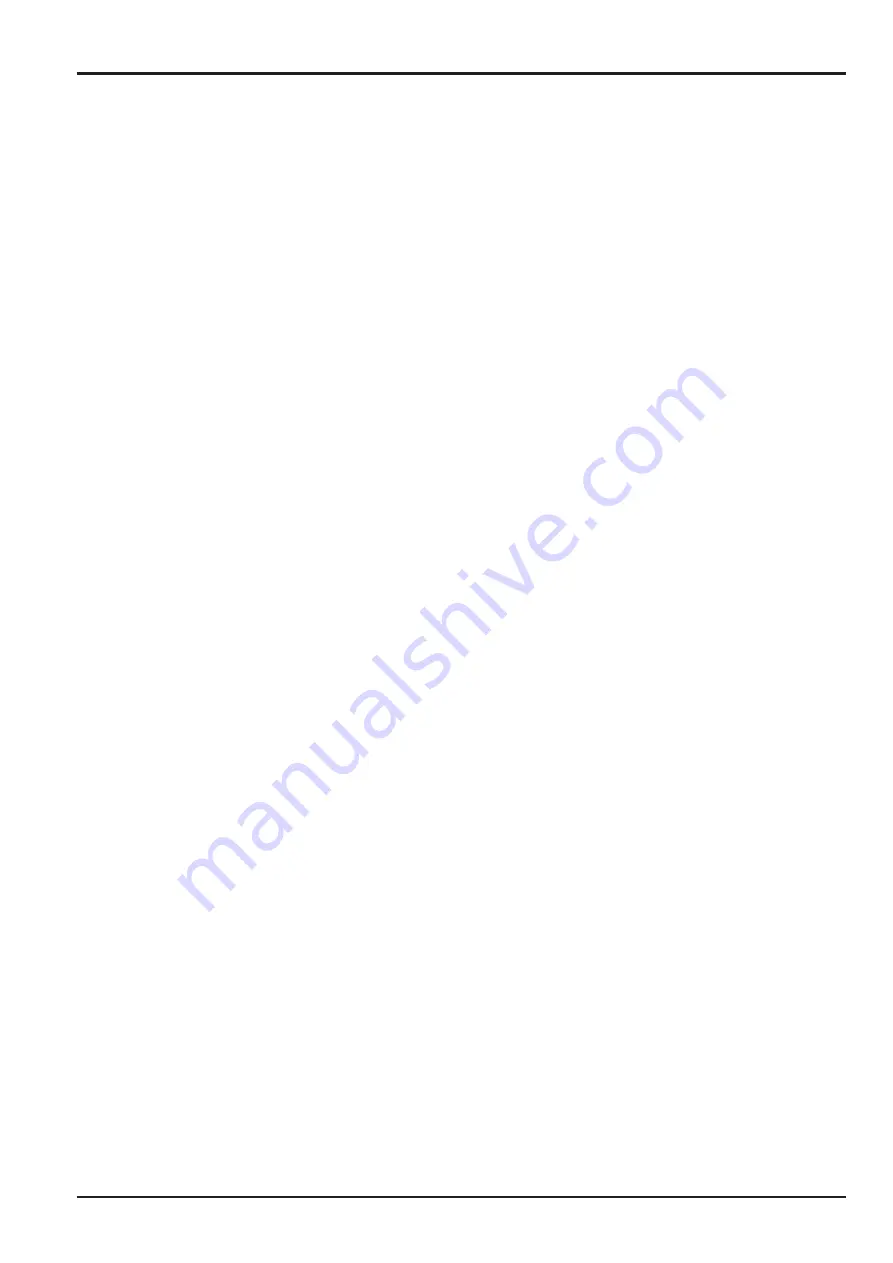
90 - 3
Section E
Hydraulics
9803/6400
Section E
90 - 3
Issue 2*
Slew Motor
Operation
(continued)
Relief Valve Working Principles
1
On starting
Due to the superstructure’s inertia there is a build-up of
pressure in the motor when it begins to slew. To prevent
damage, excess pressure is diverted between ports
A
and
B
via poppet valves
43
(part of cross-line relief
valve
J
).
2
When the brake is applied (cushioning)
When the slew control valve is returned to neutral the oil
return path from the motor is closed. While the
superstructure is coming to a halt it is, in effect, ‘driving’
the motor as a pump. This results in a pressure build-up
at the outlet port (
A
or
B
depending on slew direction).
