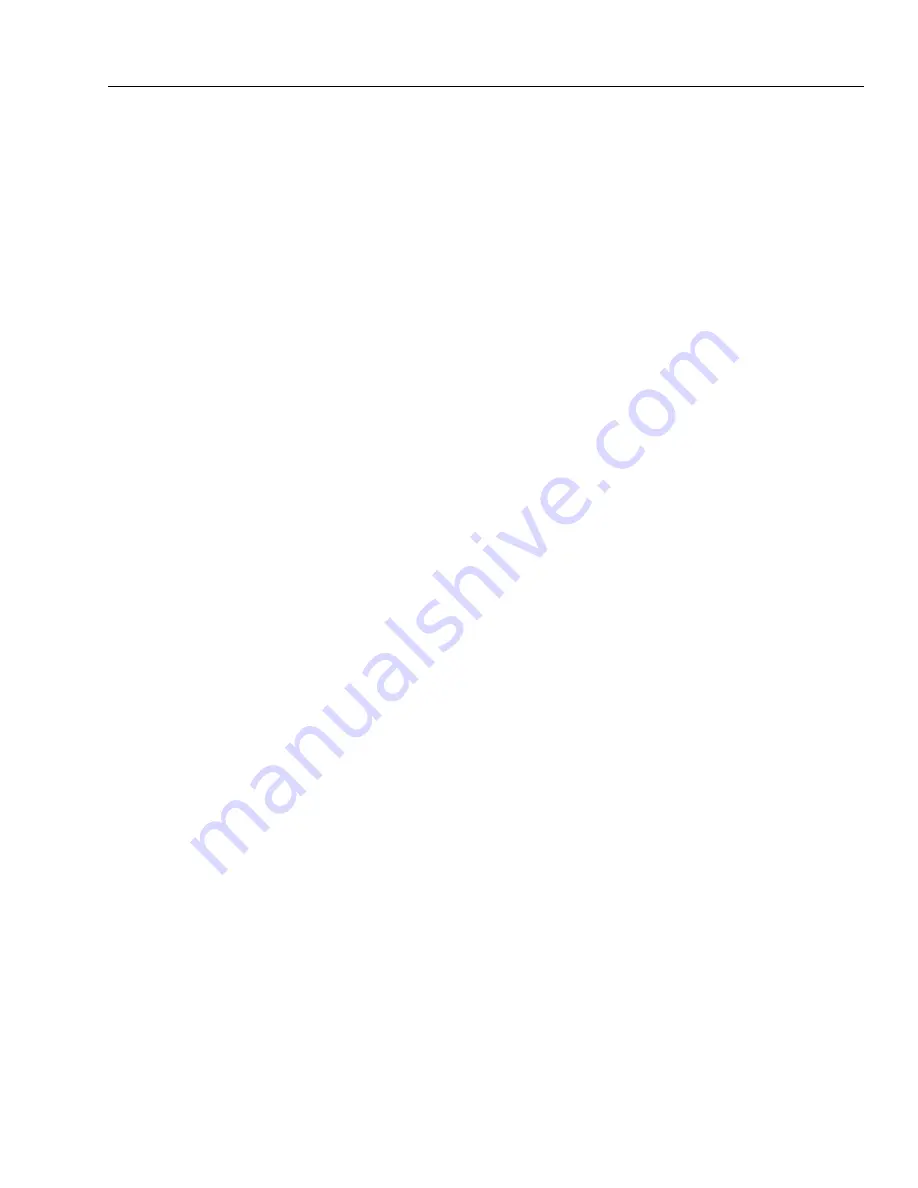
SECTION 4 - BOOM & PLATFORM
3121234
4-49
STEP 4: CALIBRATING THE PLATFORM LEVEL UP AND DOWN
VALVE CRACKPOINTS
NOTE:
Since the valve position which allows minimum oil flow
(crackpoint) is dependent on the oil pressure, verify the
proper stand-by pressure as outlined in Section 5.3 prior to
setting the crackpoints.
1.
Put machine into “Ground Mode”.
2.
Start machine and plug in Analyzer.
3.
Go to the “Access Level 2” screen.
4.
Enter “33271” to get into Access Level 1 mode.
5.
Go to the “Calibrations” menu and hit ENTER.
6.
Go to the “Basket U Crkpt” Screen. Hit ENTER.
7.
“Calibrate?” prompt should appear. Hit ENTER again.
8.
The engine will rise to 1800 rpm.
9.
Using UP ARROW, increase the value until you see the
basket up movement. (Typically from 275 – 425).
10.
Hit ENTER again. “Cal Complete” message should appear
11.
Engine should again return to idle.
12.
Hit ESC should return to “Basket U Crkpt” screen.
13.
Hit RIGHT ARROW to get to the “Basket D Crkpt” screen.
Hit ENTER.
14.
“Calibrate?” prompt should appear. Hit ENTER again.
15.
The engine will rise to 1800 rpm.
16.
Using UP ARROW, increase the value until you see the
basket down movement. (Typically from 275 – 425).
17.
Hit ENTER again. “Cal Complete” message should
appear.
18.
Engine should again return to idle.
19.
Hit ESC to exit.
20.
Cycle power to the machine.
