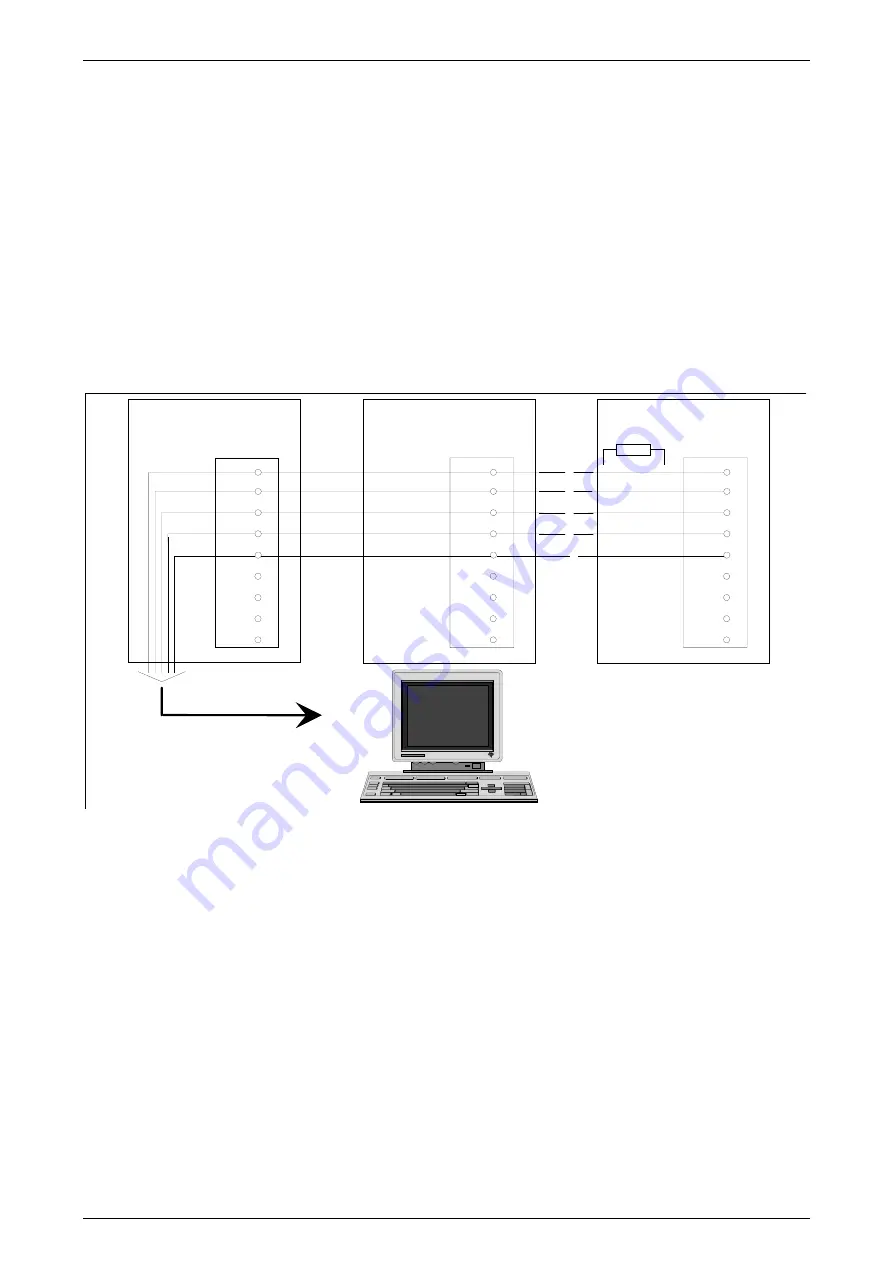
Page A10
Operations Manual SC-610
Harmonic Drive AG
900105
11/2005
APPENDIX D
Multi - Drop - Applications
This mode is available setting DIP-switch no. 10 at the front panel of the drive to ON. The wiring
principle for multi-drop applications is shown below. Each connected drive will also get it´s own
hardware address. The setting can be done by DIP-switches AS1-4 on the front panel or by using
the setup software Work Bench v5.
The picture below shows termination resistors on the last connected drive. The resistor can be
activated by using DIP-switch AS1.6 and set it to ON-position.
Multi-drop wiring principle for RS485:
TX-
TX+
RX+
RX-
DGND
3
7
8
2
5
6
7
8
9
X6
RS485
SC / A0
SC / A1
SC / An
c/f
Termination Res.
RS485
Interface cable refer
to chapter 4.2.7.
TX-
TX+
RX+
RX-
DGND
3
7
8
2
5
6
7
8
9
X6
RS485
TX-
TX+
RX+
RX-
DGND
3
7
8
2
5
6
7
8
9
X6
RS485
Summary of Contents for SC-610 Series
Page 1: ...Operations Manual AC Servo Controller SC 610 No 900105 11 2005 24 11 2005 FA...
Page 3: ......
Page 52: ...Operations Manual SC 610 Page A1 Harmonic Drive AG 900105 11 2005 APPENDIX...
Page 64: ...Operations Manual SC 610 Page A13 Harmonic Drive AG 900105 11 2005 APPENDIX G...
Page 65: ...Page A14 Operations Manual SC 610 Harmonic Drive AG 900105 11 2005 APPENDIX H...
Page 66: ...Operations Manual SC 610 Page A15 Harmonic Drive AG 900105 11 2005 APPENDIX I...
Page 67: ...Page A16 Operations Manual SC 610 Harmonic Drive AG 900105 11 2005 APPENDIX J...
Page 68: ...Operations Manual SC 610 Page A17 Harmonic Drive AG 900105 11 2005 APPENDIX K...
Page 69: ......