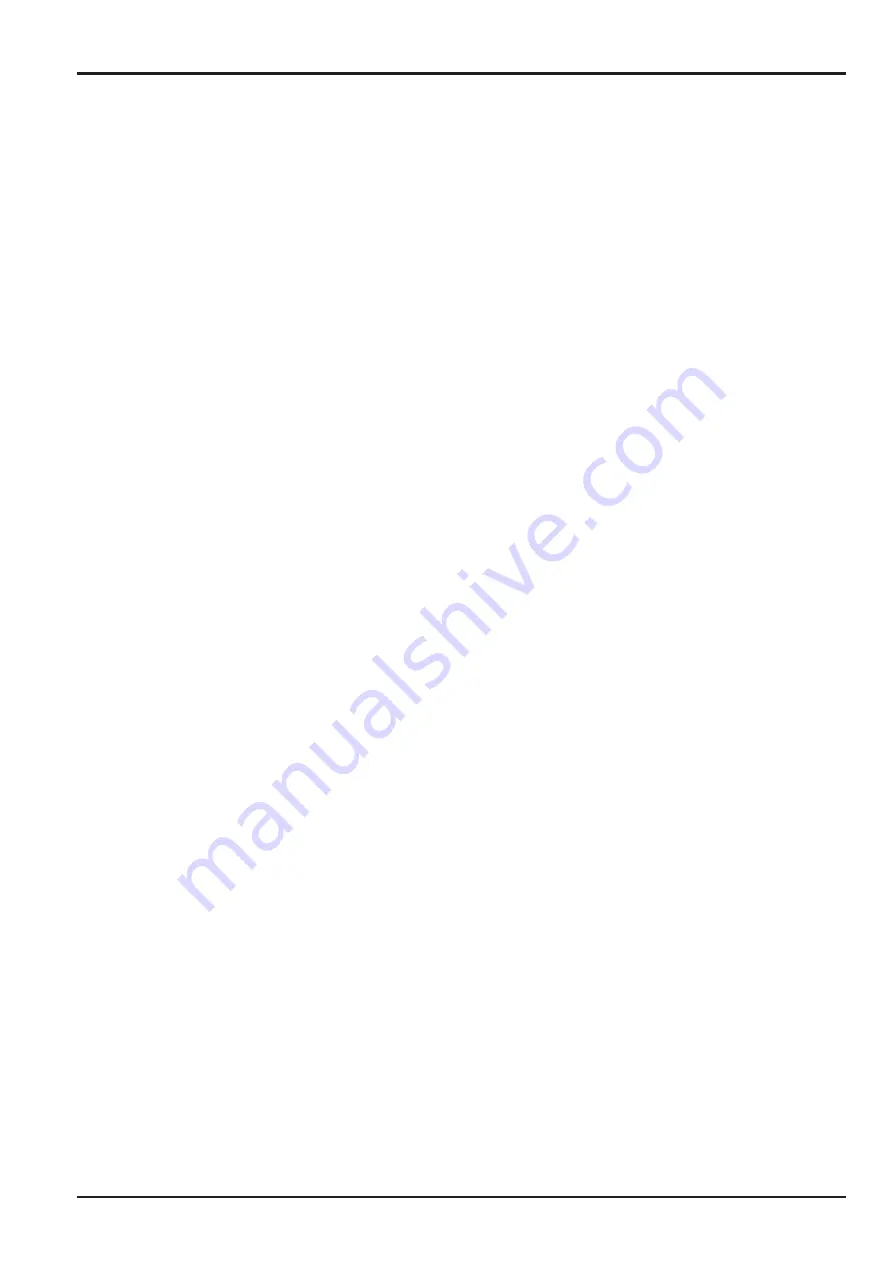
6 - 1
Direct Glazing
The following procedures explain how to correctly remove
and install panes of glass that are directly bonded to the cab
frame apertures. When carrying out the procedures, relevant
safety precautions must be taken.
1
Always wear safety glasses during both removal and
replacement.
2
Use protective gloves - heavy duty leather gauntlet type
gloves when cutting out the broken glass; 'non-slip' type
gloves when handling/moving panes of glass; surgical
type gloves when using the polyurethane adhesives.