21.
The preceding steps will provide acceptable crackpoint
settings for the majority of machines. However, if the
operator can feel small jolts in the platform from the
valve opening during a leveling operation, the crack-
point is likely too high for this machine. A high crack-
point may also lead to “over-leveling”, causing the
platform to drift beyond the set point. An example of
this would be the platform tilting too far backwards
during a Lift Up operation. Therefore, use the following
guidelines to evaluate whether further crackpoint
adjustment is required.
a.
Telescope the machine halfway.
b.
Perform Lift Up. If the basket leans backward (over
compensates), the Level Down crackpoint is too
high. If the basket leans forward or a BASKET LEVEL-
ING SYSTEM TIMEOUT fault occurs, the Level Down
crackpoint is too low.
c.
Perform Lift Down. If the basket leans forward (over
compensates), the Level Up crackpoint is too high. If
the basket leans backwards or the Tilt Cutout Alarm
comes on, the Level Up crackpoint is too low.
22.
If Platform Level is slow to respond during Lift com-
mands, causing PLATFORM LEVEL TIMED OUT faults, it
may be necessary to increase the crackpoint settings.
Use the following guidelines to evaluate whether fur-
ther crackpoint adjustment is required.
a.
Perform a continued Lift Up command (do not cycle
the joystick on/off repeatedly). If the PLATFORM
LEVEL TIMED OUT fault sets or if Platform Level
Down seems slow to respond, an increase in the
Platform Level Down crackpoint may be necessary.
b.
Perform a continued Lift Down command (do not
cycle the joystick on/off repeatedly). If the PLAT-
FORM LEVEL TIMED OUT fault sets or if Platform
Level Up seems slow to respond an increase in the
Platform Level Up crackpoint may be necessary.
Summary of Contents for 680S
Page 2: ......
Page 52: ...SECTION 2 GENERAL 2 14 3121234 NOTES...
Page 55: ...SECTION 3 CHASSIS TURNTABLE 3121234 3 3 This page left blank intentionally...
Page 89: ...SECTION 3 CHASSIS TURNTABLE 3121234 3 37 Figure 3 28 Assembly Tools Seal Pressing...
Page 139: ...SECTION 3 CHASSIS TURNTABLE 3121234 3 87 Figure 3 62 Swing Hub Prior to SN 0300134352...
Page 143: ...SECTION 3 CHASSIS TURNTABLE 3121234 3 91 Figure 3 64 Swing Brake...
Page 205: ...SECTION 3 CHASSIS TURNTABLE 3121234 3 153 This page left blank intentionally...
Page 208: ...SECTION 3 CHASSIS TURNTABLE 3 156 3121234 Figure 3 91 Generator Electrical Circuit Diagram...
Page 224: ...SECTION 3 CHASSIS TURNTABLE 3 172 3121234 Figure 3 103 EMR 2 Engine Side Equipment...
Page 225: ...SECTION 3 CHASSIS TURNTABLE 3121234 3 173 Figure 3 104 Deutz EMR 2 Troubleshooting Flow Chart...
Page 229: ...SECTION 3 CHASSIS TURNTABLE 3121234 3 177 Figure 3 108 EMR 2 Engine Plug Pin Identification...
Page 230: ...SECTION 3 CHASSIS TURNTABLE 3 178 3121234 Figure 3 109 EMR 2 Vehicle Plug Pin Identification...
Page 231: ...SECTION 3 CHASSIS TURNTABLE 3121234 3 179 Figure 3 110 EMR2 Fault Codes Sheet 1 of 5...
Page 232: ...SECTION 3 CHASSIS TURNTABLE 3 180 3121234 Figure 3 111 EMR2 Fault Codes Sheet 2 of 5...
Page 233: ...SECTION 3 CHASSIS TURNTABLE 3121234 3 181 Figure 3 112 EMR2 Fault Codes Sheet 3 of 5...
Page 234: ...SECTION 3 CHASSIS TURNTABLE 3 182 3121234 Figure 3 113 EMR2 Fault Codes Sheet 4 of 5...
Page 235: ...SECTION 3 CHASSIS TURNTABLE 3121234 3 183 Figure 3 114 EMR2 Fault Codes Sheet 5 of 5...
Page 264: ...SECTION 3 CHASSIS TURNTABLE 3 212 3121234 NOTES...
Page 285: ...SECTION 4 BOOM PLATFORM 3121234 4 21 This page left blank intentionally...
Page 333: ...SECTION 4 BOOM PLATFORM 3121234 4 69 Figure 4 25 Load Sensing Device...
Page 336: ...SECTION 4 BOOM PLATFORM 4 72 3121234 NOTES...
Page 416: ...SECTION 5 BASIC HYDRAULICS INFORMATION SCHEMATICS 5 80 3121234 NOTES...
Page 423: ...SECTION 6 JLG CONTROL SYSTEM 3121234 6 7 Figure 6 2 ADE Block Diagram...
Page 480: ...SECTION 6 JLG CONTROL SYSTEM 6 64 3121234 NOTES...
Page 528: ...SECTION 7 BASIC ELECTRICAL INFORMATION SCHEMATICS 7 48 3121234 NOTES...
Page 529: ......