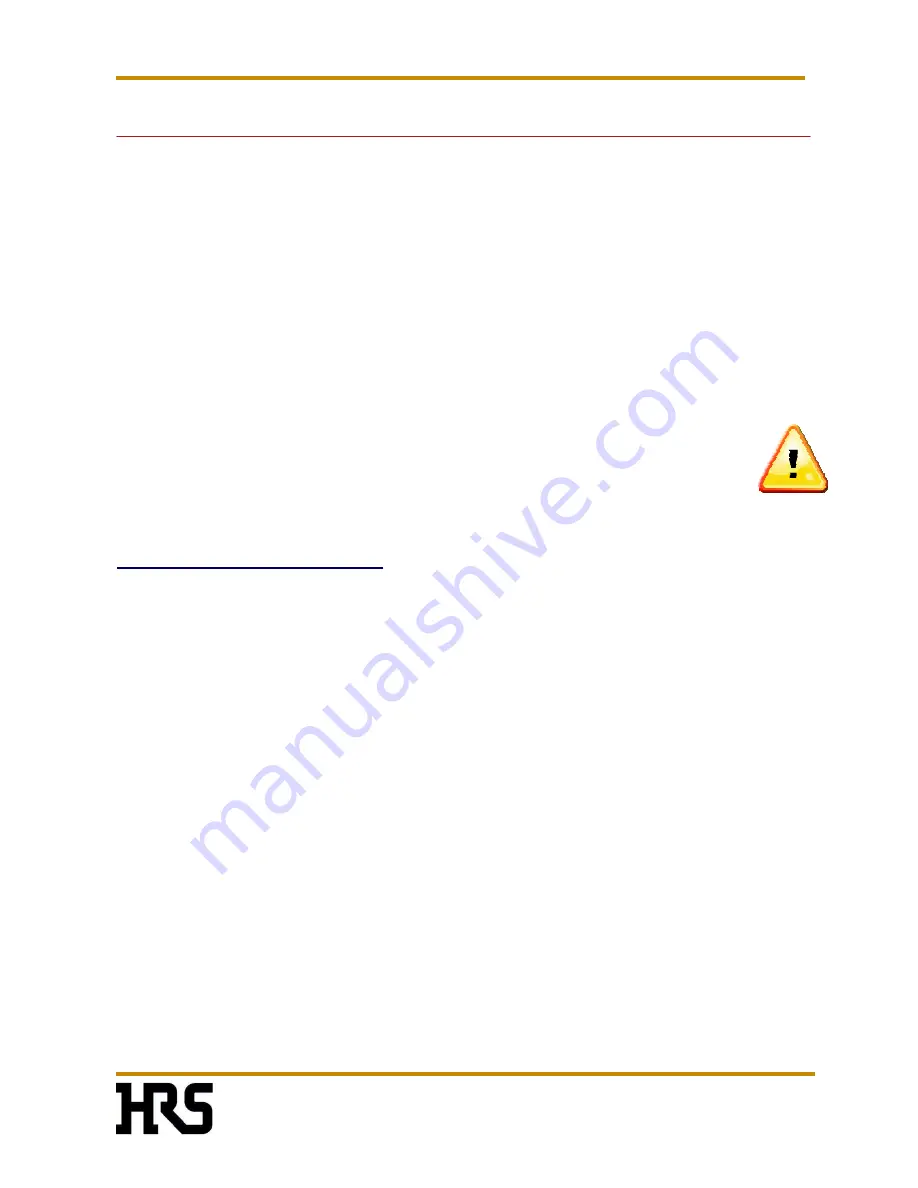
IT3/IT5
Connector System
PWB
A
SSEMBLY
N
OTES
Document Number:
ETAD-F0458
Revision 3.10
Page
46
of
73
10.7 Site Redressing
When the receptacle is removed from the PWB, some
excess solder will remain
on the pads.
The remaining solder
must be thoroughly cleaned
off before new solder paste can be added.
Excess solder should only be removed with non-contact, vacuum solder removal systems.
Some automated BGA workstations have solder removal systems built into them. These are
generally the safest methods of removing excess solder.
Manual vacuum solder removal
systems are also effective, but require more operator care to
ensure non-contact with the board and limit damage due to scraping with the nozzle or
localized overheating. If manual vacuum solder removal is necessary, the PWB should be
preheated to 150
o
C if tin-lead solder is used and 180
o
C if lead-free solder is used,
Soldering irons and wick should not be used to remove excess solder.
This method
provides the highest risk of lifted pads, torn traces, or damaged solder mask. If wick
must be used to remove the excess solder, see section titled
Solder Wicking
Guidelines
on next page.
Vacuum Solder Removal Guidelines
Liquid flux
should be dispensed onto the PWB to help the solder flow during the redressing
operation, especially if the redressing process uses air. Liquid flux may be optional if the
redressing operation uses nitrogen.
Preheat
the PWBs to
150
o
C for SnPb
, or
180
o
C for SAC alloys
.
Typical
nozzle temperatures
for removing excess solder are
280
o
C for SnPb
and
340
o
C for
SAC
.
Clearance
between the nozzle and the PWB should be approximately
125 um
.
Please
consult equipment manufacturer
for specific instructions on site redressing process.
Nov.1.2022 Copyright 2022 HIROSE ELECTRIC CO., LTD. All Rights Reserved.