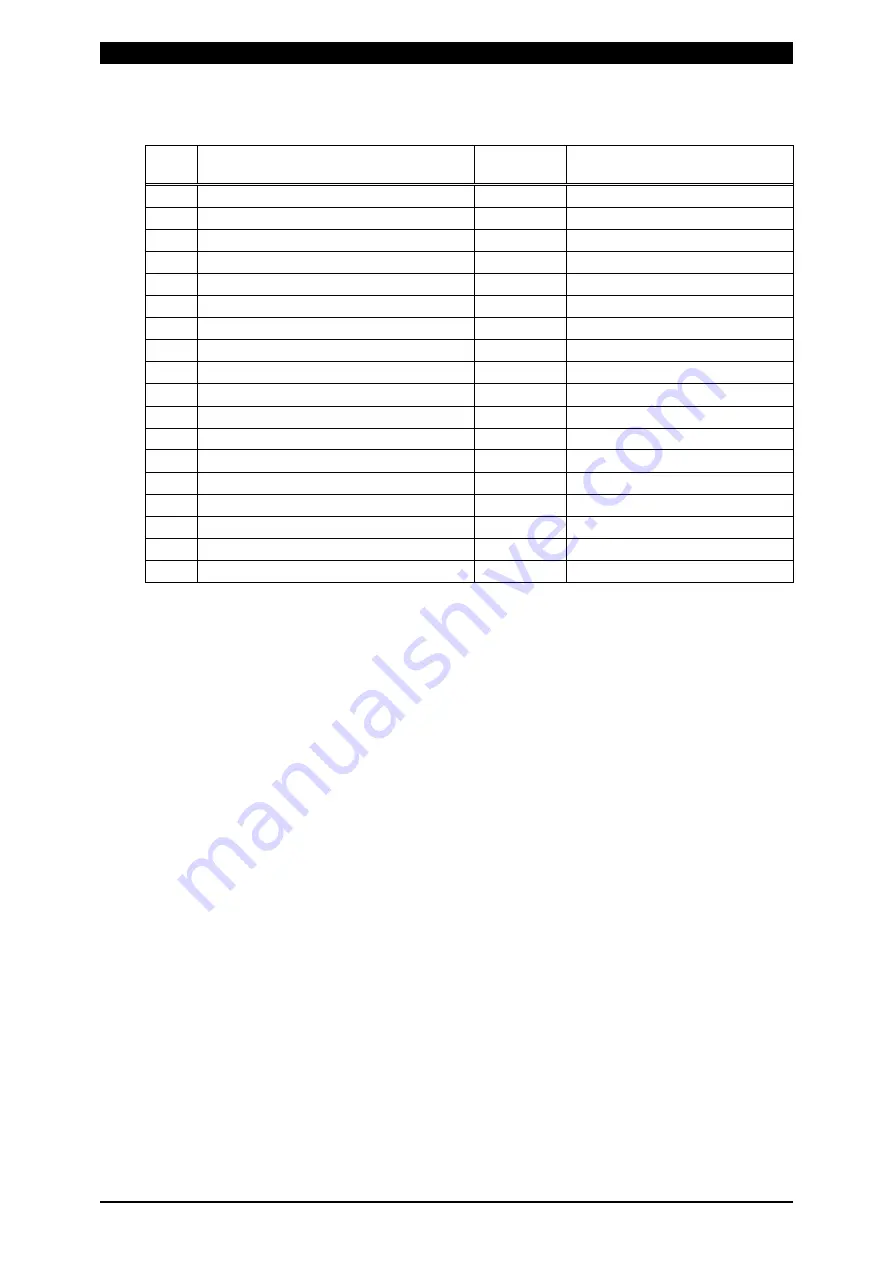
MEA-100B
14. External Communication Function
14-7
Screen 03 (Stepper data) Common data (Schedule No.: 00)
Item
Contents
Character
string
Range
1
SOL1 STEP1 Count
nnnn,
0000 to 9999
2
SOL1 STEP2 Count
nnnn,
0000 to 9999
3
SOL1 STEP2 Stepper Rate
nnn,
050 to 150 (%)
4
SOL1 STEP3 Count
nnnn,
0000 to 9999
5
SOL1 STEP3 Stepper Rate
nnn,
050 to 150 (%)
6
SOL1 STEP4 Count
nnnn,
0000 to 9999
7
SOL1 STEP4 Stepper Rate
nnn,
050 to 150 (%)
8
SOL1 STEP5 Count
nnnn,
0000 to 9999
9
SOL1 STEP5 Stepper Rate
nnn,
050 to 150 (%)
10
SOL2 STEP1 Count
nnnn,
0000 to 9999
11
SOL2 STEP2 Count
nnnn,
0000 to 9999
12
SOL2 STEP2 Stepper Rate
nnn,
050 to 150 (%)
13
SOL2 STEP3 Count
nnnn,
0000 to 9999
14
SOL2 STEP3 Stepper Rate
nnn,
050 to 150 (%)
15
SOL2 STEP4 Count
nnnn,
0000 to 9999
16
SOL2 STEP4 Stepper Rate
nnn,
050 to 150 (%)
17
SOL2 STEP5 Count
nnnn,
0000 to 9999
18
SOL2 STEP5 Stepper Rate
nnn
050 to 150 (%)