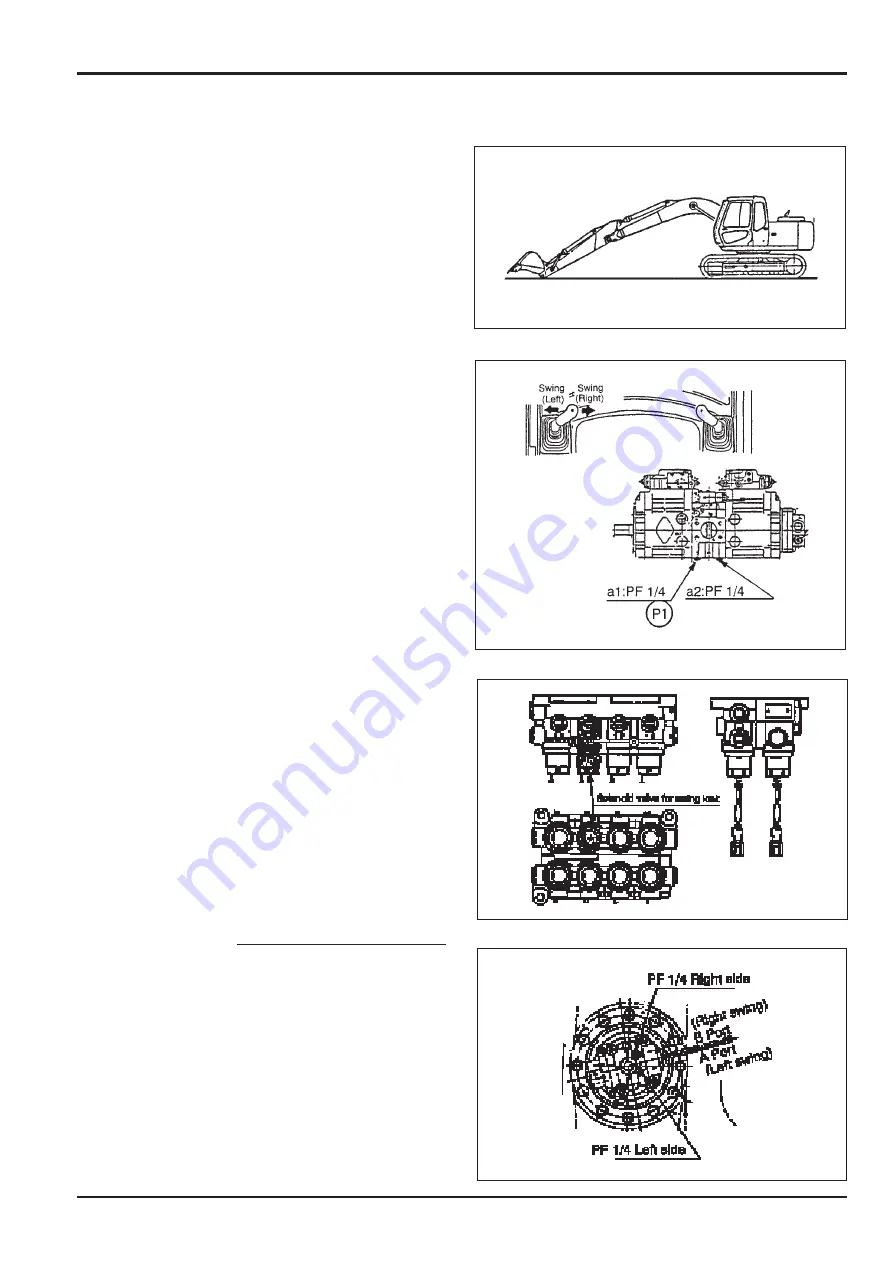
4 - 4
Slew Motor Pressure Relief
1. Prepare the machine
Put the operators lever into neutral, lower the gate lock
lever. Start the engine and place the machine on level
ground, lower and open the dipper and set the bucket on
the ground. Stop the engine.
2.
Release the hydraulic oil tank pressure.
(See
Releasing Tank Pressure
)
.
3.
Connect a 0-500 bar (0-7000 lb/in
2
) pressure gauge and
adaptor to the port marked P1 on the pump.
4. Initiate slew lock procedures.
a.
Remove the water-proof connector on the slew lock
solenoid valve, which is on the hydraulic pump side.
b.
