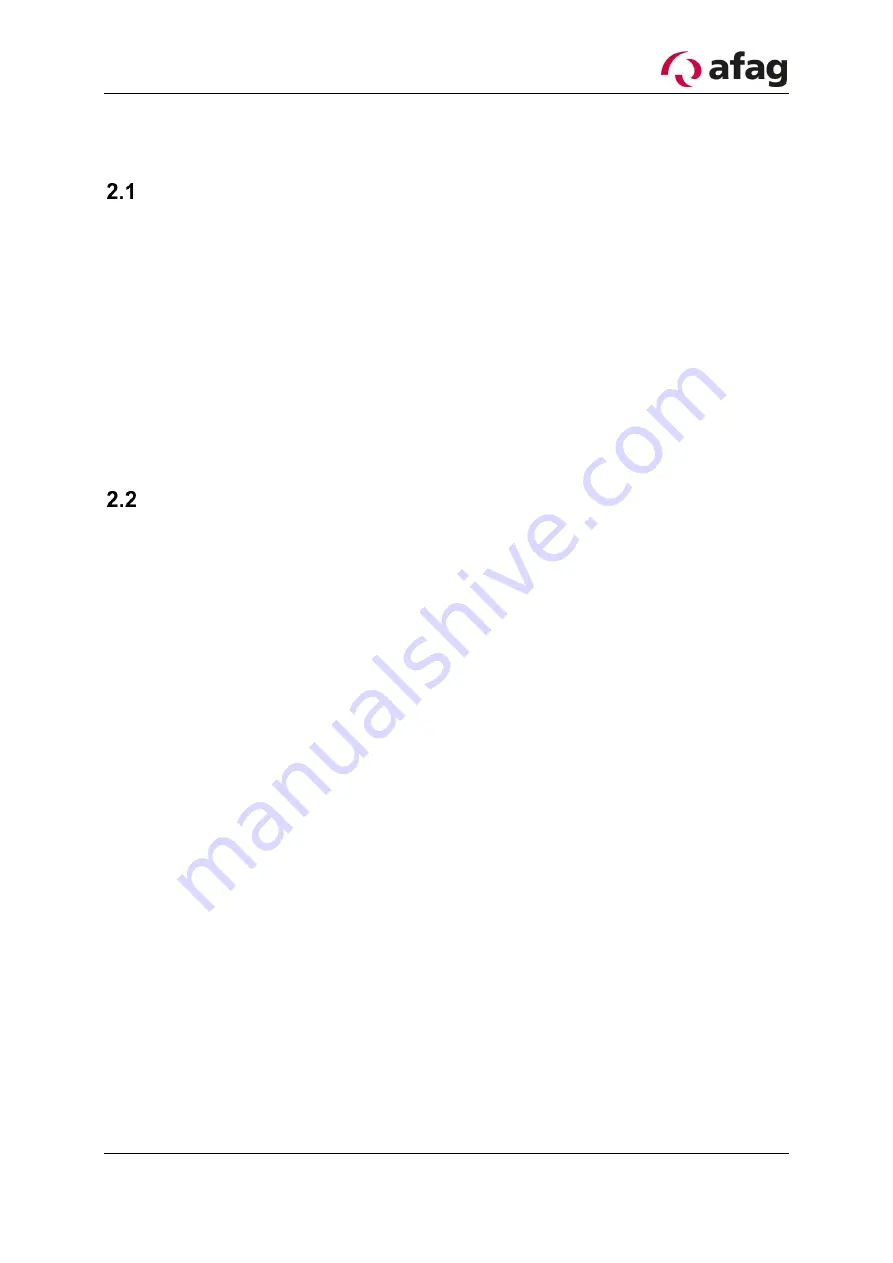
R01.43
22.10.2018
Page 11
2 Description of the device
General
The aflex system consists of an aflex and an external control system. This consists of
individual control modules. A ControlUnit and two drive modules are used in the stand-
ard configuration. Optionally, the control can be extended with additional field bus in-
terfaces.
The aflex control provides following interfaces for superior control:
- Digital input/output
- TCP/IP Telnet
- Profibus (optional)
- EtherCAT (optional)
- Profinet (optional)
Function description
On the aflex, the components are separated and isolated through vibrations. If re-
quired, the components can be conveyed into any areas by defined conveying direc-
tions. These movements must be adapted to the components.
The components are conveyed to the aflex as bulk material. As a rule, a bunker system
is used. The valid tapping coordinates are determined via a camera system and the
component with handling system is removed to the further stations.
An as efficient as possible cycle time implementation of the aflex consists of the fol-
lowing features:
1. The aflex is driven with the least possible drive time. This should be long enough
to re-orient the component. The "flipp" configuration is used for that purpose.
It is more effective to isolate a little many times and take camera pictures in the
mean time to isolate longer.
2. Components are only delivered if are collected in the corner of aflex over many
cycles and large quantities. In all other cases, the components are re-oriented
via flipp impulse (see point 1).
Since during transport the probability of the reorientation to an accessible posi-
tion is small, a short flip pulse is triggered after the transport.
3. The camera detects how many other components can be accessible, the last
accessible component is gripped, the aflex is controlled as soon as the handling
system moves away from the accessible surface.
4. During the switching-on phase of the bunker, the components are conveyed on
the aflex away from the bunker.