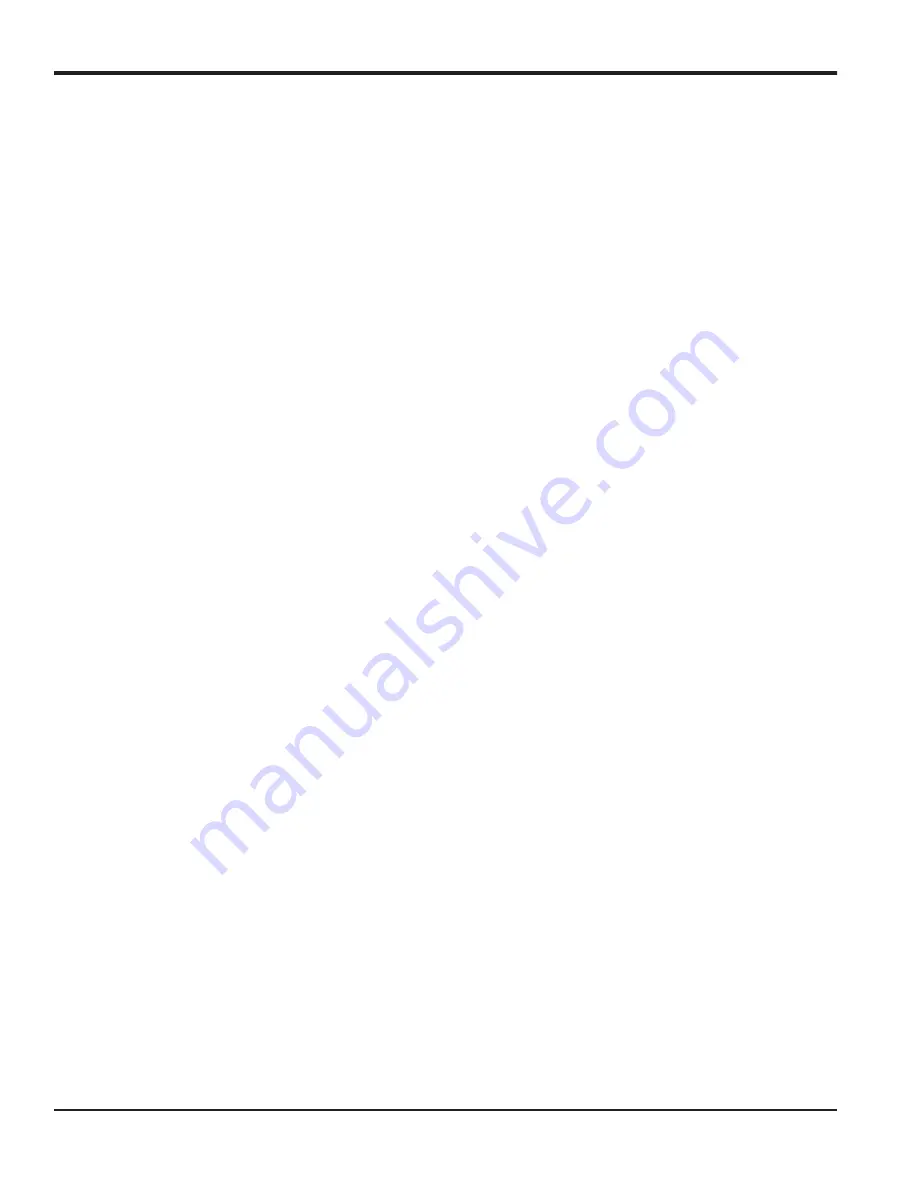
Chapter 9. Specifications
102
moisture.IQ User’s Manual
9.6 General Specifications
Display
Resistive WVGA, 800 (H) x 480 (V) pixels with touch screen
Display Functions
Display up to 12 channel/parameter combinations simultaneously using text and/or graphics
Operating Temperature
-20 to +60°C (-4 to +140°F)
Storage Temperature
-40 to +70°C (-40 to +158°F)
Auto-Calibration
Occurs on power up and at user-selectable time intervals
Warm-up Time
Meets specified accuracy within 5 minutes of turn-on
Data Logging
Up to six simultaneous logs per storage device, with up to 16 parameters each, stored in 4 GB Micro SDHC
Summary of Contents for moisture.IQ
Page 1: ...Moisture and Oxygen 910 298 Rev E September 2017 bhge com moisture IQ User s Manual ...
Page 2: ......
Page 4: ... no content intended for this page ...
Page 12: ...Preface x moisture IQ User s Manual no content intended for this page ...
Page 45: ...moisture IQ User s Manual 33 Chapter 2 Operation ...
Page 49: ...moisture IQ User s Manual 37 Chapter 2 Operation ...
Page 50: ...Chapter 2 Operation 38 moisture IQ User s Manual ...
Page 110: ...Chapter 8 Troubleshooting 98 moisture IQ User s Manual no content intended for this page ...
Page 180: ... no content intended for this page ...
Page 181: ......