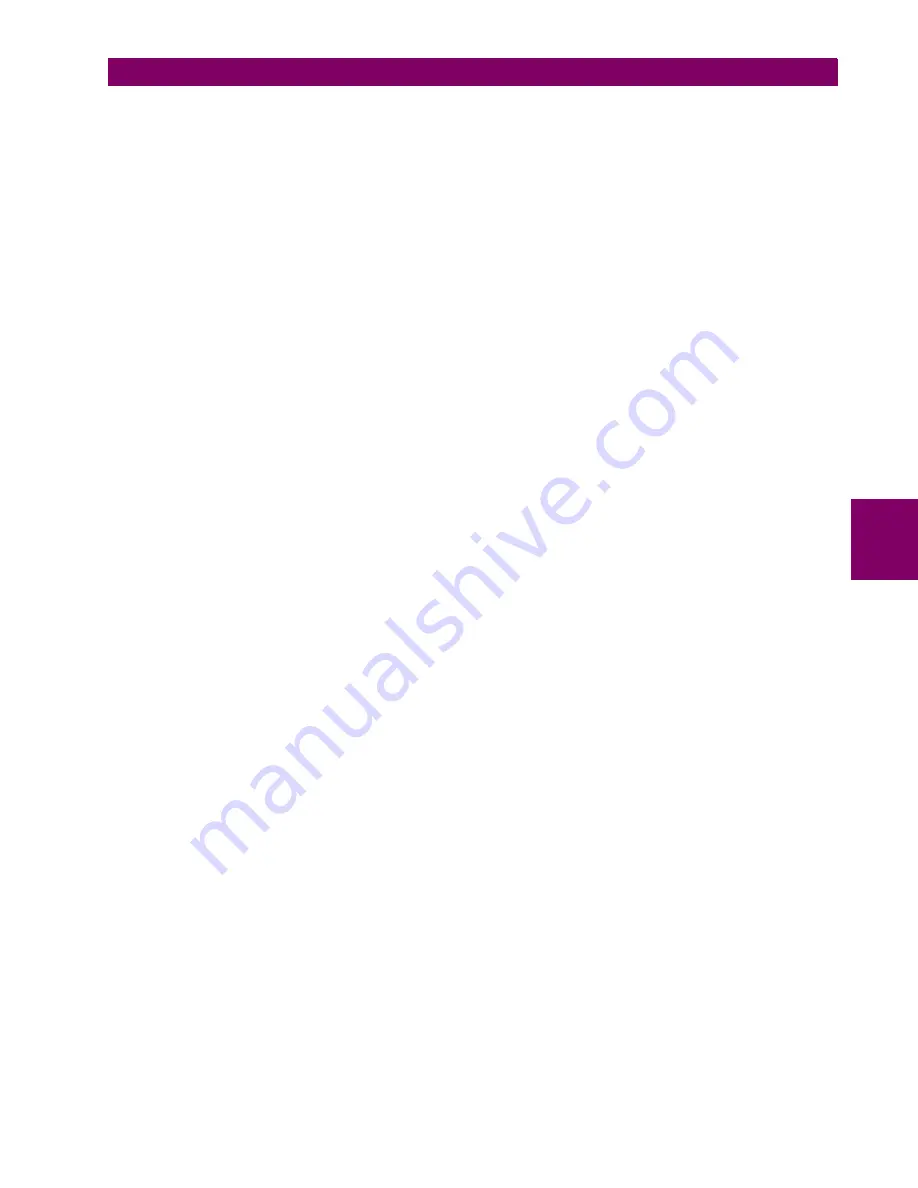
GE Multilin
F60 Feeder Protection System
5-23
5 SETTINGS
5.2 PRODUCT SETUP
5
The F60 has the ability of detecting if a data item in one of the GOOSE datasets is erroneously oscillating. This can be
caused by events such as errors in logic programming, inputs improperly being asserted and de-asserted, or failed station
components. If erroneously oscillation is detected, the F60 will stop sending GOOSE messages from the dataset for a min-
imum period of one second. Should the oscillation persist after the one second time-out period, the F60 will continue to
block transmission of the dataset. The F60 will assert the
MAINTENANCE ALERT: GGIO Ind XXX oscill
self-test error mes-
sage on the front panel display, where
XXX
denotes the data item detected as oscillating.
The configurable GOOSE feature is recommended for applications that require GOOSE data transfer between UR-series
IEDs and devices from other manufacturers. Fixed GOOSE is recommended for applications that require GOOSE data
transfer between UR-series IEDs.
