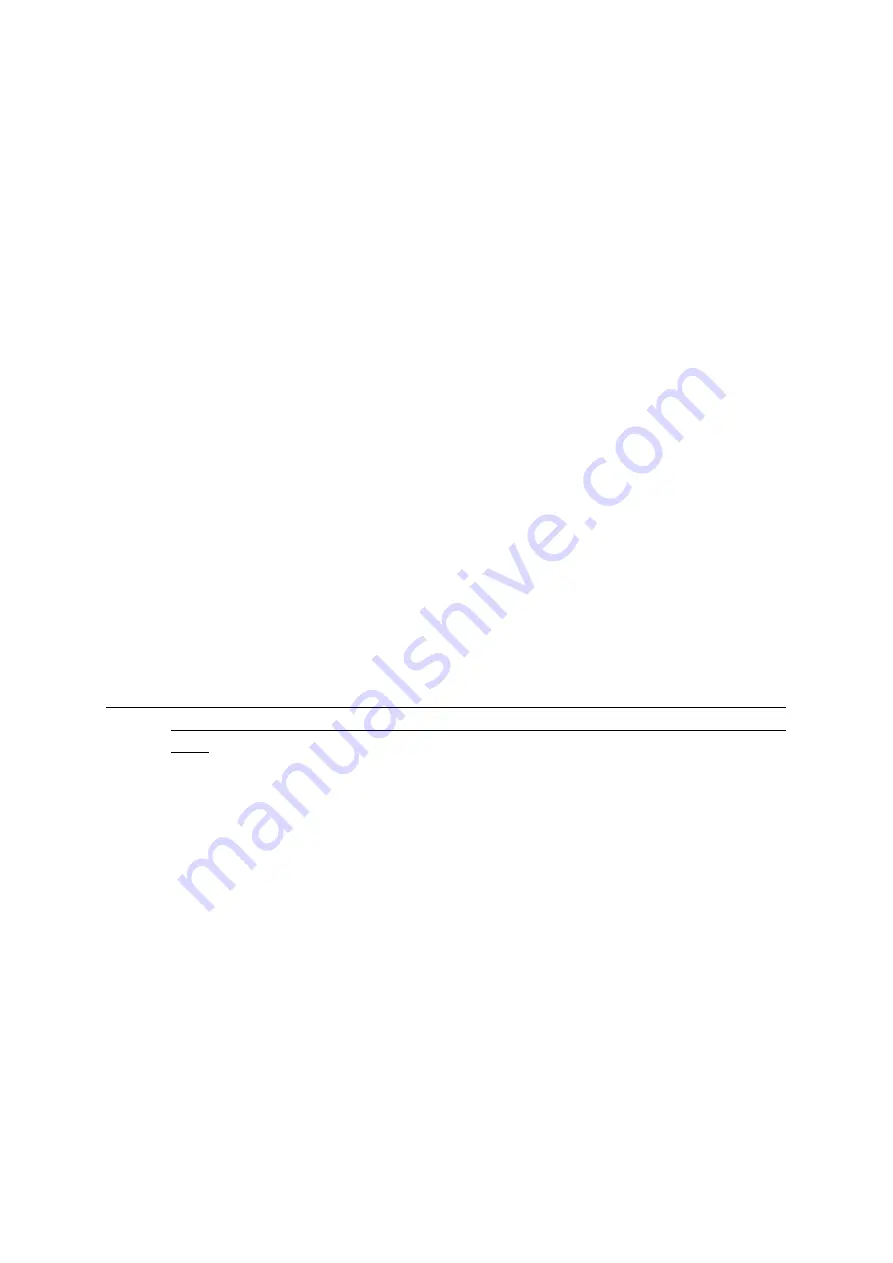
G-1
G. REGULAR INSPECTIONS
1.
Daily Inspection, Maintenance and Adjustment
(1)
Point to be checked before turning on the Power
1) The air pressure is 5.0kgf/cm
2
G-71 P.S.I. or more.
2) There is no foreign matter in the hose.
3) Does the air spindle shaft revolve freely ?
4) Is the flange not marked with cutlery tooth, scratched, or contaminated ?
5) That the chuck table is not contaminated or scratched.
6) There is no hit mark, contamination, dust or rust between the chuck table and rotary disk.
7) Is 90
°
revolving operation smoothly performed ?
8) Did the present operator receive sufficient information on the current situation of the machine from the
preceding operator ?
(2)
Points to be checked after turning on the Power
1) Try and enter necessary data by number keys.
2) That Z-axis moves upward to the limit by EM operation.
3) (Not Assigned)
4) There is no back flow in the drainage hose.
5) There is no abnormal sound or vibration with SPINDLE switch turned on.
