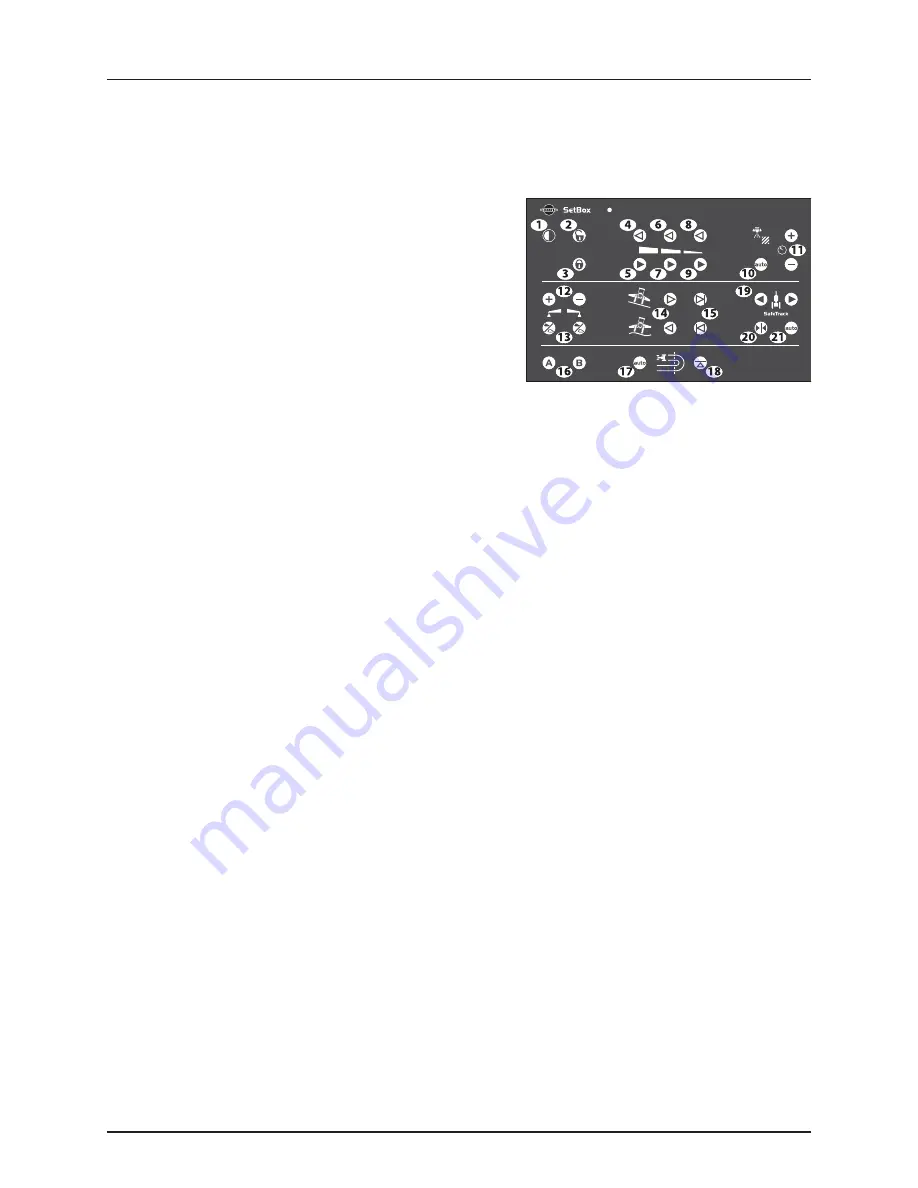
3 - Description
3.7
SetBox
The SetBox controls secondary functions. The keys are grouped into control areas to simplify operator understanding.
÷
NOTE! Self-propelled sprayers do not have a SetBox as the controls are built-in to the cabin.
1.
Power ON/OFF.
2.
Pendulum unlock.
3.
Pendulum lock.
4.
Inner wing fold.
5.
Inner wing unfold.
6.
1st outer wing fold.
7.
1st outer wing unfold.
8.
2nd outer wing fold.
9.
2nd outer wing unfold.
10.
Automatic volume rate selector.
11.
Manual pressure control.
12.
Foam marker regulation.
13.
Foam marker Left/Right selector.
14.
DynamicCenter adjustment (increments).
15.
DynamicCenter outer positions 1 or 5.
16.
Optional function A-B.
17.
HeadlandAssist automatic.
18.
HeadlandAssist boom align.
19.
SafeTrack manual control (if installed).
20.
SafeTrack align selector (if installed).
21.
SafeTrack automatic selector (if installed).
ATTENTION! Button 1 has different function on ISOBUS sprayers as this turns the JobCom ON/OFF.
ATTENTION! Buttons 17 and 18 can have different functions if the sprayer is equipped with AutoHeight.
ATTENTION! The Grip cannot be switched ON/OFF separately. It is automatically switched ON when tractor power is
turned ON (ISOBUS).
Summary of Contents for ISOBUS VT
Page 2: ......
Page 4: ......
Page 8: ...Table of contents TOC 4 ...
Page 10: ...1 Welcome 1 2 ...
Page 12: ...2 Safety notes 2 2 ...
Page 48: ...5 Menu 1 Daily settings 5 2 ...
Page 52: ...6 Menu 2 Setup 6 4 ...
Page 74: ...8 Menu 4 Toolbox 8 4 ...
Page 78: ...10 Maintenance 10 2 ...
Page 103: ......