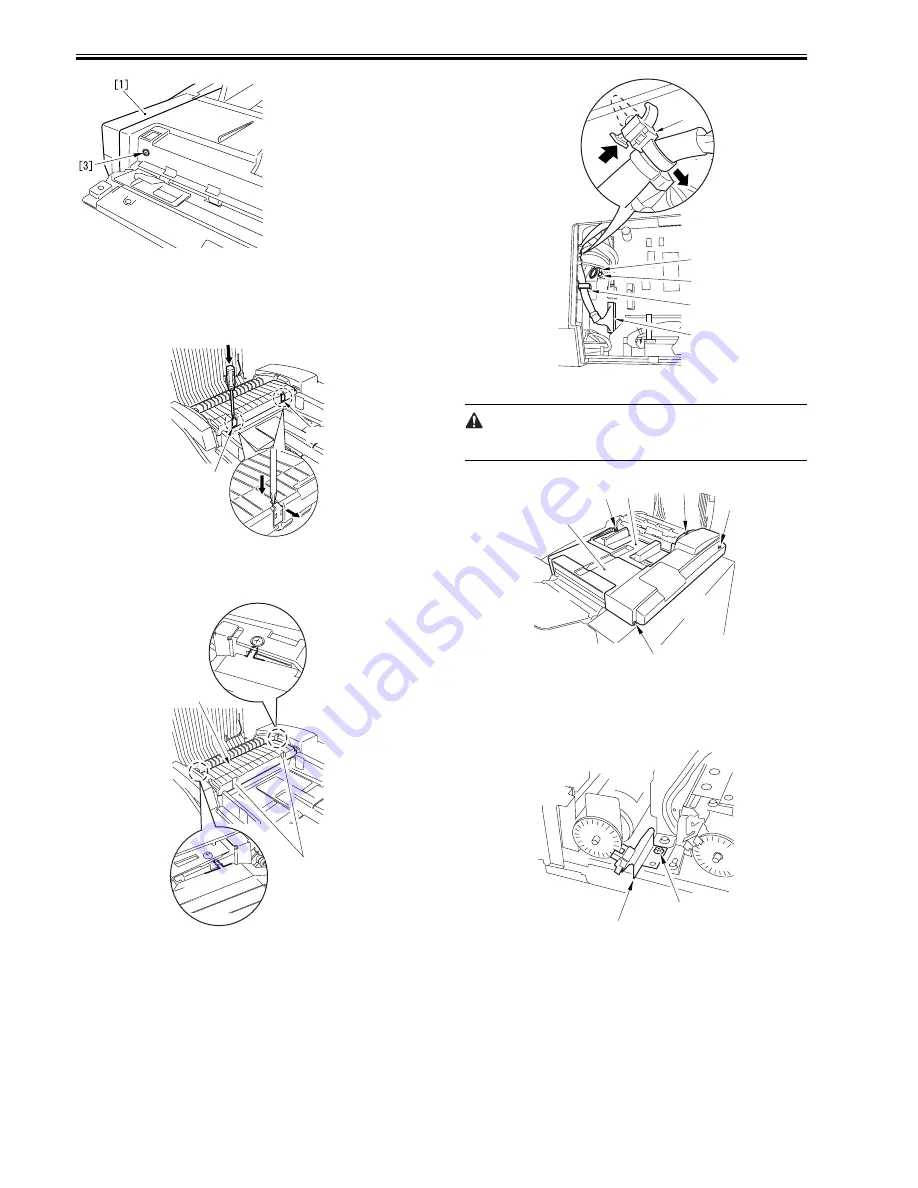
Chapter 3
3-4
F-3-22
3.3.2.2 Removing the Main Cover
0011-8130
1) Open the upper cover, and insert a screwdriver from above the hook; then,
remove the two hooks [1].
F-3-23
2) Free the hook of the pickup assembly cover [2] from the right stay; then,
detach it while paying attention to the hooks on the front and rear side
plates.
F-3-24
3) When you have removed the ADF controller cover, disconnect the con-
nector [3] of the ADF controller PCB; then, remove the screw [4], and re-
move the grounding wire [5]. Free the harness from the wire saddle [6],
and detach the other saddle [7].
F-3-25
4) Remove the four screws [1], and detach the main cover [2].
The main cover is fitted with the original tray [3], and cables are connected
to it. Take extra care when removing it not to damage the cables.
F-3-26
3.3.2.3 Removing the Separation Motor Unit
0011-8131
1) Remove the screw [1], and detach the separation motor sensor support
plate [2].
F-3-27
2) Disconnect the two connectors [1].
[1]
[1]
[2]
Hooks
Push.
Freed.
[5]
[7]
[4]
[6]
[3]
[1]
[1]
[1]
[1]
[3]
[2]
[2]
[1]
Summary of Contents for DADF-Q1
Page 1: ...Aug 24 2007 Service Manual Feeder DADF Q1 ...
Page 2: ......
Page 6: ......
Page 11: ...Chapter 1 Specifications ...
Page 12: ......
Page 14: ......
Page 18: ......
Page 19: ...Chapter 2 Functions ...
Page 20: ......
Page 22: ......
Page 75: ...Chapter 3 Parts Replacement Procedure ...
Page 76: ......
Page 107: ...Chapter 4 Maintenance ...
Page 108: ......
Page 149: ...Chapter 5 Error Code ...
Page 150: ......
Page 152: ......
Page 154: ......
Page 155: ...Aug 24 2007 ...
Page 156: ......