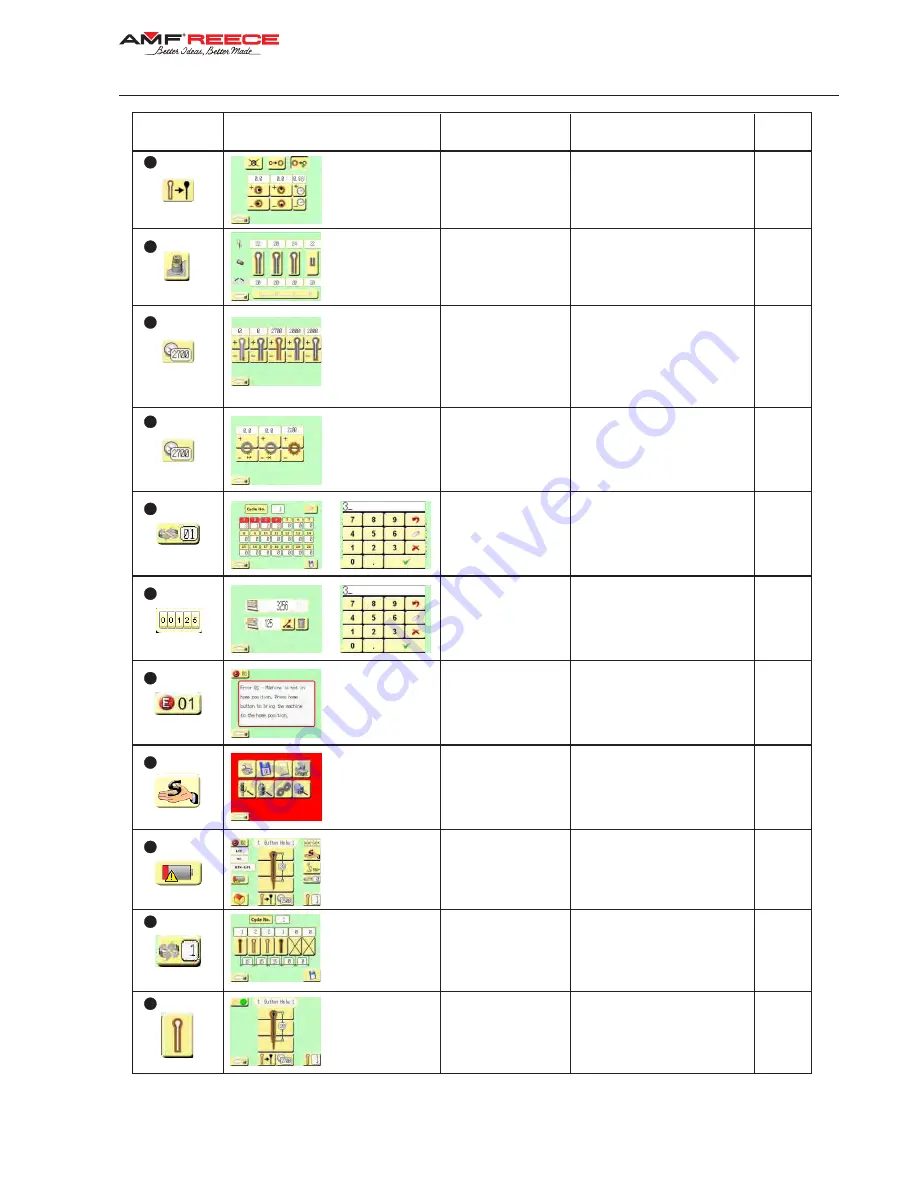
ES-505
1-33
Released: 01/2018
E-mail: [email protected]; webside: amfreece.com
Phone: +420 582 309 146; Fax: +420 582 360 606
D - MACHINE CONTROLS
D 2.10.
D 2.5.
D 2.9.
7
9
9
10
11
12
Buttonhole sewing
speed parameters
Number of stitches sewn slowly
at the beginning of sewing
Sewing speed in the firs and
second raw of stitches
Sewing speed in the eye
Sewing speed in the bar
Round buttonhole
cutting parameters
screen
Cutting types
Correction of cut in X / Y axes
Cutting time delay
Round buttonhole
sewing speed screen
Error mesages screen
Current / following
screen
Button -
icon
Screen name -
icon name
Parameter setting
Chapter
Counter mode
Total machine productivity
Standard cycling
program screen
Error number
Error description
Instructions to eliminate errors
0
Cycling program from 1 to 47
Buttonhole program in chosen
cycling program
D3.1.
D3.2.
D 5.1.
D 5.2.
13
14
Service menu screen
Setting machine parameters/
for traines service
mechanics only
E2.1.
Productivity screen
Nuber of stitches sewn slowly at
the end of sewing
Number of stitches sewn slowly
at the beginning of sewing
Round buttonhole sewing speed
Over-sewing speed
Number of stitches sewn slowly
at the end of sewing
The main screen
Low battery alarm
15
16
Indexer cycle mode
screen
Number of cycle mode
Number of button hole
Distance between button hole
Button hole edit
screen
Button hole parameters
is possible to change according
describetion in section
D2.1-D2.7
8
Electronic thread
tension screen
(optional device)
Electronic thread tension
D 2.8.
D 5.3.
D 4.1.
D 4.3.