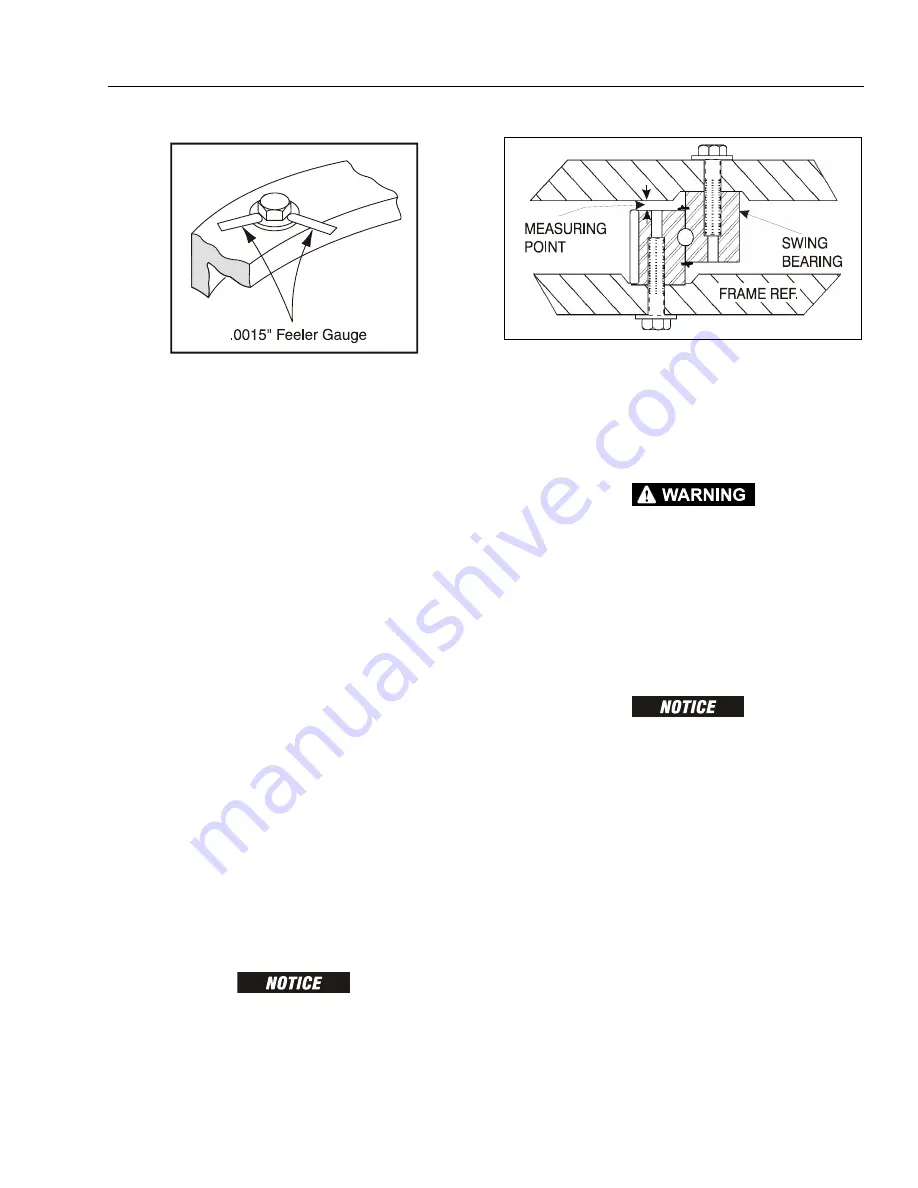
SECTION 3 - CHASSIS & TURNTABLE
3121234
3-139
Wear Tolerance
1.
From the underside of the machine, at rear center, with
the main boom fully elevated and fully retracted, as
shown in Figure 3-75., Swing Bearing Tolerance Boom
Placement - Sheet 1 of 2, using a magnetic base dial
indicator, measure and record the distance between the
swing bearing and turntable. See Figure 3-79., Swing
Bearing Tolerance Measuring Point.
2.
At the same point, with the main boom at horizontal
and fully extended, as shown in Figure 3-76., Swing
Bearing Tolerance Boom Placement - Sheet 2 of 2. Using
a magnetic base dial indicator, measure and record the
distance between the swing bearing and turntable. See
Figure 3-79., Swing Bearing Tolerance Measuring Point.
3.
If a difference greater than 0.079 in. (2.00 mm) is deter-
mined, the swing bearing should be replaced.
4.
If a difference less than 0.079 in. (2.00 mm) is deter-
mined, and any of the following conditions exist, the
bearing should be removed, disassembled, and
inspected for the following:
a.
Metal particles in the grease.
b.
Increased drive power required.
c.
Noise.
d.
Rough rotation.
5.
If bearing inspection shows no defects, reassemble and
return to service.
THE SWING BEARING IS ONE OF THE MOST CRITICAL POINTS ON AN AERIAL
LIFT. IT IS HERE THAT THE STRESSES OF LIFTING ARE CONCENTRATED, AT THE
CENTER OF ROTATION. BECAUSE OF THIS, PROPER MAINTENANCE OF THE
SWING BEARING BOLTS IS A MUST FOR SAFE OPERATION.
