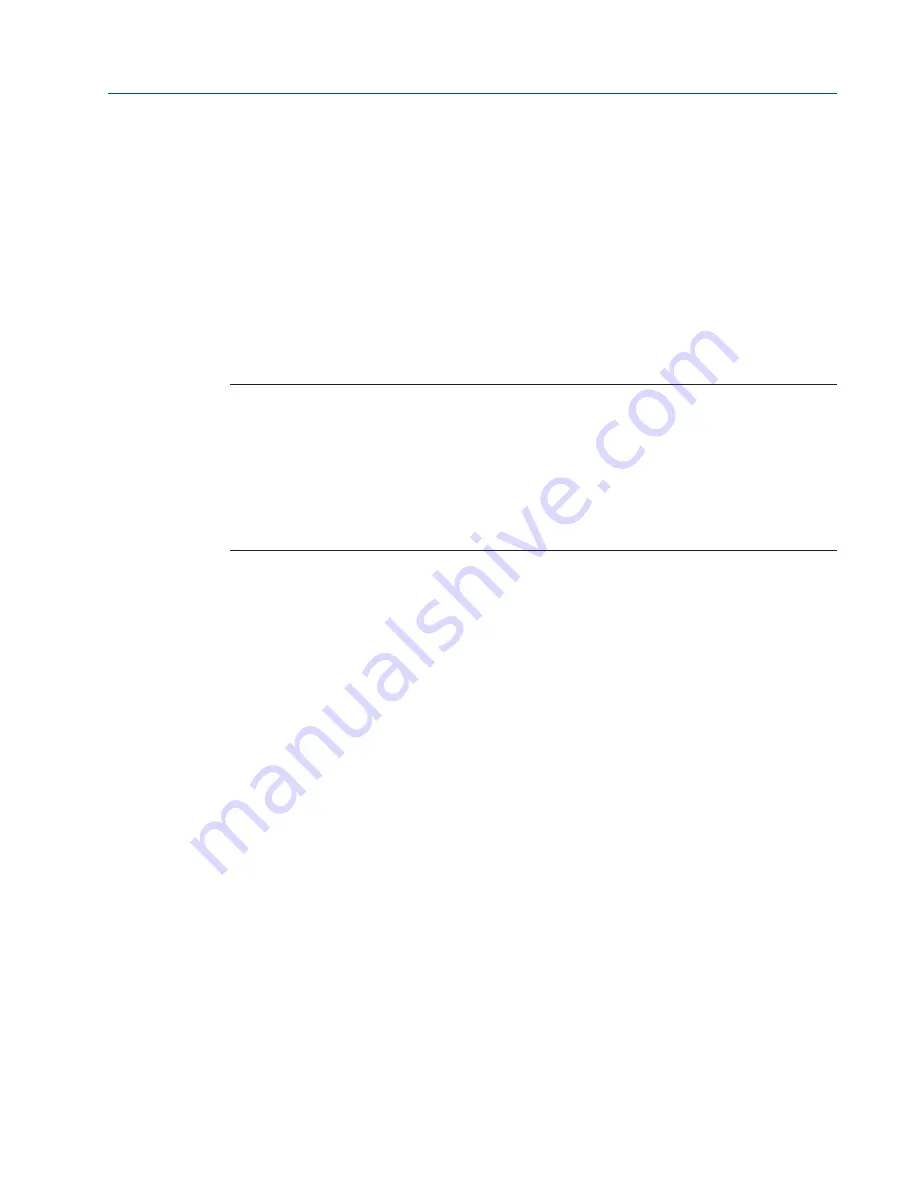
CAM216/16 IOM
Doc. Number: ECM-402-0116
January 2016, Rev. 1
63
Section 10: Miscellaneous
Miscellaneous
If the actuator is in analog control mode, you must use the configured Analog Input
designated for control, and supply a signal of 4mA (0%) to close and 20mA (100%)
to open.
The M2CP actuator is not polarity sensitive for HART communications, but it is polarity
sensitive for analog control purposes. Hence incorrect connection of the analog
current cables will not allow a host to control the position of the actuator.
10.1.4
Using the Local Control Station (if equipped)
This section provides information as to the status indications received from the
actuator when the actuator is equipped with a Local Control Station.
When the Local Control Station is used, placing the LOR selector switch in the Local/
Manual position on the control panel will cause the "Local Override” status in the
Actuator Status parameter to become true.
NOTE:
The Local Control Station has priority over all control sources. When equipped and activated,
no other control sources, including HART, can control the actuator until the Local Control Sta-
tion selector switch is returned to the “Remote/Auto” position, returning control to the other
“electronic” control means.
The Local Control Station has two sets of controls; 1) LOR selector switch with three (3)
positions (Local/Manual, OFF, and Remote/Auto) and 2) Control push-buttons with three
(3) buttons (Open, Stop, and Close).
Procedure is as follows –
•
Change the LOR selector switch position (mode) to (L) "Local/Manual".
•
Move the actuator to the desired position using the Open, Stop, or Closed
push buttons.
•
When the actuator has moved to the desired position, return control to the HART
Interface by placing the LOR in “Remote/Auto” position.
•
At this point, the actuator will travel to its commanded position as specified via the
Setpoint or Actuator Command parameter.
10.1.5
Using Other Remote Control Means
This section provides information on remote control of the actuator by means other
than the HART Interface. The 320B controller within the actuator has two independent
communication channels. One channel is used by the HART Interface and the other
may be available to other configuration or remote control devices communicating on
the other channel with another protocol. Such devices include Emerson’s DCMlink, a
PC Windows-based software package.
The 320B controller may also be configured to accept control from other means such
as “discrete switch inputs” (pulse input mode) and “4-20mA control signal” (analog
control mode). Refer to Emerson Process Management Electric Actuator Quick Startup
Guide for wire connections and configuration setting of the 320B module.
When the actuator is configured to “Network” mode, it will be controlled by the digital
command sent from the control system to the value of SV (set point), or when in block mode,
to whichever open, close or stop command has been sent.
When the actuator is configured to “Analog Control” mode, the actuator will be controlled by
the input connected to Analog Input 1 channel (4-20mA) to indicate 0-100% once it has
been calibrated.