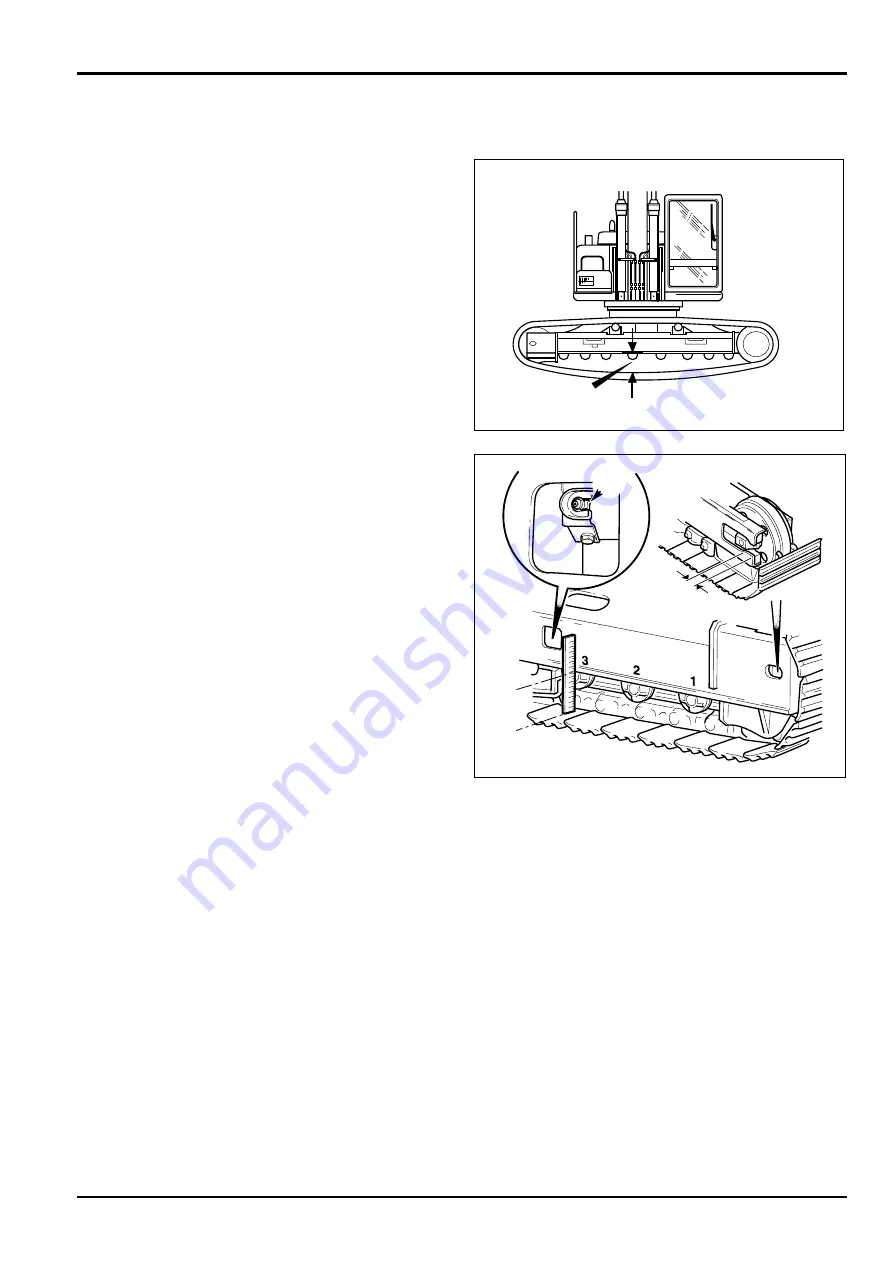
7 - 2
Checking/Adjusting the Track Tension
1. Prepare the Machine
Position the machine on level ground. Run it backwards
and forwards several times. Stop after running it
forwards.
Carry out steps 1 to 3 of
Cleaning the Tracks
. Block up
the undercarriage frame. Finish track rotation by running
the track forwards. Stop the engine and remove the
starter key.
!
!
WARNING
NEVER position yourself or any part of your body under a
raised machine which is not properly supported. If the
machine moves unexpectedly you could become
trapped and suffer serious injury or be killed.
