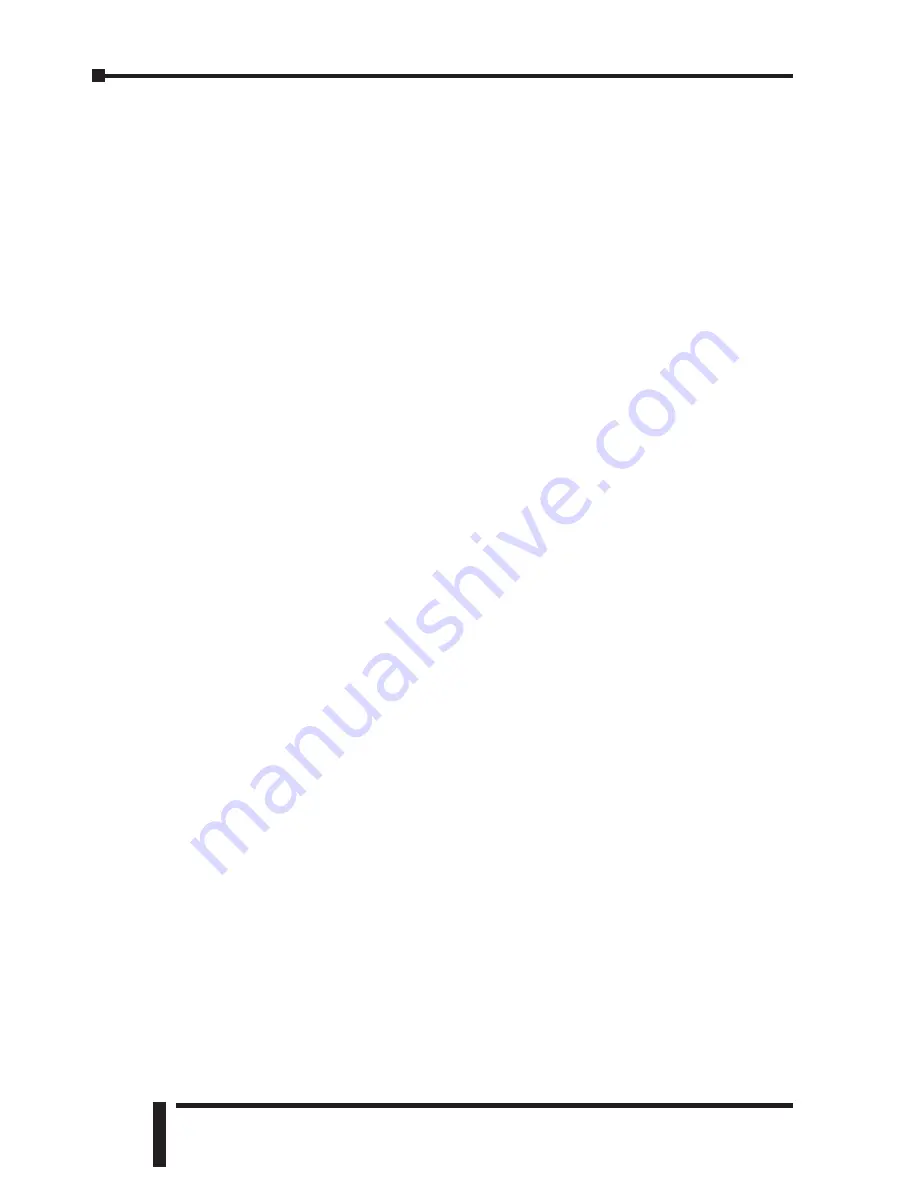
1st Ed. Rev. D 05/2013
DURA
PULSE
AC Drive User Manual
Communication Delay Summary
Now that you know how to calculate the time required for one message to one
GS drive, you would simply multiply this value per message to each GS drive on
the network, since only one message can be sent at a time.
As you can deduce from the statement above, the more messages being sent to
GS drives, the longer it takes to communicate to an individual drive as each
message has to take its turn.
So how do you optimize your communications to get messages faster to your GS
drives?
There is no way to make a message go faster than what is specified above, but
what you can affect is the amount of messages being sent to any given GS drive in
two ways.
1) Group together messages into Block requests whenever possible. For example, if
you wanted to read Status Monitor 1 and the Output Frequency status register
from the drive, read the two together as a block (Status Monitor 1, Status Monitor
2, Frequency Command and Output Frequency), and ignore the other two status
registers that you don’t need instead of sending two separate read commands. If
you do the calculations above, you will see that is much faster to take the
additional hit from four extra bytes in the reply message than it would be to send
a separate message. NOTE that you cannot read across non-contiguous Modbus
addresses, so this typically only works when reading within the Status registers or
in a Parameter category (P9.xx, P1.xx, etc…).
2) Only send a write message when the value changes in the Master device. It is
simpler to setup your communications instructions to read and write all the time,
but it wastes precious network time to write the same value to the GS drive over
and over if that value is not changing. Write some simple logic that only triggers a
write command when the value to be sent has changed.
For more specific instructions on how to configure and/or interlock, in detail, the
individual communications instructions, consult your PLC or Modbus Master
Device user manual. If using DirectLogic PLCs as the Modbus Master, consult the
Dx-USER-M manuals for specifics on configuring the individual communications
instructions and look at the Hx-ECOM-M manual for information on interlocking
communications instructions.
5–78
Chapter 5:
DURA
PULSE
MODBUS Communications
Summary of Contents for DURAPULSE GS3-2010
Page 1: ...230V Class 1 50 Hp 460V Class 1 100 Hp User Manual AC Drive...
Page 2: ......
Page 6: ...w 4 DURAPULSE AC Drive User Manual 1st Ed Rev D 05 2013...
Page 8: ...Revision History DURAPULSE AC Drive User Manual h 2 BLANK PAGE...
Page 148: ...Chapter 4 AC Drive Parameters 4 80 DURAPULSE AC Drive User Manual 1st Ed Rev D 05 2013...
Page 241: ...DURAPULSE AC Drive User Manual A 1c Appendix A Accessories 1st Ed Rev D 05 2013...
Page 292: ...Appendix A Accessories DURAPULSE AC Drive User Manual A 52 BLANK PAGE 1st Ed Rev D 05 2013...
Page 314: ...Index i 8 DURAPULSE AC Drive User Manual 1st Ed Rev D 05 2013...
Page 315: ......
Page 316: ......