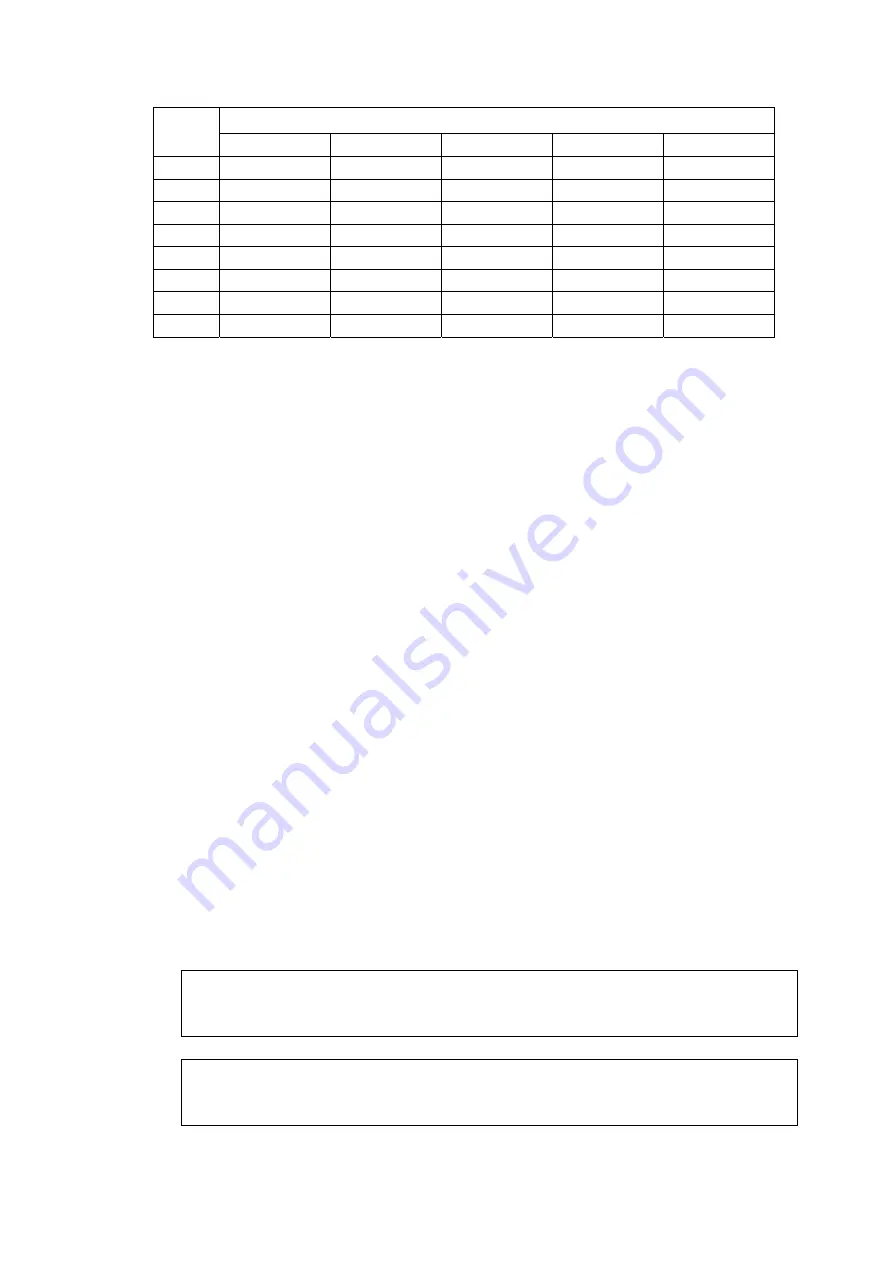
37
Table 5.6 Integral Time and Full-scale Current Values of Various Ranges
Integral Time
Range
Code 2ms 10ms 20ms 100ms
300ms
1 10mA
3.0mA
1.5mA
300µA
100µA
2 1.0mA
300µA
150µA
30µA
10µA
3 100µA
30µA
15µA
3µA
1µA
4 10µA
3.0µA
1.5µA
300µA
100nA
5 1.0µA
300nA
150nA
30nA
10nA
6 100nA
30nA
15nA
3nA
1nA
7 10nA
3.0nA
1.5nA
300pA
100pA
8 1.0nA
300pA
150pA
30pA
10pA
5.2.6 Setting integral time (sampling time)
Stable high-sensitivity current measurement is sometimes disabled due to impacts of
noise components contained in the input current. This meter performs A/D conversion
after integrating the input current to remove noise components for stable measurement.
The noise removal rate increases longer the integral time is and power source noise
(ham) can be greatly removed by increasing the integral time by integer multiplication of
the power source period.
A long integral time also increases the measuring time. Set an appropriate integral time
depending on measured resistance value (current value) referring to 5.1.5 Setting
measuring range.
The integral time can be set in increment of 1ms or 1PLC.
(1) Keying
(a) Press the [F5] PSET key to set up the Measuring Condition Setting screen.
(b) Move to “SAMPL:” operating the cursor moving keys [
◄
], [
►
], [
▲
] and [
▼
]
and input an integral time.
(c) [F4] and [F5] keys become the keys to select ms and PLC respectively. The
[F2] and [F3] keys change to the DOWN and UP functions respectively.
(d) Press the [F4] ms key to set input in the unit of ms, allowing setting of
integral time in increment of 1ms. The [F5] PLC key allows input in the unit
of PLC, allowing settings in increment of 2ms to 300ms and in increment of 1
to 15PLC.
[Note]
“PLC” stands for “one power line cycle” and is about 17ms at 60Hz and 20ms
at 50Hz.
[Notice]
Setting of an integral time changes the full-scale sensitivity of the current
measuring unit. Refer to 5.2.5 “Setting measuring range.”
Summary of Contents for DSM-8542
Page 2: ......
Page 21: ...11 3 2 Block Diagram of DSM 8542...
Page 89: ...79 Syntax Chart Fig 7 1 Message Syntax Chart...
Page 90: ...80 Command program header Fig 7 2 Program Header Syntax Chart...
Page 91: ...81 Fig 7 3 Syntax Chart of Data Part...
Page 138: ...128 11 Product Full View...
Page 139: ......
Page 140: ......