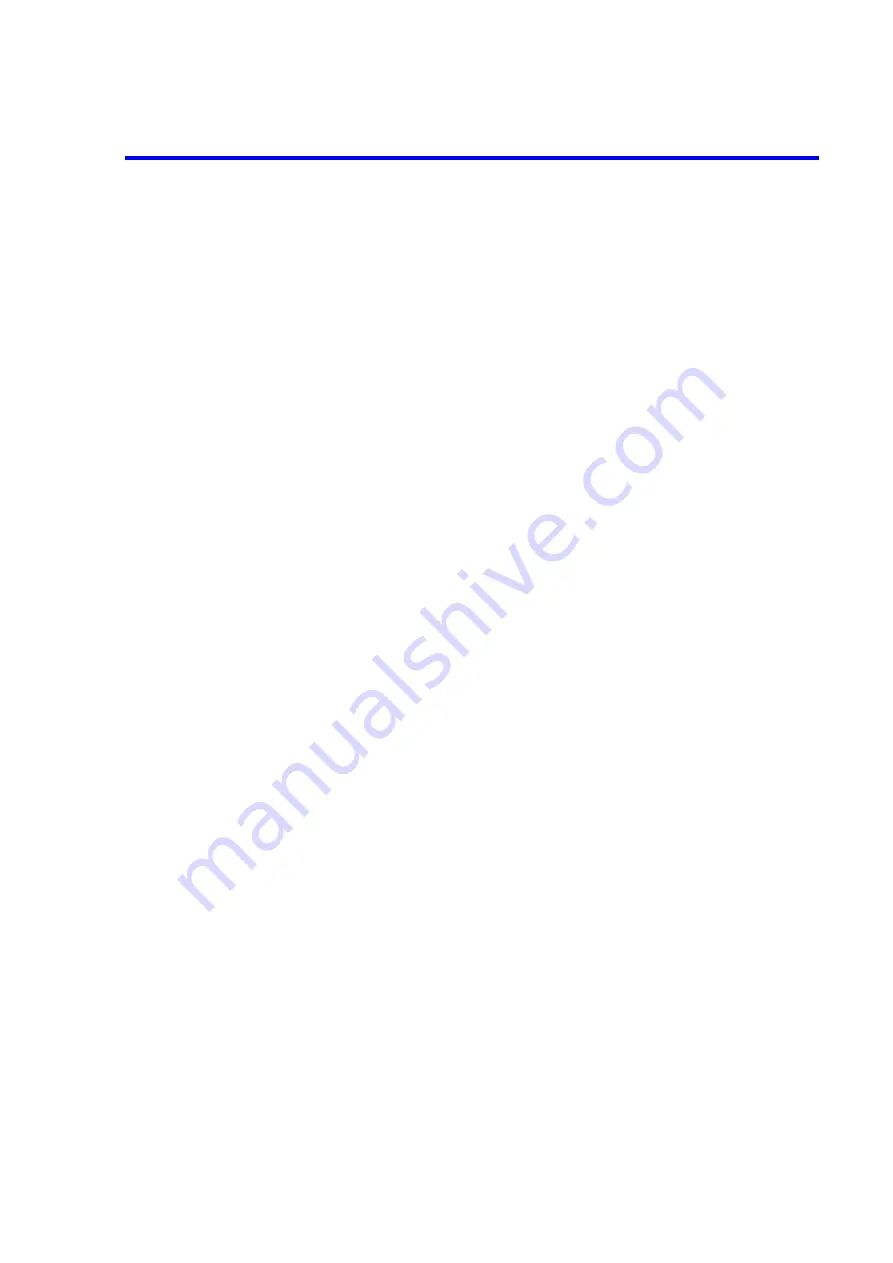
6247G/6247C DC Voltage Current Source/Monitor Operation Manual
Table of Contents
C-2
Menu Structure and Parameter Setting .......................................................
Initializing Setting Conditions ....................................................................
........................................................................................
.....................................................................................
...................................................................................
Auto Load at Power ON .............................................................................
......................................................................................
....................................................................................
.....................................................................................
................................................................
3-1
..........................................................................................
................................................................................................
4-1
.........................................................................................
AUTO Key (Measurement Range) .............................................................
DOWN Key (Source Range) ......................................................................
FIT Key (Source Range) ............................................................................
HOLD Key (Trigger Mode) .......................................................................
LIMIT Key (Limiter Setting) .....................................................................
MENU Key (Parameter Setting) ................................................................
MODE Key (Source Mode) ........................................................................
MON Key (Measurement Mode) ...............................................................
..........................................................................................
OPR/SUSPEND Key (Operating/Suspend) ...............................................
SHIFT/LOCAL Key (Shift Mode/Local) ...................................................
STBY Key (Output Standby) .....................................................................
TRIG/SWP STOP Key (Trigger/Sweep Stop) ...........................................
UP Key (Source Range) .............................................................................
VS/IS Key (Source Function) .....................................................................
123... Key (Direct Input Mode) ..................................................................
4W/2W Key (Remote Sensingn) ................................................................
.................................................................
5-1
...............................................................................................
Note for Output Terminals .........................................................................
Remote Sensing (2-Wire/4-Wire Connection) ...........................................
................................................................................
Preventing 6247G/6247C Oscillation .........................................................
Preventing DUT Oscillation .......................................................................
Connection for High Current Measurement ...............................................
Connection with Fixture 12701A ...............................................................
............................................................................................
Operations in DC Source Mode .................................................................
Operations in Pulse Source Mode ..............................................................