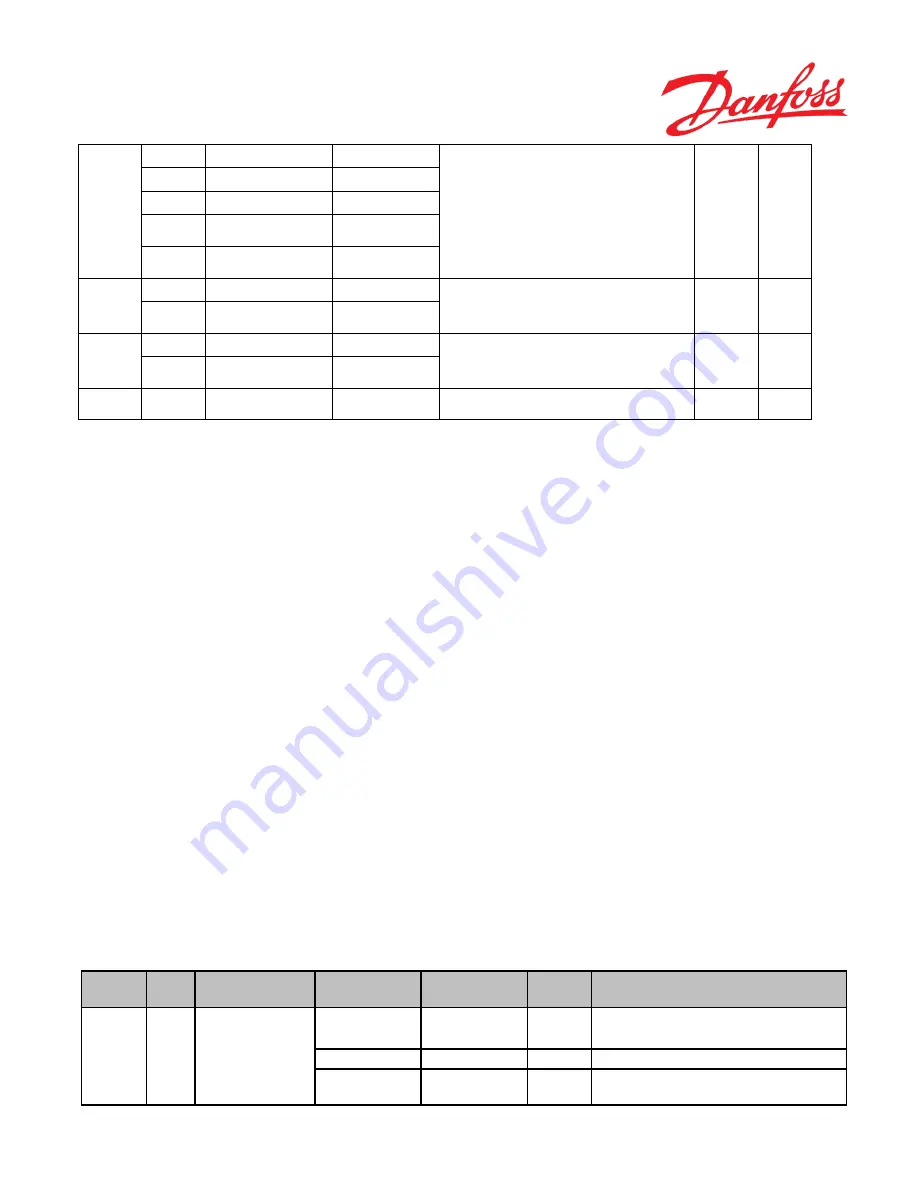
142 | © Danfoss | August 2018
AQ00000211
ENGINEERING TOMORROW
24
3426
Maximum steer angle, left
Vehicle Geometry
If WAS interface (P3244) = CAN:
Maximum steer angle, left (P3426)≤ 89 & Maximum steer angle,
right (P3428)≤ 89, Or
Automatically adjusted maximum steer angle to left side (CAN
WAS) (P3193)≤ 89 & Automatically adjusted maximum steer
angle to right side (CAN WAS) (P3195) ≤ 89
520241
2
3428
Maximum steer angle, right
Vehicle Geometry
3244
WAS interface
Peripherals Config
3193
Automatically adjusted
maximum steer angle to left
side (CAN WAS)
CAN WAS Calibration
Data
3195
Automatically adjusted
maximum steer angle to right
side (CAN WAS)
CAN WAS Calibration
Data
25
3086
Cylinder stroke volume
Hydraulic Config
If WAS interface (P3244) = ANALOG: Cylinder stroke volume
(P3086) ≤ 10000 Or
Automatically adjusted cylinder stroke volume (analogue WAS)
(P3221) ≤ 10000
520232
2
3221
Automatically adjusted
cylinder stroke volume
(analogue WAS)
Analog Sensor
Calibration Data
26
3086
Cylinder stroke volume
Hydraulic Config
If WAS interface (P3244) = CAN: Cylinder stroke volume
(P3086)≤ 10000 Or
Automatically adjusted cylinder stroke volume (CAN WAS)
(P3191) ≤ 10000
520232
2
3191
Automatically adjusted
cylinder stroke volume (CAN
WAS)
CAN WAS Calibration
Data
27
3297
PVED-CLS source address
SEHS Protocol Data
A warning shall be displayed when same source addresse is set
for Main and Safety controllers
17.2
ERROR CODES
J1939-73 DM1, DM2 and DM3 diagnostic protocol is supported.
The list of DTC is divided in 7 sections:
1.
I/O signals:
This sections lists all failures related to analogue and digital inputs & outputs
2.
CAN Messages:
This Section lists all failures related to CAN messages
3.
Safety Functions:
This Section lists all failures caused by Safety functions and externally triggered safe state
DTC’s
4.
Diagnostic functions:
This section lists all failures detected by diagnostic functions
5.
Internal Hardware:
This section lists all failures found on the internal PCB in PVED-CLS
6.
Software:
This section lists all failures detected inside the software
7.
Monitoring:
This section lists all failures detected by crosscheck input signal and calculation results on SPI
between main and Safety UC
Category
SPN
Signal Name
Failure mode
FMI
Severity
Possible root cause(s)
I/O Signals
520192
Analogue sensor connected to
AD1
Short circuit to GND
4 - Voltage below normal or short-
circuit to low source
Severe
1.
Wire connected to AD1 lost connection (open circuit).
2.
Wire connected to AD1 short circuit to GND.
Short circuit to VCC
3 - Voltage above normal or short-
circuit to high source
Severe
1.
Wire connected to AD1 short circuit to a source higher than 4.9V.
Too high deviation
25 - Signal crosscheck failed
Severe
1.
Wheel angle sensors are not calibrated properly.
2.
Sensor characteristics have changed.
3.
If two physical separated sensors are used, one of them has lost the
mechanical connection or has increased hysteresis
Summary of Contents for PVED-CLS
Page 6: ...6 Danfoss August 2018 AQ00000211 ENGINEERING TOMORROW ...
Page 71: ... Danfoss August 2018 AQ00000211 71 ENGINEERING TOMORROW Figure 29 ...
Page 127: ... Danfoss August 2018 AQ00000211 127 ENGINEERING TOMORROW ...
Page 147: ... Danfoss August 2018 AQ00000211 147 ENGINEERING TOMORROW ...
Page 182: ...182 Danfoss August 2018 AQ00000211 ENGINEERING TOMORROW ...