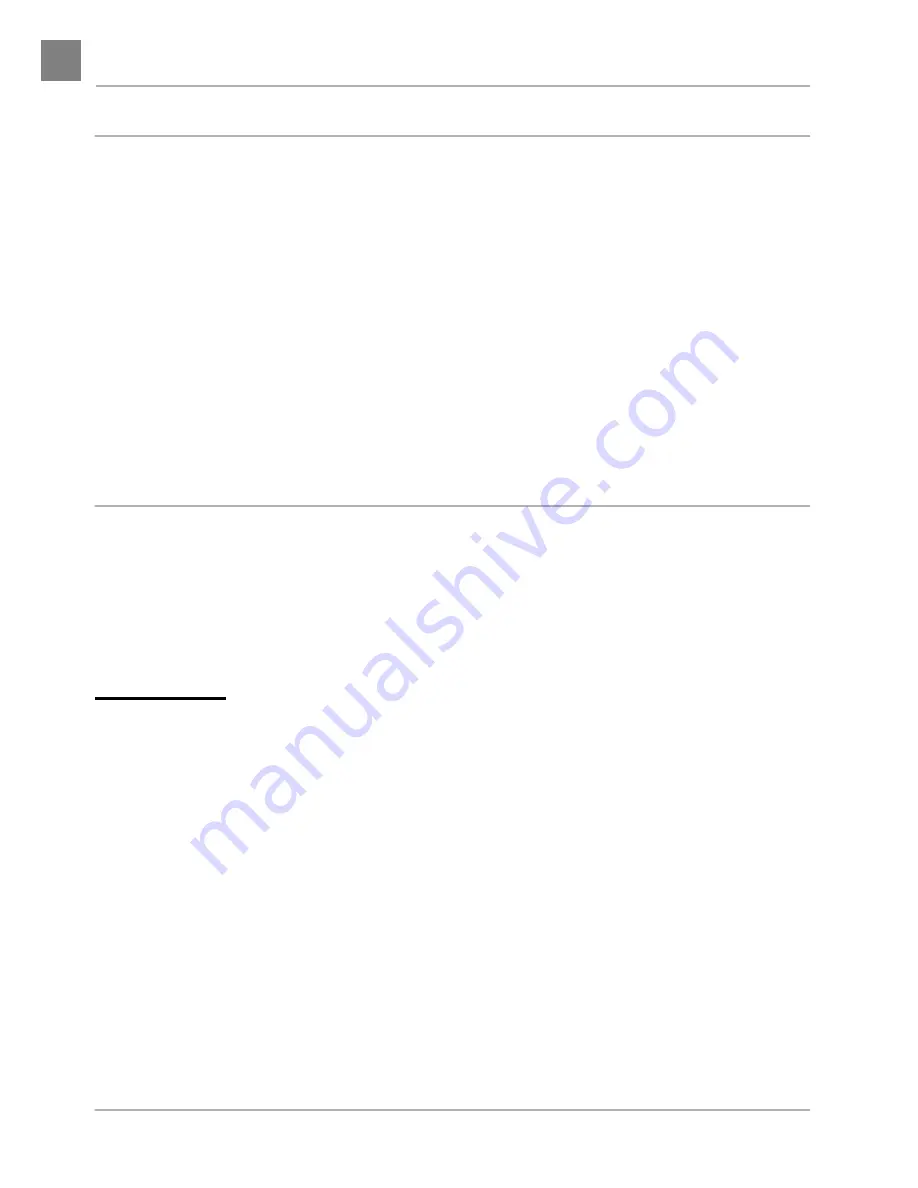
UNITIZED TRANSAXLE WITH DIFFERENTIAL LOCK
Unitized Transaxle Component Inspection
Page 16-26 2001 Pioneer 1200 Gasoline Vehicle Maintenance and Service Manual
16
UNITIZED TRANSAXLE COMPONENT INSPECTION
Read DANGER and WARNING on page 16-1.
1. Clean all of the component parts of the transaxle in a high flash-point solvent and then dry them.
Inspect all components for excessive wear or damage.
2. Inspect all bearings by spinning them by hand. Check the bearings for excessive axial (A) and radial
(B) play (Figure 16-59, Page 16-25). Replace bearings if they do not spin smoothly, if they are noisy, or
if they have excessive play. Replace bearings if they are rusted, worn, cracked, pitted, or discolored.
3. Gears should be inspected for tooth surface damage or fractures.
4. Synchronizer ring teeth should be inspected for severe wear, fractures, or other damage.
5. Using a feeler gauge, measure the distance X at several points around the assembly. The synchro ring
should be replaced when X is 0.02 inch (0.5 mm) or less (Figure 16-60, Page 16-25).
6. Inspect the O-ring (96) on the differential lock shaft (Figure 16-47, Page 16-19).
COMPONENT ASSEMBLY
Read DANGER and WARNING on page 16-1.
IDLER SHAFT ASSEMBLY
1. Press a new bearing (69) (Figure 16-48, Page 16-20) onto each end of the idler shaft (Figure 16-61,
Page 16-25). See following CAUTION.
∆ CAUTION
• Apply pressure against the inner race of the bearing only. Applying pressure anywhere else will
damage the bearing.
INTERMEDIATE GEAR ASSEMBLY
1. If the gear (61) was removed from the shaft, install the key (60) into the slot and then position the gear
on the shaft with keyway properly aligned with key. Press gear into place on the key (Figure 16-48,
Page 16-20).
2. Press the bearing (62) onto the end of the shaft next to the large gear that was installed in step 1 (Fig-
ure 16-48, Page 16-20). See preceding CAUTION.
3. Press a new bearing (41) onto the other end of the shaft (Figure 16-48, Page 16-20).
SYNCHRONIZER GEAR ASSEMBLY
1. Press the synchronizer sleeve (50) onto the splines of the input shaft (54) (Figure 16-48, Page 16-20).
No particular orientation of the sleeve is necessary, but toward the short end of the shaft, the machined
circular face surrounding the ends of the internal splines in the sleeve must be flush with the machined
lip of the shaft at the ends of the shaft splines (Figure 16-62, Page 16-27).