Press the slew lock switch which is on the left hand
console inside the cab, and confirm that the slew
(swing) lock symbol appears on the monitor.
c.
Start the engine, and operate the engine at around
1000 r.p.m, then operate the slew lever slowly. Listen
to confirm that the relief sound is heard and that the
machine does not slew.
d.
Run the engine at maximum no-load speed and in the
S
mode.
e.
Operate the slew lever.
5.
Confirm the pressure of 299.8 ± 14.4 bar (4408 ± 213
lb/in
2
) at the gauge.
Notes:
1.
If the water-proof slew lock solenoid valve is not
removed, slew lock status can be obtained with the
slew lock switch
ON
, but slew relief is not carried out.
2.
Wire colour code to the solenoid is Dark Green.
3.
Pressure measurement is also possible on the slew
motor, upper section.
6.
If the pressure is within the limits, stop engine release
tank pressure and remove the gauge and adaptor; If the
readings are outside the limits, continue as below.
7. Pressure Adjustment
a.
Confirm the present pressure reading.
b.
The difference between the set pressure and the
present pressure determines the number of shims
F
required for adjustment.
The No of shims = Set pressure-Present Pressure
4.83 bar (71.1 lb/in
2
)
8.
Remove the relief valve assembly from the slew motor.
Note:
If both relief valves are removed at the same time,
mark them left and right to facilitate reassembly in the
correct position.
Section E
Hydraulics
9803/6400
Section E
4 - 4
Issue 2*
Pressure Testing
*
Summary of Contents for JS 200 Series
Page 57: ...9 1 Section 3 Routine Maintenance 9803 6400 Section 3 9 1 Issue 2 Component Location Diagram...
Page 113: ......
Page 137: ...5 3 Section C Electrics 9803 6400 Section C 5 3 Issue 2 Pump Control FLOW CHART...
Page 201: ...10 7 Section C Electrics 9803 6400 Section C 10 7 Issue 1 CAPs II Diagnostic system K C...
Page 215: ...Section E Section E Hydraulics 9803 6400 Issue 2 3 2 3 2 Schematics...
Page 217: ...Section E Section E 9803 6400 Issue 2 3 3 3 3 Hydraulics Schematics...
Page 218: ...3 5 Section E Hydraulics 9803 6400 Section E 3 5 Issue 1 Schematics Shuttle Block JS200 JS240...
Page 232: ...10 1 Section E Hydraulics 9803 6400 Section E 10 1 Issue 1 Hydraulic Pump JS200 JS240...
Page 233: ...10 2 Section E Hydraulics 9803 6400 Section E 10 2 Issue 1 Hydraulic Pump JS200 JS240...
Page 234: ...10 3 Section E Hydraulics 9803 6400 Section E 10 3 Issue 1 Hydraulic Pump JS200 JS240...
Page 263: ...30 2 Section E Hydraulics 9803 6400 Section E 30 2 Issue 1 Control Valve JS200 JS240...
Page 264: ...30 3 Section E Hydraulics 9803 6400 Section E 30 3 Issue 1 Control Valve JS200 JS240...
Page 265: ...30 4 Section E Hydraulics 9803 6400 Section E 30 4 Issue 1 Control Valve JS200 JS240...
Page 266: ...30 5 Section E Hydraulics 9803 6400 Section E 30 5 Issue 1 Control Valve JS200 JS240...
Page 267: ...30 6 Section E Hydraulics 9803 6400 Section E 30 6 Issue 1 Control Valve JS200 JS240...
Page 268: ...30 7 Section E Hydraulics 9803 6400 Section E 30 7 Issue 1 Control Valve JS200 JS240...
Page 327: ...51 12 Section E Hydraulics 9803 6400 Section E 51 12 Issue 1 Solenoid Valve 8 spool...
Page 328: ...55 1 Schematic Section E Hydraulics 9803 6400 Section E 55 1 Issue 1 Shuttle Valve...
Page 330: ...55 3 Schematic Section E Hydraulics 9803 6400 Section E 55 3 Issue 1 Cushion Valves...
Page 481: ...7 15 Section F Transmission 9803 6400 Section F 7 15 Issue 2 Motor...
Page 482: ...7 16 Section F Transmission 9803 6400 Section F 7 16 Issue 1 Motor...