6) Is the nozzle cover set in parallel with the chuck table after setting-up operation ?
(3)
Final Inspection after completion of operation
1) Remove the front wheel cover and clean the surface of the acrylic plate.
2) Remove the chuck table for cleaning off water and dust.
3) Clean the top surface of the rotary disk and make sure it is dry.
4) Clean the inside of the water case with a paper towel and blow it out using a compressed air nozzle.
5) Clean the strainer.
Caution:
Before shutting down the equipment (and turning off air flow), run each spindle for 5-15 minutes
with the cutting water turned on; and 15-20 minutes with it off. (Do not turn off spindle coolant
water)
2.
Weekly Inspection, Maintenance and Adjustment
(1)
Points to be checked before turning on the Power
1) Ensure that the voltage is within the range of 3 phase AC 200V
±
10 %.
2) The air pressure 5.0kgf/cm
2
G-71 P.S.I.G or more.
3) The water pressure is 3kg/cm
2
-43 P.S.I. or more, or the water flow rate is 6.5 L/min-1.6 G.P.M. or more.
The difference in temperature between the inside and outside is 2
°
C or less.
4) There is no leakage inside or outside the main machine body.
5) Is there no electrical contact between the spindle shaft and main body.
6) (Not Assigned)
910810
Summary of Contents for DAD 2H/6T
Page 5: ...INTRODUCTION...
Page 7: ...A GENERAL...
Page 9: ...B CONSTRUCTION...
Page 11: ...B 2 2 Composition and Arrangement of Electrical Equipment Fig B 2 910810 910810...
Page 12: ...B 3 891110 3 Pneumatic Water Schematic Diagram Fig B 3 891110...
Page 13: ...C CIRCUIT DIAGRAM...
Page 16: ......
Page 17: ......
Page 18: ......
Page 20: ......
Page 21: ......
Page 22: ......
Page 23: ......
Page 24: ......
Page 25: ......
Page 26: ......
Page 28: ......
Page 30: ......
Page 32: ......
Page 33: ......
Page 34: ......
Page 35: ......
Page 36: ......
Page 37: ......
Page 38: ......
Page 39: ......
Page 40: ......
Page 41: ......
Page 42: ......
Page 44: ......
Page 46: ......
Page 48: ......
Page 50: ......
Page 51: ......
Page 52: ......
Page 54: ......
Page 56: ......
Page 58: ......
Page 60: ......
Page 61: ......
Page 62: ......
Page 64: ......
Page 65: ......
Page 66: ......
Page 68: ......
Page 69: ......
Page 70: ......
Page 72: ...EAUA 087600...
Page 74: ...EAUA 087703...
Page 76: ...EAUA 087800 X Y EAUA 087900 Z...
Page 78: ...EAUA 023600...
Page 81: ...D MAINTENANCE...
Page 83: ...E CHECKING PROCEDURES FOR TROUBLESHOOTING...
Page 110: ...E 27 Fig E 3 Output Waveform of Driver P C Board 840920...
Page 117: ...F ILLUSTRATION AND PARTS LIST...
Page 118: ...EXPLODED VIEW OF MAIN BODY A F 1...
Page 124: ...EXPLODED VIEW OF MAIN BODY B F 2...
Page 128: ...EXPLODED VIEW OF X AXIS 90 THETA F 3A...
Page 134: ...EXPLODED VIEW OF X AXIS MANUAL THETA F 3B MODEL DAD 2H 6TM...
Page 137: ...MEMO...
Page 138: ...EXPLODED VIEW OF X AXIS 360 THETA F 3C...
Page 141: ...MEMO...
Page 142: ...EXPLODED VIEW OF X AXIS F 3D MODEL DAD 2H 6T...
Page 144: ...EXPLODED VIEW OF Y AXIS F 4...
Page 148: ...EXPLODED VIEW OF Z AXIS F 5...
Page 154: ...EXPLODED VIEW OF PIPING A F 6...
Page 156: ...EXPLODED VIEW OF PIPING B F 7...
Page 165: ...G REGULAR INSPECTIONS...
Page 169: ...H CAMERA HEAD MONITOR TV...
Page 174: ...H 5 External Operating Unit Fig H 2 910110...
Page 175: ...H 6 Camera Head Internal Adjusters VIDEO PWB Fig H 3 891110...
Page 176: ...H 7 Monitor Internal Adjuster PROCESS PWB 891110 Fig H 4...
Page 177: ...H 8 Internal Monitor Adjusters MONITOR PWB 891110 Fig H 5...
Page 178: ...H 9 Internal Monitor Adjuster POWER SUPPLY PWB Fig H 6 891110...
Page 179: ...J MICROSCOPE MODEL DS...