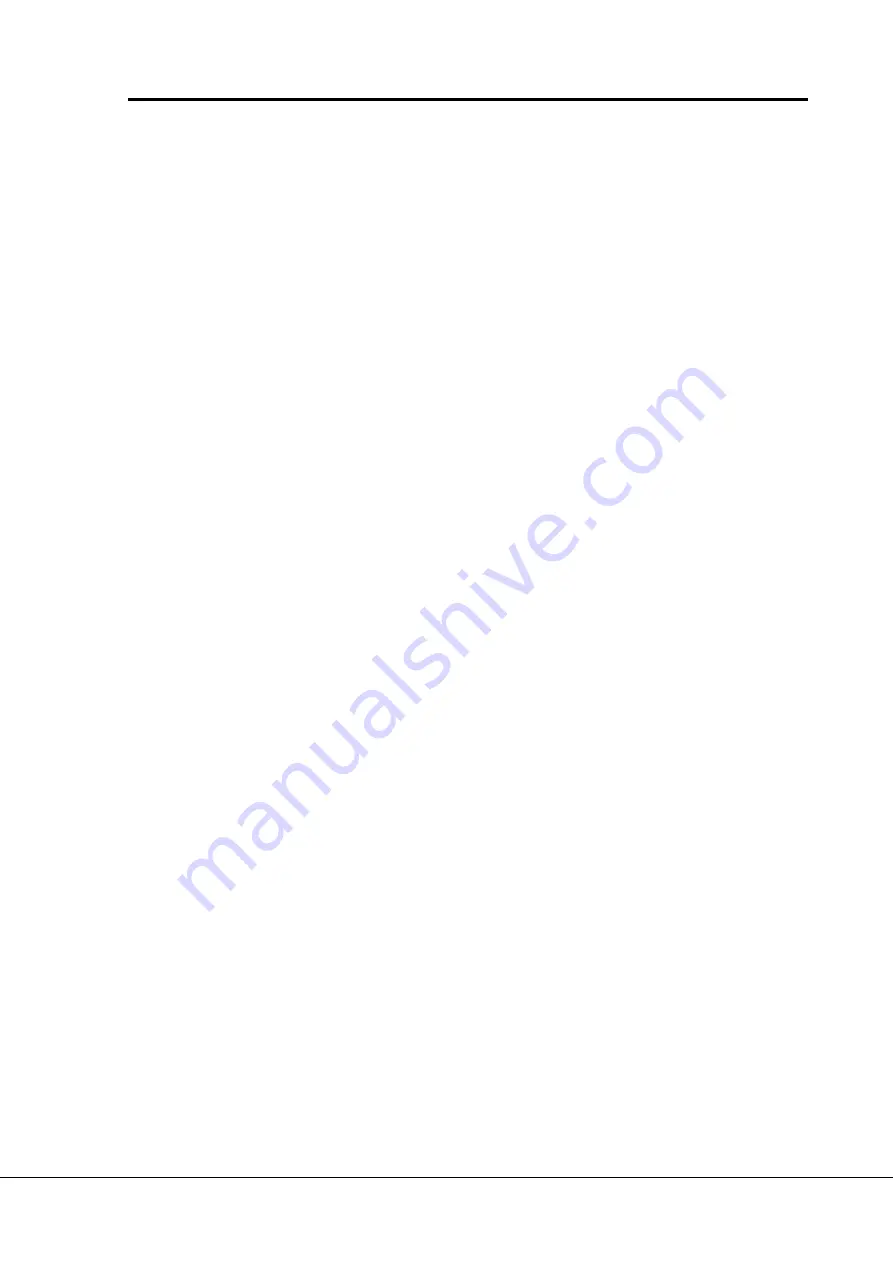
Vacon Plc
Phone: +358-201 2121
Fax:+358-201 212 205
Service: +358-40-8371 150
E-mail: [email protected]
E-mail: [email protected]
Vacon
Page 7
Pump control with autochange
5.2 Description of Group 1 parameters
1. 1, 1. 2 Minimum / maximum frequency
Defines frequency limits of the frequency converter.
The default maximum value for parameters 1
.
1 and 1
.
2 is 120 Hz. By setting 1
.
2 =
120 Hz when the device is stopped (RUN indicator not lit) parameters 1
.
1 and 1
.
2
are changed to 500 Hz. At the same time the panel reference resolution is changed
from 0.01 Hz to 0.1 Hz.
Changing the max. value from 500 Hz to 120 Hz is done by setting parameter 1
.
2 =
119 Hz when the device is stopped.
NOTICE!
Start frequency of the auxiliary drive is not conditional on maximum
frequency because in the application start frequency and stop frequency of the
auxiliary drives are scaled by the endower of the system.
1. 3, 1. 4 Acceleration time 1, deceleration time 1:
These limits correspond to the time required for the output frequency to accelerate
from the set minimum frequency (par. 1
.
1) to the set maximum frequency
(par. 1
.
2).
1. 5
PI-controller gain
This parameter defines the gain of the PI-controller.
If this parameter is set to 100%, a 10% change in error value causes the controller
output to change by 10.0 Hz.
If the parameter value is set to 0 the PI-controller operates as I-controller.
1. 6
PI-controller I-time
Defines the integration time of the PI-controller.
1. 7
Current limit
This parameter determines the maximum motor current from the frequency converter.
To avoid motor overloading set this parameter according to the rated current of the
motor.
1. 8
U/f ratio selection
Linear:
The voltage of the motor changes linearly with the frequency in
the constant flux area from 0 Hz to the field weakening point
0
(par. 6
.
3) where the nominal voltage is supplied to the motor. See
figure 6.4-1.
Linear U/f ratio should be used in constant torque applications.
This default setting should be used if there is no special demand for another
setting.
Squared:
The voltage of the motor changes following a squared curve form
with the frequency in the area from 0 Hz to the field weakening
1
point (par. 6
.
3) where the nominal voltage is supplied to the motor.
See figure 6.4-1.
The motor runs undermagnetised below the field weakening point
and produces less torque and electromechanical noise. Squared U/f
ratio can be used in applications where torque demand of the load is
proportional to the square of the speed, e.g. in centrifugal fans and
pumps.