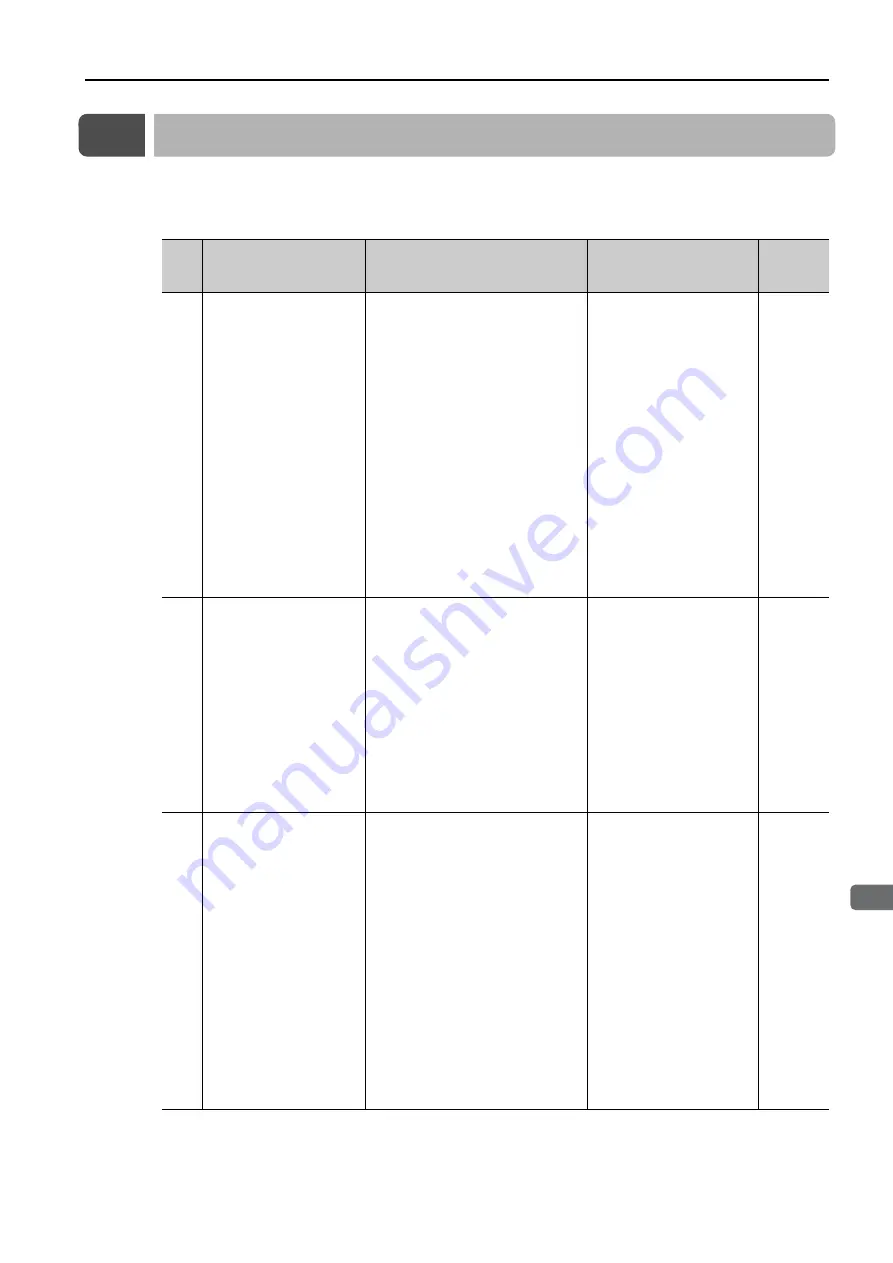
10.2 SERVOPACK Commissioning Procedure
10-3
10
Fully-Closed Loop Contr
ol
10.2
SERVOPACK Commissioning Procedure
First, confirm that the SERVOPACK operates correctly with semi-closed loop control, and then
confirm that it operates correctly with fully-closed loop control.
The commissioning procedure for the SERVOPACK for fully-closed loop control is given below.
Step
Description
Operation
Required Parameter
Settings
Con-
trolling
Device
1
Check operation of the
entire sequence with
semi-closed loop control
and without a load.
Items to Check
•
Power supply circuit
wiring
•
Servomotor wiring
•
Encoder wiring
•
Wiring of I/O signal
lines from the host con-
troller
•
Servomotor rotation
direction, motor speed,
and multiturn data
•
Operation of safety
mechanisms, such as
the brakes and the
overtravel mechanisms
Set the parameters so that the
SERVOPACK operates correctly in
semi-closed loop control without a
load and check the following
points. Set Pn002 to n.0
to
specify semi-closed loop control.
•
Are there any errors in the SER-
VOPACK?
•
Does jog operation function cor-
rectly when you operate the
SERVOPACK without a load?
•
Do the I/O signals turn ON and
OFF correctly?
•
Is power supplied to the Servo-
motor after the /S-ON signal is
sent?
•
Does the Servomotor operate
correctly when a position refer-
ence is input by the host control-
ler?
•
Pn000 (Basic Function
Select Switch 0)
•
Pn001 (Basic Function
Select Switch 1)
•
Pn002 = n.X
(External Encoder
Usage)
•
Pn20E (Electronic Gear
Ratio (Numerator))
•
Pn210 (Electronic Gear
Ratio (Denominator))
•
PnB03 to PnB12)
(Input Signal Selections)
•
PnB15 to PnB1E)
(Output Signal Selec-
tions)
SERVO-
PACK or
host con-
troller
2
Check operation with the
Servomotor connected
to the machine with
semi-closed loop control.
Items to Check
•
Initial response of the
system connected to
the machine
•
Movement direction,
travel distance, and
movement speed as
specified by the refer-
ences from the host
controller
Connect the Servomotor to the
machine. Set the moment of inertia
ratio in Pn103 using autotuning
without a host reference.
Check that the machine’s move-
ment direction, travel distance, and
movement speed agree with the
references from the host controller.
Pn103 (Moment of Inertia
Ratio)
Host con-
troller
3
Check the external
encoder.
Items to Check
Is the signal from the
external encoder
received correctly?
Set the parameters related to fully-
closed loop control and move the
machine with your hand without
turning ON the power supply to the
Servomotor. Check the following
status with the Digital Operator or
S.
•
Does the fully-closed feedback
pulse counter count up when the
Servomotor moves in the forward
direction?
•
Is the travel distance of the
machine visually about the same
as the amount counted by the
fully-closed feedback pulse
counter?
Note: The unit for the fully-closed feed-
back pulse counter is pulses,
which is equivalent to the exter-
nal encoder sine wave pitch.
•
Pn002 = n.X
(External Encoder
Usage)
•
Pn20A (Number of
External Scale Pitches)
•
Pn20E (Electronic Gear
Ratio (Numerator))
•
Pn210 (Electronic Gear
Ratio (Denominator))
•
Pn281 (Encoder Output
Resolution)
•
Pn51B (Motor-Load
Position Deviation Over-
flow Detection Level)
•
Pn522 (Positioning
Completed Width)
•
Pn52A (Multiplier per
Fully-closed Rotation)
–
Continued on next page.