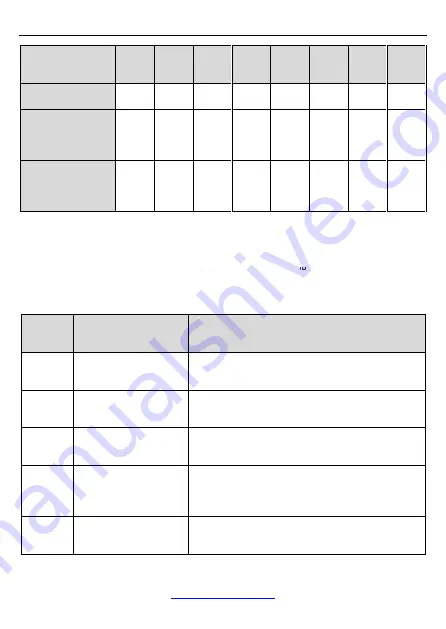
Goodrive100 inverters
Product overview
IKR Aandrijven en Besturen
www.ikr-industries.nl
GD100-XXXX-4
0R7G
1R5G
2R2G
004G
5R5G
7R5G
011G
015G
output power
(
kW
)
Rated input
current
(
A
)
3.4
5.0
5.8
13.5
19.5
25
32
40
Rated output
current
(
A
)
2.5
3.7
5
9.5
14
18.5
25
32
2.6 Structure diagram
Below is the layout figure of the inverter (take the inverter of 2.2kW as the example).
Fig 2-3 Product structure diagram
Serial No.
Name
Illustration
1
Keypad connections
Connect the keypad
2
Cover
Protect the internal parts and components
3
Keypad
See
Keypad Operation Procedure
for detailed information
4
Cooling fan
See
Maintenance and Hardware Fault Diagnose
for
detailed information
5
Name plate
See
Product Overview
for detailed information