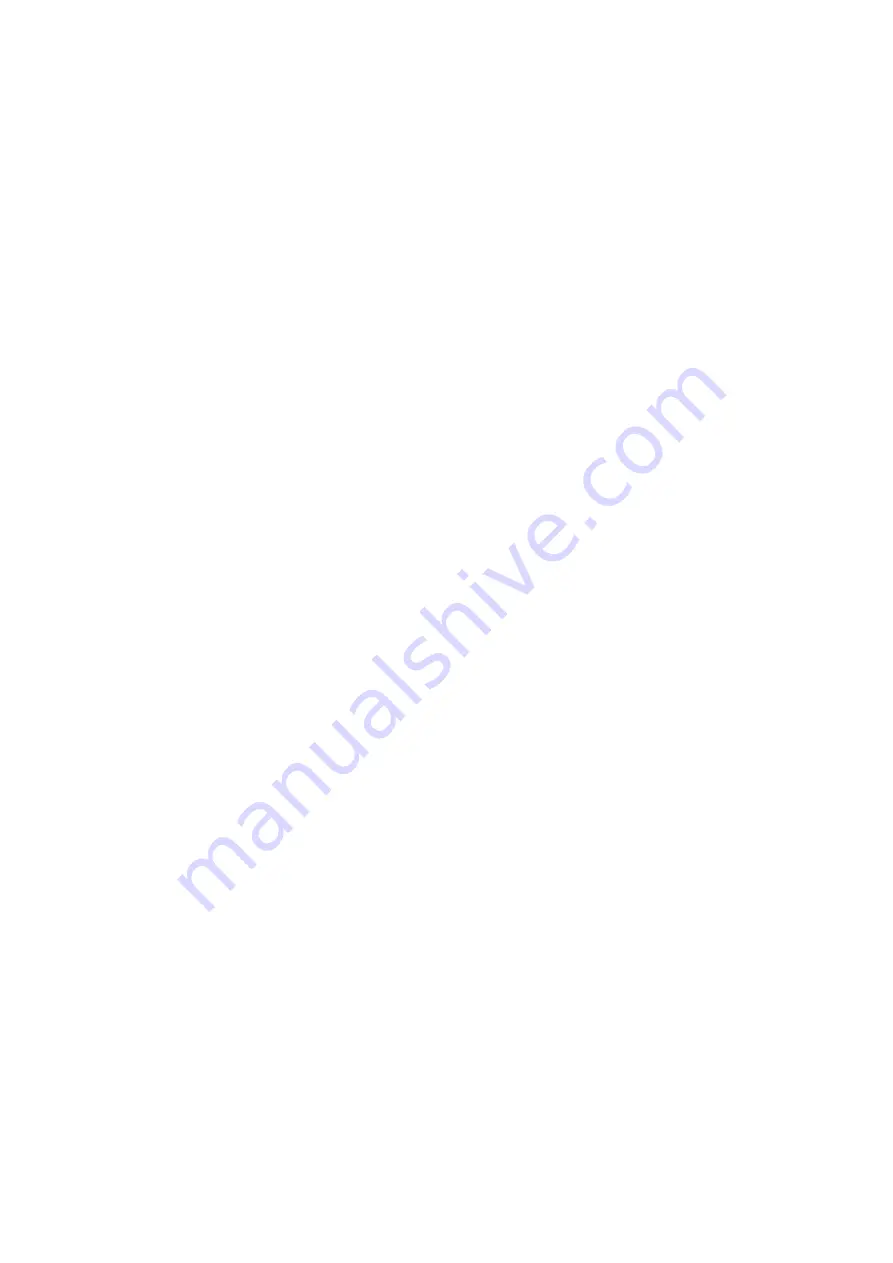
G-2
7) Insert a screwdriver into the space over Z-axis and check that Z-axis moves smoothly from the upper
limit to the lower limit.
8) Check that the helical coupling set between the Y-axis motor and the Y-axis ball screw, is tight.
(2)
Points to be checked after turning on the Power
1) Enter cutting data after turning on the power. Check brightness of microscope view and if adjustment is
necessary, refer to “Adjustment of Microscope Illumination Brightness” in the Operation Manual.
2) Remove the front cover and move X-axis manually from the right limit to the left limit to check the
machine for abnormal sound. Check that the timing belt is not broken.
3) Lift the main body cover and move Y-axis from the back limit to the front limit to check that water hose,
waterproof gum, press board, or the like are not pinched anywhere.
4) Check that the speed of the spindle reaches 30,000r.p.m. within five to ten seconds after turning it on
and that the spindle stops rotating three to six seconds after turning it off.
If adjustment is necessary, refer to “Adjustment of Spindle Motor Revolution” in the Operation Manual.
