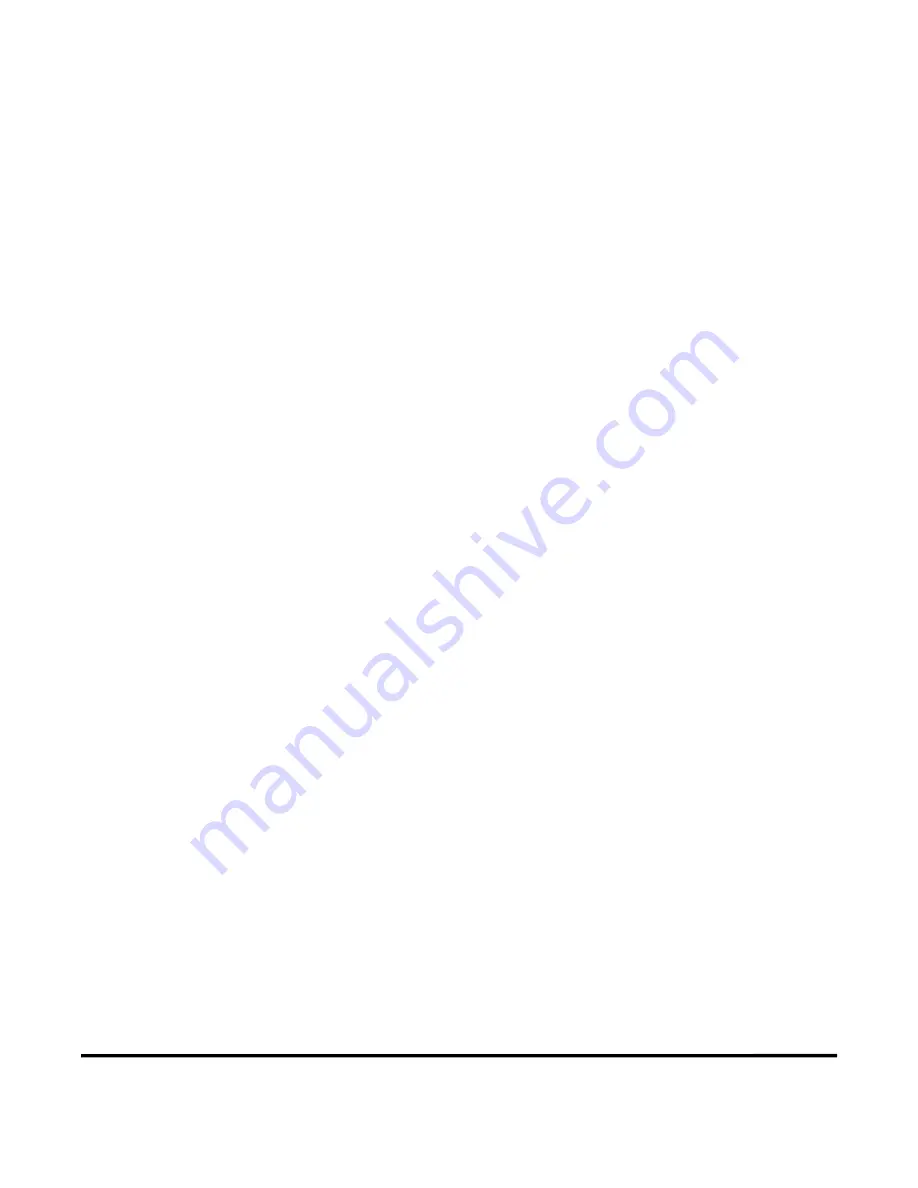
125ADP/300ADP/1000ADP DUAL PULSE RESISTANCE WELDING POWER SUPPLY
x
990-922
LIMITED WARRANTY
1. (a)
Subject to the exceptions and upon the conditions set forth herein, Seller warrants to Buyer that
for a period of one (1) year from the date of shipment (“
Warranty Period
”), that such Goods will be free
from material defects in material and workmanship.
(b)
Notwithstanding the foregoing and anything herein to the contrary, the warranty set forth in this
Section 1 shall be superseded and replaced in its entirety with the warranty set forth on
Exhibit A
hereto if the Goods being purchased are specialty products, which include, without limitation, laser
products, fiber markers, custom systems, workstations, Seller-installed products, non-catalogue
products and other custom-made items (each a “
Specialty Products.”