INT-3-3-7
2. Check the Tension
Measure gap
A
in line with the fourth roller from the front
and between the lower surface of the track frame and
the upper surface of the shoe. The dimension should be
275-295 mm for hard ground conditions. For operation
on soft sand or sticky mud it should be 320-340 mm.
3. Adjust the Track Tension
Adjustment is made by either injecting or releasing
grease from the check valve
B
. Inject grease to reduce
the gap (increase the tension) or open to release grease
and increase the gap.
!
!
WARNING
When opening the check valve always stand to one side
and loosen a little at a time until grease starts to come
out. If you over-loosen too much grease could spurt out
or the valve cover fly out and cause serious injury.
8-3-4-5
!
!
WARNING
Under no circumstances must the check valve be
dismantled or any attempt made to remove the grease
nipple from the check valve.
8-3-4-9
If gap
C
exists between the idler wheel shaft and the
track frame, you may use pressure to apply the grease. If
there is no gap
C
after the application of grease, then the
necessary repairs must be carried out.
Note:
Excessive tension can cause the track rail to wear the
drive rollers and sprocket, insufficient tension can cause
wear to the drive sprocket and track rail.
4. Lower the Track
Remove the blocks from beneath the undercarriage and
lower the track to the ground using the boom and dipper
controls.
5. Repeat for the Opposite Track
Slew the boom round to the other side and repeat steps
1 to 4 above.
Section 3
Routine Maintenance
9803/6400
Section 3
7 - 2
Issue 3*
Tracks and Running Gear
(continued)
JS03770
A
*
*
A343970
B
B
C
C
A
A
Summary of Contents for JS 200 Series
Page 57: ...9 1 Section 3 Routine Maintenance 9803 6400 Section 3 9 1 Issue 2 Component Location Diagram...
Page 113: ......
Page 137: ...5 3 Section C Electrics 9803 6400 Section C 5 3 Issue 2 Pump Control FLOW CHART...
Page 201: ...10 7 Section C Electrics 9803 6400 Section C 10 7 Issue 1 CAPs II Diagnostic system K C...
Page 215: ...Section E Section E Hydraulics 9803 6400 Issue 2 3 2 3 2 Schematics...
Page 217: ...Section E Section E 9803 6400 Issue 2 3 3 3 3 Hydraulics Schematics...
Page 218: ...3 5 Section E Hydraulics 9803 6400 Section E 3 5 Issue 1 Schematics Shuttle Block JS200 JS240...
Page 232: ...10 1 Section E Hydraulics 9803 6400 Section E 10 1 Issue 1 Hydraulic Pump JS200 JS240...
Page 233: ...10 2 Section E Hydraulics 9803 6400 Section E 10 2 Issue 1 Hydraulic Pump JS200 JS240...
Page 234: ...10 3 Section E Hydraulics 9803 6400 Section E 10 3 Issue 1 Hydraulic Pump JS200 JS240...
Page 263: ...30 2 Section E Hydraulics 9803 6400 Section E 30 2 Issue 1 Control Valve JS200 JS240...
Page 264: ...30 3 Section E Hydraulics 9803 6400 Section E 30 3 Issue 1 Control Valve JS200 JS240...
Page 265: ...30 4 Section E Hydraulics 9803 6400 Section E 30 4 Issue 1 Control Valve JS200 JS240...
Page 266: ...30 5 Section E Hydraulics 9803 6400 Section E 30 5 Issue 1 Control Valve JS200 JS240...
Page 267: ...30 6 Section E Hydraulics 9803 6400 Section E 30 6 Issue 1 Control Valve JS200 JS240...
Page 268: ...30 7 Section E Hydraulics 9803 6400 Section E 30 7 Issue 1 Control Valve JS200 JS240...
Page 327: ...51 12 Section E Hydraulics 9803 6400 Section E 51 12 Issue 1 Solenoid Valve 8 spool...
Page 328: ...55 1 Schematic Section E Hydraulics 9803 6400 Section E 55 1 Issue 1 Shuttle Valve...
Page 330: ...55 3 Schematic Section E Hydraulics 9803 6400 Section E 55 3 Issue 1 Cushion Valves...
Page 481: ...7 15 Section F Transmission 9803 6400 Section F 7 15 Issue 2 Motor...
Page 482: ...7 16 Section F Transmission 9803 6400 Section F 7 16 Issue 1 Motor...