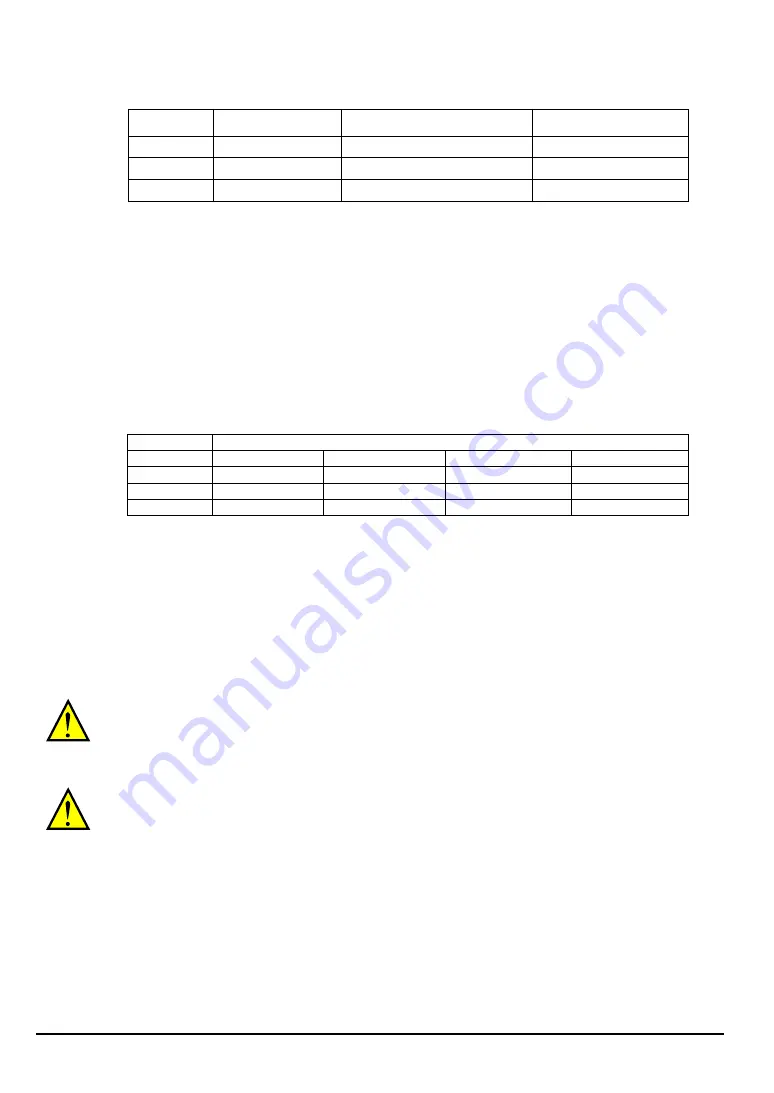
92
Components to be combined
Followings are the example of the safety devices to be combined.
Series
Model
Norms to comply
Certification date
GS9A
301
ISO13849-2 cat4, SIL3
06.06.2007
G9SX
GS226-T15-RC
IEC61508 SIL1-3
04.11.2004
NE1A
SCPU01-V1
IEC61508 SIL3
27.09.2006
The configuration of and components used in any circuit other than an appropriately pre approved
safety module that interfaces with the WL200 GS1/GS2 and EDM ports MUST be at least equivalent
to Cat.3 PLd under ISO 13849-1:2006 in order to be able to claim an overall Cat.3 PLd for the
WL200 and external circuit combination.
The EMI level that the external module has been assessed to must be at least equivalent to that of
Annex E in IEC 62061.
Periodical check (proof test)
Proof test is essential to be able to reveal any dangerous undetected failures after a period of time, in
this case 1 year. Carrying out this proof test at least one a year is the condition to comply the
ISO13849-1 PLd.
Terminal
Status
GS1
current OFF
current ON
current OFF
current ON
GS2
current OFF
current OFF
current ON
current ON
EDM
conducted
not conducted
not conducted
not conducted
(output)
forbidden
forbidden
forbidden
Allowed
- To activate (give current to) GS1 and GS2 simultaneously and separately to see output is allowed and EDM is
conducting
- To activate (give current to) both GS1 and GS2 to see output is allowed and EDM is not conducting
- To activate (give current to) GS1, not to activate GS2 and see output is forbidden and EDM is not conducting
- To activate (give current to) GS2, not to activate GS1 and see output is forbidden and EDM is not conducting
- To deactivate (interrupt current to) both GS1 and GS2 to see output is forbidden and EDM is conducting
Be sure to carry out the proof test when installation is ready before operation.
IF the protection diodes used when the units are in wired parallel are only single diodes then their condition would
be checked as part of the proof test. Check to reconfirm the diodes are not damaged when proof test is done.
Precautions
1. To assure, that the Safe Disable function appropriately fulfills the safety requirements
of the application, a throughout risk assessment for the whole safety system has to be
carried out.
2. The Safe Disable function does not cut the power supply to the drive and does not
provide electrical isolation. Before any installation or maintenance work is done, the
drives power supply must be switched off and place a tag/lock-out.
3. The wiring distance for the Safe Disable inputs should be shorter than 30 m.
4. The time from opening the Safe Disable input until the drive output is switched off is
less than 10 ms.