IEC 61850 GOOSE messaging contains a number of configurable parameters, all of which must be correct to achieve the
successful transfer of data. It is critical that the configured datasets at the transmission and reception devices are an exact
match in terms of data structure, and that the GOOSE addresses and name strings match exactly. Manual configuration is
possible, but third-party substation configuration software may be used to automate the process. The EnerVista UR Setup-
software can produce IEC 61850 ICD files and import IEC 61850 SCD files produced by a substation configurator (refer to
the
IEC 61850 IED configuration
section later in this appendix).
The following example illustrates the configuration required to transfer IEC 61850 data items between two devices. The
general steps required for transmission configuration are:
1.
Configure the transmission dataset.
2.
Configure the GOOSE service settings.
3.
Configure the data.
The general steps required for reception configuration are:
1.
Configure the reception dataset.
2.
Configure the GOOSE service settings.
3.
Configure the data.
This example shows how to configure the transmission and reception of three IEC 61850 data items: a single point status
value, its associated quality flags, and a floating point analog value.
The following procedure illustrates the transmission configuration.
1.
Configure the transmission dataset by making the following changes in the
PRODUCT SETUP
ÖØ
COMMUNICATION
ÖØ
IEC 61850 PROTOCOL
Ö
GSSE/GOOSE CONFIGURATION
Ö
TRANSMISSION
ÖØ
CONFIGURABLE GOOSE
Ö
CONFIGURABLE
GOOSE 1
ÖØ
CONFIG GSE 1 DATASET ITEMS
settings menu:
–
Set
ITEM 1
to “GGIO1.ST.Ind1.q” to indicate quality flags for GGIO1 status indication 1.
–
Set
ITEM 2
to “GGIO1.ST.Ind1.stVal” to indicate the status value for GGIO1 status indication 1.
The transmission dataset now contains a set of quality flags and a single point status Boolean value. The reception
dataset on the receiving device must exactly match this structure.
2.
Configure the GOOSE service settings by making the following changes in the
PRODUCT SETUP
ÖØ
COMMUNICATION
ÖØ
IEC 61850 PROTOCOL
Ö
GSSE/GOOSE CONFIGURATION
Ö
TRANSMISSION
ÖØ
CONFIGURABLE GOOSE
Ö
CONFIGU-
RABLE GOOSE 1
settings menu:
–
Set
CONFIG GSE 1 FUNCTION
to “Enabled”.
–
Set
CONFIG GSE 1 ID
to an appropriate descriptive string (the default value is “GOOSEOut_1”).
–
Set
CONFIG GSE 1 DST MAC
to a multicast address (for example, 01 00 00 12 34 56).
–
Set the
CONFIG GSE 1 VLAN PRIORITY
; the default value of “4” is OK for this example.
–
Set the
CONFIG GSE 1 VLAN ID
value; the default value is “0”, but some switches may require this value to be “1”.
–
Set the
CONFIG GSE 1 ETYPE APPID
value. This setting represents the ETHERTYPE application ID and must match
the configuration on the receiver (the default value is “0”).
–
Set the
CONFIG GSE 1 CONFREV
value. This value changes automatically as described in IEC 61850 part 7-2. For
this example it can be left at its default value.
Summary of Contents for F60 UR Series
Page 2: ......
Page 4: ......
Page 30: ...1 20 F60 Feeder Protection System GE Multilin 1 5 USING THE RELAY 1 GETTING STARTED 1 ...
Page 48: ...2 18 F60 Feeder Protection System GE Multilin 2 2 SPECIFICATIONS 2 PRODUCT DESCRIPTION 2 ...
Page 126: ...4 30 F60 Feeder Protection System GE Multilin 4 2 FACEPLATE INTERFACE 4 HUMAN INTERFACES 4 ...
Page 354: ...5 228 F60 Feeder Protection System GE Multilin 5 9 TESTING 5 SETTINGS 5 ...
Page 382: ...6 28 F60 Feeder Protection System GE Multilin 6 5 PRODUCT INFORMATION 6 ACTUAL VALUES 6 ...
Page 398: ...8 8 F60 Feeder Protection System GE Multilin 8 2 FAULT LOCATOR 8 THEORY OF OPERATION 8 ...
Page 414: ...A 14 F60 Feeder Protection System GE Multilin A 1 PARAMETER LIST APPENDIXA A ...
Page 492: ...B 78 F60 Feeder Protection System GE Multilin B 4 MEMORY MAPPING APPENDIXB B ...
Page 530: ...D 10 F60 Feeder Protection System GE Multilin D 1 IEC 60870 5 104 APPENDIXD D ...
Page 542: ...E 12 F60 Feeder Protection System GE Multilin E 2 DNP POINT LISTS APPENDIXE E ...
Page 558: ...x F60 Feeder Protection System GE Multilin INDEX ...