3
Wear protective overalls.
4
DO NOT smoke - the activators and primers used in the
procedures are highly flammable.
5
Do not attempt to handle or move panes of glass unless
you are using glass lifters (see
Service Tools
, Section
1).
Several special tools are required to successfully complete
the removal and replacement procedures. Reference is
made to the tools in the text. The majority of these tools can
be obtained locally and the remainder from JCB Service (see
Service Tools
, Section 1).
The work must only be carried out in a dry, frost free
environment. A protective canopy may be required or the
machine/frame must be moved to a sheltered area. In damp
or wet conditions, hinged doors and window frames can be
removed from the machine and taken to a more suitable (dry)
environment.
Glass should not be replaced at temperatures below 5°C
(41°F).
Removing the Broken Glass and Old Sealant
!
!
WARNING
Always wear safety glasses when removing or installing
screen glass. Never use a power operated knife when
removing the sealant around a toughened glass screen.
The action of the knife could cause particles of glass to
be thrown with sufficient force to cause serious injury,
even when safety glasses are being worn. Use only hand
operated tools when working with toughened glass.
BF 2-3/1
Section B
Body & Framework
9803/6400
Section B
6 - 1
Issue 1
Cab
Summary of Contents for JS 200 Series
Page 57: ...9 1 Section 3 Routine Maintenance 9803 6400 Section 3 9 1 Issue 2 Component Location Diagram...
Page 113: ......
Page 137: ...5 3 Section C Electrics 9803 6400 Section C 5 3 Issue 2 Pump Control FLOW CHART...
Page 201: ...10 7 Section C Electrics 9803 6400 Section C 10 7 Issue 1 CAPs II Diagnostic system K C...
Page 215: ...Section E Section E Hydraulics 9803 6400 Issue 2 3 2 3 2 Schematics...
Page 217: ...Section E Section E 9803 6400 Issue 2 3 3 3 3 Hydraulics Schematics...
Page 218: ...3 5 Section E Hydraulics 9803 6400 Section E 3 5 Issue 1 Schematics Shuttle Block JS200 JS240...
Page 232: ...10 1 Section E Hydraulics 9803 6400 Section E 10 1 Issue 1 Hydraulic Pump JS200 JS240...
Page 233: ...10 2 Section E Hydraulics 9803 6400 Section E 10 2 Issue 1 Hydraulic Pump JS200 JS240...
Page 234: ...10 3 Section E Hydraulics 9803 6400 Section E 10 3 Issue 1 Hydraulic Pump JS200 JS240...
Page 263: ...30 2 Section E Hydraulics 9803 6400 Section E 30 2 Issue 1 Control Valve JS200 JS240...
Page 264: ...30 3 Section E Hydraulics 9803 6400 Section E 30 3 Issue 1 Control Valve JS200 JS240...
Page 265: ...30 4 Section E Hydraulics 9803 6400 Section E 30 4 Issue 1 Control Valve JS200 JS240...
Page 266: ...30 5 Section E Hydraulics 9803 6400 Section E 30 5 Issue 1 Control Valve JS200 JS240...
Page 267: ...30 6 Section E Hydraulics 9803 6400 Section E 30 6 Issue 1 Control Valve JS200 JS240...
Page 268: ...30 7 Section E Hydraulics 9803 6400 Section E 30 7 Issue 1 Control Valve JS200 JS240...
Page 327: ...51 12 Section E Hydraulics 9803 6400 Section E 51 12 Issue 1 Solenoid Valve 8 spool...
Page 328: ...55 1 Schematic Section E Hydraulics 9803 6400 Section E 55 1 Issue 1 Shuttle Valve...
Page 330: ...55 3 Schematic Section E Hydraulics 9803 6400 Section E 55 3 Issue 1 Cushion Valves...
Page 481: ...7 15 Section F Transmission 9803 6400 Section F 7 15 Issue 2 Motor...
Page 482: ...7 16 Section F Transmission 9803 6400 Section F 7 16 Issue 1 Motor...