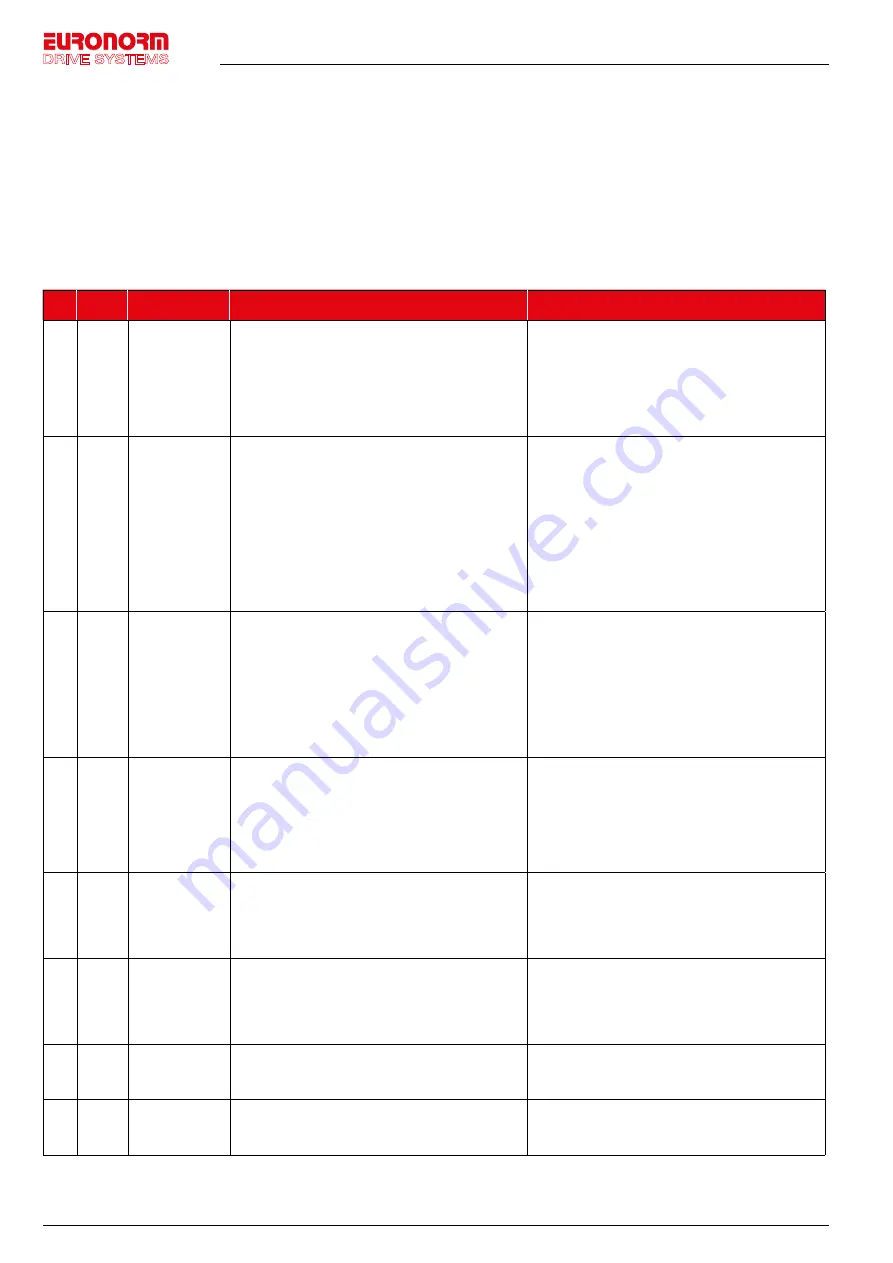
Hub van Doorneweg 8 • 2171 KZ Sassenheim – NL •
T
+31(0)252 228850 •
F
+31(0)252 228235 •
E
I
euronormdrives.com
Hub van Doorneweg 8 • 2171 KZ Sassenheim – NL •
T
+31(0)252 228850 •
F
+31(0)252 228235 •
E
I
euronormdrives.com
52
53
NEURN030000_220_A
NEURN030000_220_A
8 Troubleshooting
8.1 Fault alarm and countermeasures
JI500 inverter system operation in the process of failure, the inverter will protect the motor immediately to stop the output,
while the inverter fault relay contact action. Inverter panel will display the fault code, the fault code corresponding to the
type of fault and common solutions refer to the following table. List for reference only, please do not repair, transformation,
if you can not get rid of the trouble, please division or product agents to seek technical support.