(c)
EXCEPT FOR THE WARRANTY SET FORTH IN SECTION 1(A), SELLER MAKES NO
WARRANTY WHATSOEVER WITH RESPECT TO THE GOODS (INCLUDING ANY SOFTWARE) OR
SERVICES, INCLUDING ANY (a) WARRANTY OF MERCHANTABILITY; (b) WARRANTY OF
FITNESS FOR A PARTICULAR PURPOSE; (c) WARRANTY OF TITLE; OR (d) WARRANTY
AGAINST INFRINGEMENT OF INTELLECTUAL PROPERTY RIGHTS OF A THIRD PARTY;
WHETHER EXPRESS OR IMPLIED BY LAW, COURSE OF DEALING, COURSE OF
PERFORMANCE, USAGE OF TRADE OR OTHERWISE.
(d)
Products manufactured by a third party and third party software (“
Third Party Product
”) may
constitute, contain, be contained in, incorporated into, attached to or packaged together with, the
Goods. Third Party Products are not covered by the warranty in Section 1(a). For the avoidance of
doubt,
SELLER MAKES NO REPRESENTATIONS OR WARRANTIES WITH RESPECT TO ANY
THIRD PARTY PRODUCT, INCLUDING ANY (a) WARRANTY OF MERCHANTABILITY; (b)
WARRANTY OF FITNESS FOR A PARTICULAR PURPOSE; (c) WARRANTY OF TITLE; OR (d)
WARRANTY AGAINST INFRINGEMENT OF INTELLECTUAL PROPERTY RIGHTS OF A THIRD
PARTY; WHETHER EXPRESS OR IMPLIED BY LAW, COURSE OF DEALING, COURSE OF
PERFORMANCE, USAGE OF TRADE OR OTHERWISE.
Notwithstanding the foregoing, in the event
of the failure of any Third Party Product, Seller will assist (within reason) Buyer (at Buyer’s sole
expense) in obtaining, from the respective third party, any (if any) adjustment that is available under
such third party’s warranty.
(e)
Seller shall not be liable for a breach of the warranty set forth in Section 1(a) unless: (i) Buyer gives
written notice of the defect, reasonably described, to Seller within five (5) days of the time when Buyer
discovers or ought to have discovered the defect and such notice is received by Seller during the
Warranty Period; (ii) Seller is given a reasonable opportunity after receiving the notice to examine such
Goods; (iii) Buyer (if requested to do so by Seller) returns such Goods (prepaid and insured to Seller at
1820 South Myrtle Avenue, Monrovia, CA 91016or to such other location as designated in writing by
Seller) to Seller pursuant to Seller’s RMA procedures and Buyer obtains a RMA number from Seller
prior to returning such Goods for the examination to take place; and (iii) Seller reasonably verifies
Buyer’s claim that the Goods are defective and that the defect developed under normal and proper use.
(f)
Seller shall not be liable for a breach of the warranty set forth in Section 1(a) if: (i) Buyer makes any
further use of such Goods after giving such notice; (ii) the defect arises because Buyer failed to follow
Seller’s oral or written instructions as to the storage, installation, commissioning, use or maintenance of
the Goods; (iii) Buyer alters or repairs such Goods without the prior written consent of Seller; or (iv)
repairs or modifications are made by persons other than Seller’s own service personnel, or an
authorized representative’s personnel, unless such repairs are made with the written consent of Seller
in accordance with procedures outlined by Seller.
Summary of Contents for 1000ADP
Page 1: ...990 922 Rev G STORED ENERGY POWER SUPPLY 125 300 1000ADP OPERATION MANUAL...
Page 8: ...125ADP 300ADP 1000ADP DUAL PULSE RESISTANCE WELDING POWER SUPPLY viii 990 922...
Page 9: ...125ADP 300ADP 1000ADP DUAL PULSE RESISTANCE WELDING POWER SUPPLY 990 922 ix...
Page 14: ......
Page 24: ......
Page 58: ......
Page 64: ......
Page 82: ......
Page 92: ......