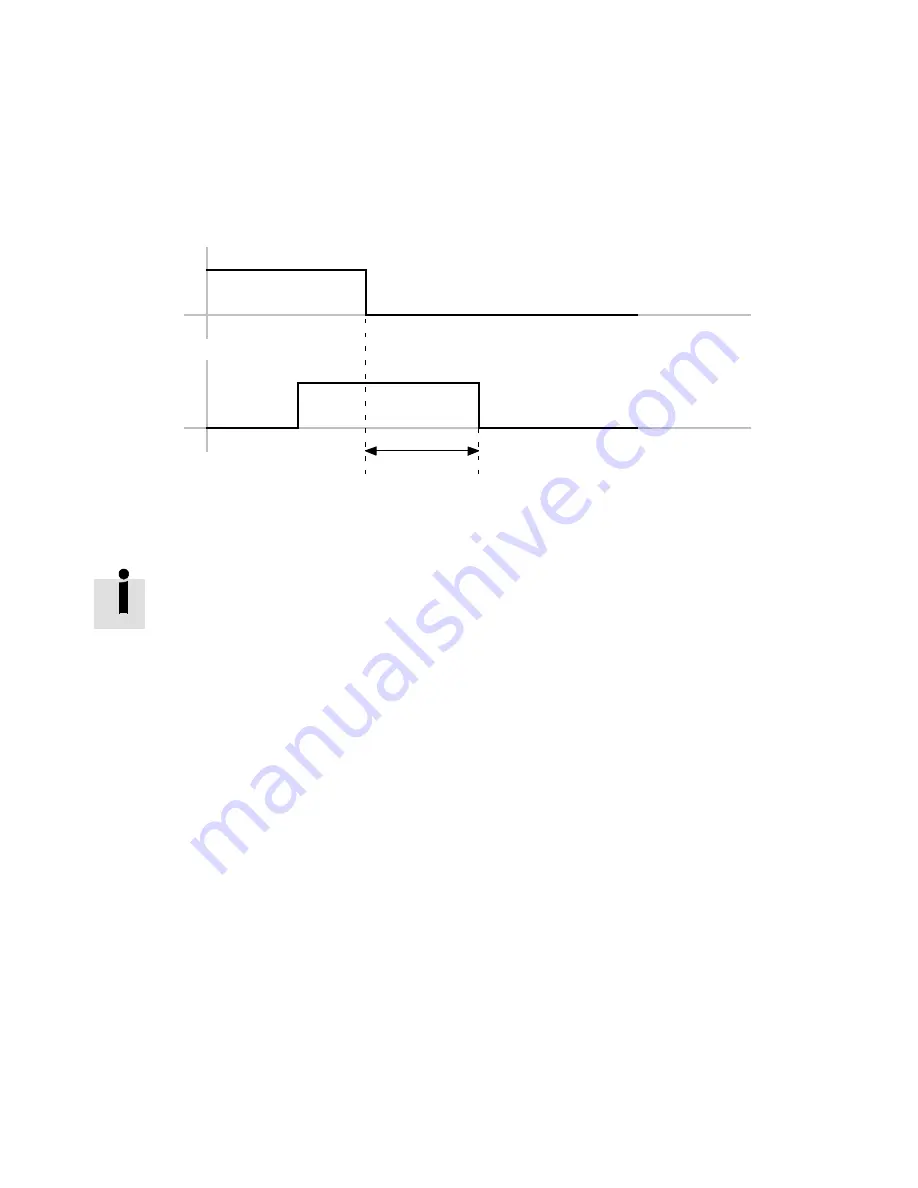
8
Service functions and diagnostic messages
80
Festo – GDCP-CMMP-M3-FW-EN – 1203NH
8.2.3
Acknowledgement of error messages
Error messages can be acknowledged through:
–
the parametrisation interface
–
the fieldbus (control word)
–
a decreasing edge at DIN5 [X1]
Controller
enable
DIN5 [X1]
1
“Error active”
1 L
80 ms
Fig. 8.1
Timing diagram: acknowledge error
Diagnostic events which are parametrised as warnings are automatically acknowledged
when the cause is no longer on hand.
8.2.4
Diagnostic messages
The significance and their measures for diagnostic messages are summarised in the following chapter:
(
chapter A Diagnostic messages).
Summary of Contents for CMMP-AS-***-M3 Series
Page 131: ......