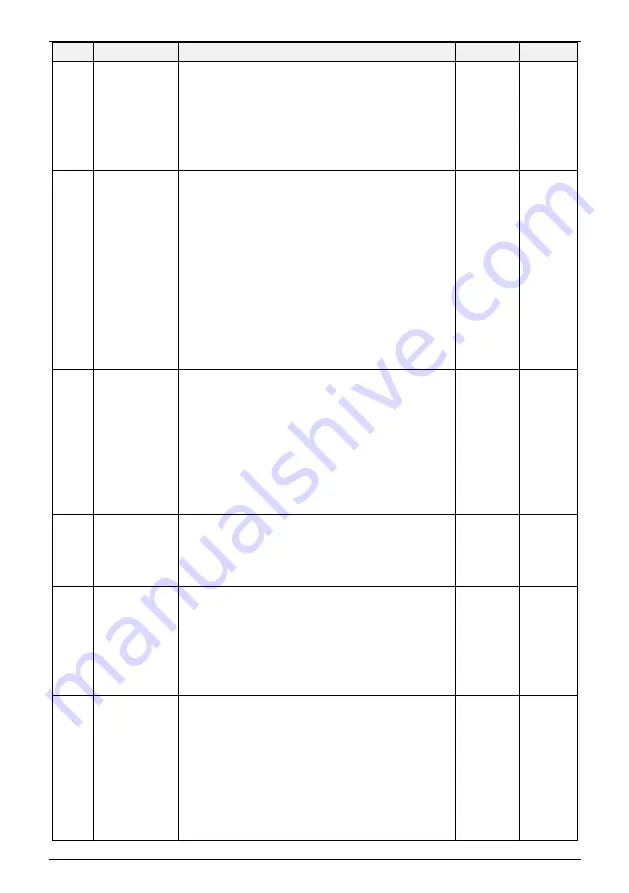
Chapter 7 Parameters
EMSD5 AC Servo Manual
58
No.
Name
Function
Rang
Default
too small, it would lead to low response, which
would result in shaking.
4.The value is bigger, the cut-off frequency is
higher and the response frequency is quicker. If
you need higher torque response frequency, it is
recommended to increase the setting value.
PA-8
Speed
detection filter
1.
To set the characters of speed detection filter.
2.
The value is smaller, the cut-off frequency is
lower and noise from the motor is smaller. If the
load inertia is great, reducing the setting value is
recommended. If the value is too small, it would
lead to low response, which would result in
shaking.
3.
The value is bigger, the cut-off frequency is
higher and the response frequency is quicker. If
you need higher torque response frequency, it is
recommended to increase the setting value.
20-500%
100
PA-9
Proportional
gain of position
loop
1.To set the proportional gain of position loop .
2.The value is bigger, the gain is higher and its
rigidity is stronger. So the position lag is smaller
under the same frequency command pulse
condition. But if it is too big, it will happen
oscillation.
3.The parameter value is set according to your
exact servo driving system model and the load.
1-1000
80
PA-10
Number of
pulses output
for each motor
revolution
To set the number of pulses output by the encoder AB
phase for each motor revolution.
0-20000
10000
PA-11
Command
pulses of each
motor
revolution
1.To set command pulses of each motor
revolution.
2.When it is set to 0, PA-12( numerator of
electronic gear for position command pulses),
PA-13(denominator of electronic gear for position
command pulses) are valid.
0-30000
10000
PA-12
1
st
numerator
of electronic
gear for
position
command
pulse
1.Set the electric gear ratio for position command
pulse.
2.In position control mode,it is convenient to
match all kinds of pulse source through set the
parameter PA-12 and PA-13, which helps to reach
ideal control resolution(angle/pulse).
3. P×G=N×C×4
P: pulses of input command; G:electric gear ratio;
0-32767
0