Swing Bearing Removal
1.
From Ground Control station, operate the boom ade-
quately to provide access to frame opening to rotary
coupling.
NEVER WORK BENEATH THE BOOM WITHOUT FIRST ENGAGING BOOM SAFETY
PROP OR PROVIDING ADEQUATE OVERHEAD SLING SUPPORT AND/OR BLOCK-
ING.
2.
Attach an adequate support sling to the boom and draw
all slack from sling. Prop or block the boom if feasible.
3.
From inside turntable, remove mounting hardware
which attach rotary coupling retaining yoke brackets to
turntable.
HYDRAULIC LINES AND PORTS SHOULD BE CAPPED IMMEDIATELY AFTER DIS-
CONNECTING LINES TO AVOID THE ENTRY OF CONTAMINANTS INTO THE SYS-
TEM.
4.
Tag and disconnect the hydraulic lines from the fittings
on the top of the rotary coupling. Use a suitable con-
tainer to retain any residual hydraulic fluid. Immediately
cap lines and ports.
5.
Attach suitable overhead lifting equipment to the base
of the turntable weldment.
6.
Use a suitable tool to scribe a line on the inner race of
the swing bearing and on the underside of the turnta-
ble. This will aid in aligning the bearing upon installa-
tion. Remove the bolts and washers which attach the
turntable to the bearing inner race. Discard the bolts.
7.
Use the lifting equipment to carefully lift the complete
turntable assembly from the bearing. Ensure that no
damage occurs to the turntable, bearing or frame-
mounted components.
Figure 3-78. Swing Bolt Feeler Gauge Check.
Figure 3-79. Swing Bearing Tolerance Measuring Point.
Summary of Contents for 680S
Page 2: ......
Page 52: ...SECTION 2 GENERAL 2 14 3121234 NOTES...
Page 55: ...SECTION 3 CHASSIS TURNTABLE 3121234 3 3 This page left blank intentionally...
Page 89: ...SECTION 3 CHASSIS TURNTABLE 3121234 3 37 Figure 3 28 Assembly Tools Seal Pressing...
Page 139: ...SECTION 3 CHASSIS TURNTABLE 3121234 3 87 Figure 3 62 Swing Hub Prior to SN 0300134352...
Page 143: ...SECTION 3 CHASSIS TURNTABLE 3121234 3 91 Figure 3 64 Swing Brake...
Page 205: ...SECTION 3 CHASSIS TURNTABLE 3121234 3 153 This page left blank intentionally...
Page 208: ...SECTION 3 CHASSIS TURNTABLE 3 156 3121234 Figure 3 91 Generator Electrical Circuit Diagram...
Page 224: ...SECTION 3 CHASSIS TURNTABLE 3 172 3121234 Figure 3 103 EMR 2 Engine Side Equipment...
Page 225: ...SECTION 3 CHASSIS TURNTABLE 3121234 3 173 Figure 3 104 Deutz EMR 2 Troubleshooting Flow Chart...
Page 229: ...SECTION 3 CHASSIS TURNTABLE 3121234 3 177 Figure 3 108 EMR 2 Engine Plug Pin Identification...
Page 230: ...SECTION 3 CHASSIS TURNTABLE 3 178 3121234 Figure 3 109 EMR 2 Vehicle Plug Pin Identification...
Page 231: ...SECTION 3 CHASSIS TURNTABLE 3121234 3 179 Figure 3 110 EMR2 Fault Codes Sheet 1 of 5...
Page 232: ...SECTION 3 CHASSIS TURNTABLE 3 180 3121234 Figure 3 111 EMR2 Fault Codes Sheet 2 of 5...
Page 233: ...SECTION 3 CHASSIS TURNTABLE 3121234 3 181 Figure 3 112 EMR2 Fault Codes Sheet 3 of 5...
Page 234: ...SECTION 3 CHASSIS TURNTABLE 3 182 3121234 Figure 3 113 EMR2 Fault Codes Sheet 4 of 5...
Page 235: ...SECTION 3 CHASSIS TURNTABLE 3121234 3 183 Figure 3 114 EMR2 Fault Codes Sheet 5 of 5...
Page 264: ...SECTION 3 CHASSIS TURNTABLE 3 212 3121234 NOTES...
Page 285: ...SECTION 4 BOOM PLATFORM 3121234 4 21 This page left blank intentionally...
Page 333: ...SECTION 4 BOOM PLATFORM 3121234 4 69 Figure 4 25 Load Sensing Device...
Page 336: ...SECTION 4 BOOM PLATFORM 4 72 3121234 NOTES...
Page 416: ...SECTION 5 BASIC HYDRAULICS INFORMATION SCHEMATICS 5 80 3121234 NOTES...
Page 423: ...SECTION 6 JLG CONTROL SYSTEM 3121234 6 7 Figure 6 2 ADE Block Diagram...
Page 480: ...SECTION 6 JLG CONTROL SYSTEM 6 64 3121234 NOTES...
Page 528: ...SECTION 7 BASIC ELECTRICAL INFORMATION SCHEMATICS 7 48 3121234 NOTES...
Page 529: ......