No.
Fault
ID
Failure type
Possible causes
Solutions
1
Err.01
Inverter unit
protection
1. The short circuit of inverter output happens
2. The wiring for the motor and the inverter is too long
3. Module overheating
4. The internal wiring of inverter is loose
5. The main control panel is abnormal
6. The drive panel is abnormal.
7. The inverter module is abnormal
1. Eliminate peripheral faults
2. Additionally install the reactor or the output filter
3. Check the air duct is blocked or not and the fan is
working normally or not, and eliminate problems
4. Correctly plug all cables
5. Seek for technical support
2
Err.02
Acceleration
overcurrent
1.The acceleration time is too short
2. Manual torque boost or V/F curve is not suitable
3. The voltage is low
4. The short-circuit or earthing of inverter output
happens
5. The control mode is vector and without
identification of parameters
6. The motor that is rotating is started unexpectedly
7. Suddenly increase the load in the process of
acceleration.
8. The type selection of inverter is small
1. Increase acceleration time
2. Adjust manual torque boost or V/F curve
3. Set the voltage to the normal range
4. Eliminate peripheral faults
5. Perform identification for the motor parameters
6. Select Speed Tracking Start or restart after stopping
the motor.
7. Cancel the sudden load
8. Choose the inverter with large power level
3
Err.03
Deceleration
overcurrent
1. The short-circuit or earthing of inverter output
happens
2. The control mode is vector and without
identification of parameters
3. The deceleration time is too short
4. The voltage is low
5. Suddenly increase the load in the process of
deceleration.
6. Didn’t install braking unit and braking resistor
1. Eliminate peripheral faults
2. Perform identification for the motor parameters
3. Increase the deceleration time
4. Set the voltage to the normal range
5. Cancel the sudden load
6. Install braking unit and brake resistor
4
Err.04
Constant speed
overcurrent
1. The short-circuit or earthing of inverter output
happens
2. The control mode is vector and without
identification of parameters
3. The voltage is low
4. whether suddenly increase the load when running
5. The type selection of inverter is small
1. Eliminate peripheral faults
2. Perform identification for the motor parameters
3. Set the voltage to the normal range
4. Cancel the sudden load
5. Choose the inverter with large power level
5
Err.05
Acceleration
overvoltage
1. Didn’t install braking unit and braking resistor
2. The input voltage is high
3. There is external force to drag the motor to run
when accelerating.
4. The acceleration time is too short
1. Install braking unit and brake resistor
2. Set the voltage to the normal range
3. Cancel the external force or install braking
resistor.
4. Increase acceleration time
6
Err.06
Deceleration
overvoltage
1. The input voltage is high
2. There is external force to drag the motor to run
when decelerating.
3. The deceleration time is too short
4. Didn’t install braking unit and braking resistor
1. Set the voltage to the normal range
2. Cancel the external force or install braking
resistor.
3. Increase the deceleration time
4. Install braking unit and brake resistor
7
Err.07
Constant
speed
overvoltage
1. There is external force to drag the motor to run
when running
2. The input voltage is high
1. Cancel the external force or install braking
resistor.
2. Set the voltage to the normal range
8
Err.08
Control power
failure
1. The range of input voltage is not within the
specification;
2. Frequently reported under pressure fault.
Adjust the voltage to the range of the requirements of
specification