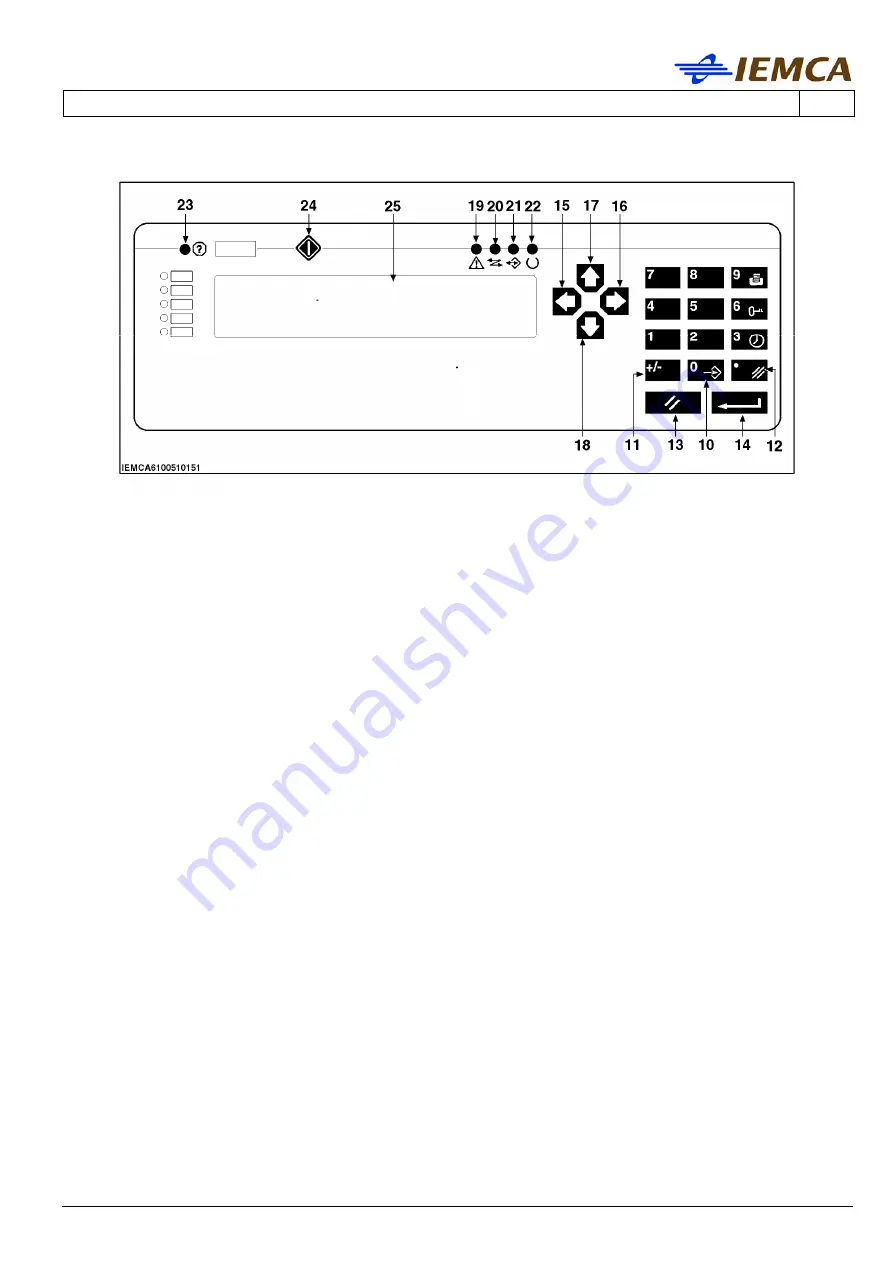
6 - USE AND OPERATION
SIR 52 MS52 P/F
EN
6 - Pag. 7 / 30
21 LED not enabled.
22 Green LED:
OFF mode - signals that the display is not active;
ON mode - signals that the display is active.
23 Green LED:
OFF mode - signals that no key is pressed;
ON mode - signals that any key is pressed.
Red
LED:
status BLINK - indicates that the keyboard battery needs to be replaced (refer to Chapter 9
for instructions on how to replace it);
ON state - indicates serious problems in the keyboard.
24 Key not enabled.
25 Display.
Summary of Contents for SIR52 MS52 P
Page 2: ......
Page 4: ......
Page 6: ......
Page 20: ...EN 2 TECHNICAL INFORMATION SIR 52 MS52 P F 2 Pag 10 14 2 6 TECHNICAL INFORMATION...
Page 24: ...EN 2 TECHNICAL INFORMATION SIR 52 MS52 P F 2 Pag 14 14...
Page 50: ...EN 4 HANDLING AND INSTALLATION SIR 52 MS52 P F 4 Pag 22 22...
Page 72: ...EN 5 ADJUSTMENTS AND SETTING UP SIR 52 MS52 P F 5 Pag 22 22...
Page 102: ...EN 6 USE AND OPERATION SIR 52 MS52 P F 6 Pag 30 30...
Page 148: ...EN 9 PART REPLACEMENT SIR 52 MS52 P F 9 Pag 16 16...
Page 174: ...EN 11 GUIDE CHANNELS BAR PUSHER REVOLVING TIPS SIR 52 MS52 P F 11 Pag 6 6...
Page 185: ...12 GRIPPERS SIR 52 MS52 P F EN 12 Pag 11 34...
Page 203: ...12 GRIPPERS SIR 52 MS52 P F EN 12 Pag 29 34...
Page 212: ...EN 13 LIST OF AFTER SALES CENTERS SIR 52 MS52 P F 13 Pag 4 4...