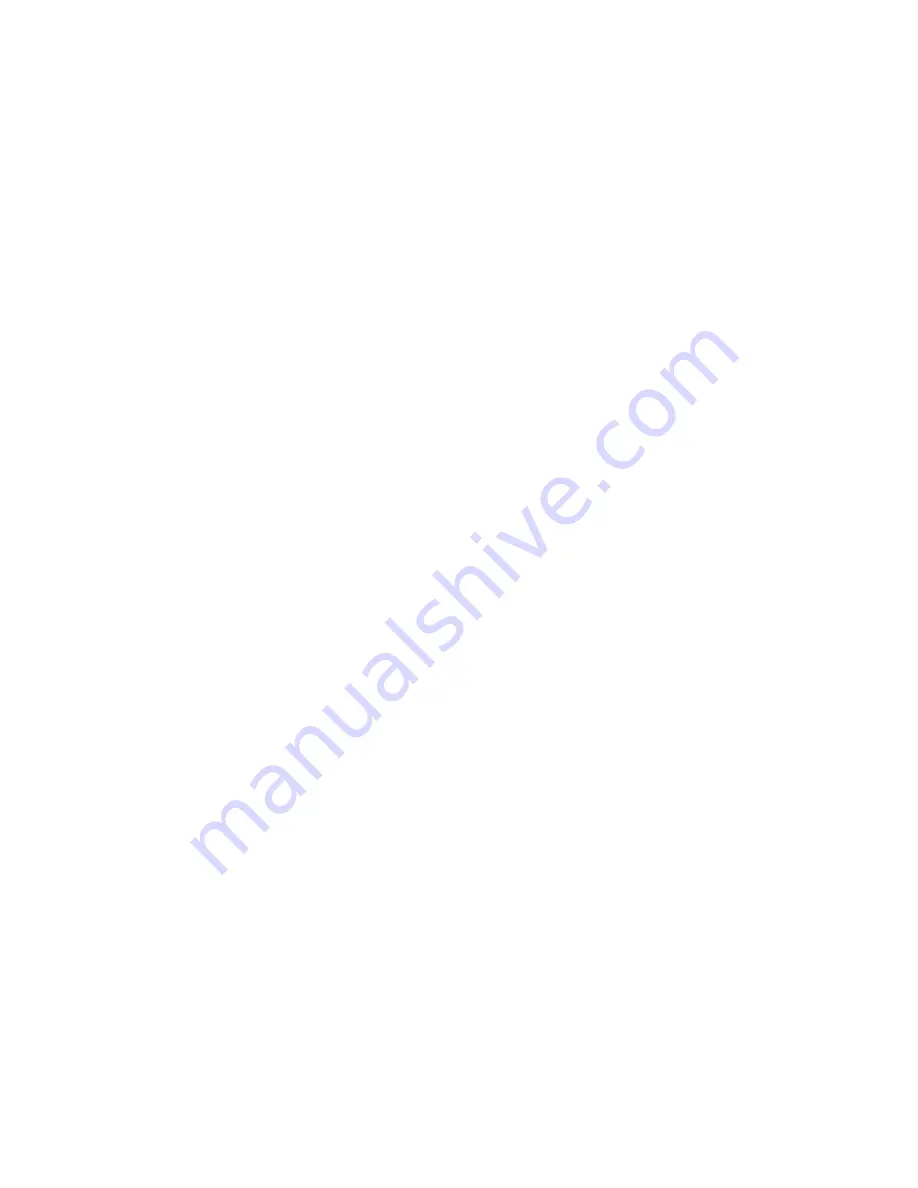
3-26
3.6.2.4
Turn off DC Power Supply. Disconnect supply line from P2
BATTERY connector.
3.6.3 Battery Charge Verification & Adjustment
The following requires Iradimed TF009 Battery Simulator:
3.6.3.1
Connect Battery Simulator TF009 to P2 BATTERY connector
and connect DC Power Supply to P6 POWER IN connector. Connect
meter to measure Amps to Battery Simulator (This is the DC Power
Supply current). Ensure TF009 Battery Simulator Load Knob is turned
fully counter-clockwise. Set DC Power Supply to 19 VDC. Adjust Battery
Simulator Load Knob clockwise until charge current flows. Verify Power
LED is lit Green and changes to Yellow (or Amber) when charge current
begins to flow.
3.6.3.2
Adjust Battery Simulator Load Knob fully CCW for maximum
charge current. Verify current 1.4A +/- 0.2A and Power LED remains
Yellow (or Amber).
3.6.3.3
Adjust Battery Simulator Load Knob CW for 0.50A +/-0.03A
and adjust CHRG Pot R89 for 16.82V +/-0.01V at P2-2.
3.6.3.4
Disconnect Battery Simulator cable from P2 BATTERY connec-
tor.
3.6.3.5
Reconnect internal P2 BATTERY connector.
3.6.4 Pump Motor Speed Adjustment
Reference the Section 2 Service Mode description
.
Put Pump into Service
Mode by pressing Keypad On (I) button and holding the Keypad
CANCEL key depressed until the Service Mode is displayed.
3.6.4.1
Set R41 (feedback) fully CW. R57 (frequency) fully CCW, R52
(speed) fully CCW. Scope Setup: Channel 1, Sweep Speed to 2ms,
100v/division. Channel 2, Sweep Speed to 2ms, 2v/division.
3.6.4.2
Select MANUAL PUMP RUN, press and hold ENTER on Keypad
(100% duty cycle). Adjust R57 CW until speed begins to increase or
speed reaches approximately 60-70 RPM. Ensure motor is running CCW
(when viewed from the motor end).
3.6.4.3
Adjust R41 fully CCW and note speed is above 240 RPM. Then
Reduce speed by turning R41 CW until speed reaches 130~150 RPM.
3.6.4.4
Connect Channel 1 (set to 100V/Div) to PJ5R Pin 1 on
IVPAB001 board. Connect Channel 2 (set to 2V/Div) to Encoder output
A (J1 pin 3 of the IVPAB043 or P1 pin 3 of the IVPAB003 Board) sync on
Channel 2. Select index and press enter. Verify motor goes to index.
Select Rate and set to 20, press Start/Stop A. Adjust R57 drive pulse
Channel 1 to 4~8ms. Ensure that Channel 2 is measuring 2 pulses
(tics). Monitor the lower left counter on the display (displays encoder
position from 0 to 1000), verify at least three revolutions. Insure enco-
der position count rolls over at 1000 back to 1, count should not count
more than 2 tics above 1000.
Summary of Contents for MRidium 3860
Page 2: ......
Page 4: ...1 4...
Page 8: ...iv...
Page 34: ...1 26...
Page 50: ...2 16...
Page 71: ...3 21 Figure 3 2...
Page 88: ...3 38 Figure B Too Much Taper Raw Curve 3860 61 Figure C Not Enough Taper Raw Curve 3860 61...
Page 95: ...3 45 Return the Stop Cock to the Test Position...
Page 106: ...4 2 Figure 4 1...