5) Remove the chuck table and turn on the VACUUM switch. Close the openings on the top surface of
rotary ring with a finger and the pointer of the vacuum meter should then deflect to the green zone. If it
deflects to the red zone, air pressure may be abnormal or the tubing may be broken.
Further check that there is no foreign matter in the “CONVUM”.
6) Be sure to check all functions listed above before operating the machine.
3.
Monthly Inspection, Maintenance and Adjustment
1)
Are the timing belts for the X-axis drives free from cracking, splitting anf other defects?
2)
Is the mist separater’s interval element dirty?
If the surface of the filter element has become red, please change the element (normal color is white).
Please inspect the air tubing, air dryer etc. When checking if there is any oil other contamination on the
inside wall of the sighting glass.
3)
Are all ducts and drainpipes clear and free from obstructions?
4.
Spindle Inspection
If oil, water or dirt get into the air being supplied to the spindle, a critical spindle malfunction will occur.
Therefore it is of the utmost importance to make sure that the compressor, air filters and air drier are
properly maintained. Prior to use, supply air to the spindle for several minutes, turning the shaft lightly with
your fingers. This will detect unusual spindle operation and also help to remove moisture from the spindle.
If in manually rotating the spindle you feel it binding and not tuning smoothly, remove the bearing air
connector and inject several cc of fleon 113 into the hose. After reconnecting the hose, blow air through it.
This will effectively remove oil and dirt from around the spindle shaft. If this operation is repeated several
times without any effect, special disassembly and cleaning will be required. Please contact our local service
office about this.
880930
Summary of Contents for DAD 2H/6T
Page 5: ...INTRODUCTION...
Page 7: ...A GENERAL...
Page 9: ...B CONSTRUCTION...
Page 11: ...B 2 2 Composition and Arrangement of Electrical Equipment Fig B 2 910810 910810...
Page 12: ...B 3 891110 3 Pneumatic Water Schematic Diagram Fig B 3 891110...
Page 13: ...C CIRCUIT DIAGRAM...
Page 16: ......
Page 17: ......
Page 18: ......
Page 20: ......
Page 21: ......
Page 22: ......
Page 23: ......
Page 24: ......
Page 25: ......
Page 26: ......
Page 28: ......
Page 30: ......
Page 32: ......
Page 33: ......
Page 34: ......
Page 35: ......
Page 36: ......
Page 37: ......
Page 38: ......
Page 39: ......
Page 40: ......
Page 41: ......
Page 42: ......
Page 44: ......
Page 46: ......
Page 48: ......
Page 50: ......
Page 51: ......
Page 52: ......
Page 54: ......
Page 56: ......
Page 58: ......
Page 60: ......
Page 61: ......
Page 62: ......
Page 64: ......
Page 65: ......
Page 66: ......
Page 68: ......
Page 69: ......
Page 70: ......
Page 72: ...EAUA 087600...
Page 74: ...EAUA 087703...
Page 76: ...EAUA 087800 X Y EAUA 087900 Z...
Page 78: ...EAUA 023600...
Page 81: ...D MAINTENANCE...
Page 83: ...E CHECKING PROCEDURES FOR TROUBLESHOOTING...
Page 110: ...E 27 Fig E 3 Output Waveform of Driver P C Board 840920...
Page 117: ...F ILLUSTRATION AND PARTS LIST...
Page 118: ...EXPLODED VIEW OF MAIN BODY A F 1...
Page 124: ...EXPLODED VIEW OF MAIN BODY B F 2...
Page 128: ...EXPLODED VIEW OF X AXIS 90 THETA F 3A...
Page 134: ...EXPLODED VIEW OF X AXIS MANUAL THETA F 3B MODEL DAD 2H 6TM...
Page 137: ...MEMO...
Page 138: ...EXPLODED VIEW OF X AXIS 360 THETA F 3C...
Page 141: ...MEMO...
Page 142: ...EXPLODED VIEW OF X AXIS F 3D MODEL DAD 2H 6T...
Page 144: ...EXPLODED VIEW OF Y AXIS F 4...
Page 148: ...EXPLODED VIEW OF Z AXIS F 5...
Page 154: ...EXPLODED VIEW OF PIPING A F 6...
Page 156: ...EXPLODED VIEW OF PIPING B F 7...
Page 165: ...G REGULAR INSPECTIONS...
Page 169: ...H CAMERA HEAD MONITOR TV...
Page 174: ...H 5 External Operating Unit Fig H 2 910110...
Page 175: ...H 6 Camera Head Internal Adjusters VIDEO PWB Fig H 3 891110...
Page 176: ...H 7 Monitor Internal Adjuster PROCESS PWB 891110 Fig H 4...
Page 177: ...H 8 Internal Monitor Adjusters MONITOR PWB 891110 Fig H 5...
Page 178: ...H 9 Internal Monitor Adjuster POWER SUPPLY PWB Fig H 6 891110...
Page 179: ...J MICROSCOPE MODEL DS...