This increased pressure opens poppet valve
43
, which
allows oil to flow via paths
g
and
h
, opening check valve
29
and relieving the pressure into cavity
C
.
At the same time, oil flows between the two ports via the
cross-line relief valve
J
, which has already been partially
opened by poppet valve
43
.
The result is a 2-stage relief action which momentarily
delays the pressure build-up as the superstructure
comes to a halt. This reduces the shocks arising due to
sudden braking.
3
Anti-Pendulum Feature
While the superstructure is coming to a halt, as
described in
2
, it drives the motor as a pump. The initial
result is a braking effect on the superstructure. However,
the resulting pressure build-up in port
A
(or
B
, depending
on direction) tends to cause the superstructure to
‘bounce back’ a little. The process repeats itself to create
what is known as a ‘pendulum effect’.
To prevent this happening, check valves
50
and flow
control valves
48
work together to divert oil pressure
between ports
A
and
B
until the superstructure has come
to a halt.
Reduction Gear Structure and Working
Principles
(illustration reference page 83 - 2)
Power transmitted by the hydraulic motor output shaft is
transmitted to second sun gear
77
via first sun gear
66
,
planetary gear
69
and holder
65
. Power is then transmitted to
output shaft
53
via second sun gear
77
, planetary gear
72
and holder
76
. The output shaft is constructed with an
integral pinion and is supported in gear case
58
by bearings
57
and
62
.
Due to the severe conditions under which the output shaft
operates, an oil seal
61
is provided in the centre of gear case
58
to protect the bearings from metal waste worn from the
gears. The bearing in chamber
A
is lubricated with gear oil
and the bearing in chamber
B
with grease.
*
Summary of Contents for JS 200 Series
Page 57: ...9 1 Section 3 Routine Maintenance 9803 6400 Section 3 9 1 Issue 2 Component Location Diagram...
Page 113: ......
Page 137: ...5 3 Section C Electrics 9803 6400 Section C 5 3 Issue 2 Pump Control FLOW CHART...
Page 201: ...10 7 Section C Electrics 9803 6400 Section C 10 7 Issue 1 CAPs II Diagnostic system K C...
Page 215: ...Section E Section E Hydraulics 9803 6400 Issue 2 3 2 3 2 Schematics...
Page 217: ...Section E Section E 9803 6400 Issue 2 3 3 3 3 Hydraulics Schematics...
Page 218: ...3 5 Section E Hydraulics 9803 6400 Section E 3 5 Issue 1 Schematics Shuttle Block JS200 JS240...
Page 232: ...10 1 Section E Hydraulics 9803 6400 Section E 10 1 Issue 1 Hydraulic Pump JS200 JS240...
Page 233: ...10 2 Section E Hydraulics 9803 6400 Section E 10 2 Issue 1 Hydraulic Pump JS200 JS240...
Page 234: ...10 3 Section E Hydraulics 9803 6400 Section E 10 3 Issue 1 Hydraulic Pump JS200 JS240...
Page 263: ...30 2 Section E Hydraulics 9803 6400 Section E 30 2 Issue 1 Control Valve JS200 JS240...
Page 264: ...30 3 Section E Hydraulics 9803 6400 Section E 30 3 Issue 1 Control Valve JS200 JS240...
Page 265: ...30 4 Section E Hydraulics 9803 6400 Section E 30 4 Issue 1 Control Valve JS200 JS240...
Page 266: ...30 5 Section E Hydraulics 9803 6400 Section E 30 5 Issue 1 Control Valve JS200 JS240...
Page 267: ...30 6 Section E Hydraulics 9803 6400 Section E 30 6 Issue 1 Control Valve JS200 JS240...
Page 268: ...30 7 Section E Hydraulics 9803 6400 Section E 30 7 Issue 1 Control Valve JS200 JS240...
Page 327: ...51 12 Section E Hydraulics 9803 6400 Section E 51 12 Issue 1 Solenoid Valve 8 spool...
Page 328: ...55 1 Schematic Section E Hydraulics 9803 6400 Section E 55 1 Issue 1 Shuttle Valve...
Page 330: ...55 3 Schematic Section E Hydraulics 9803 6400 Section E 55 3 Issue 1 Cushion Valves...
Page 481: ...7 15 Section F Transmission 9803 6400 Section F 7 15 Issue 2 Motor...
Page 482: ...7 16 Section F Transmission 9803 6400 Section F 7 16 Issue 1 Motor...