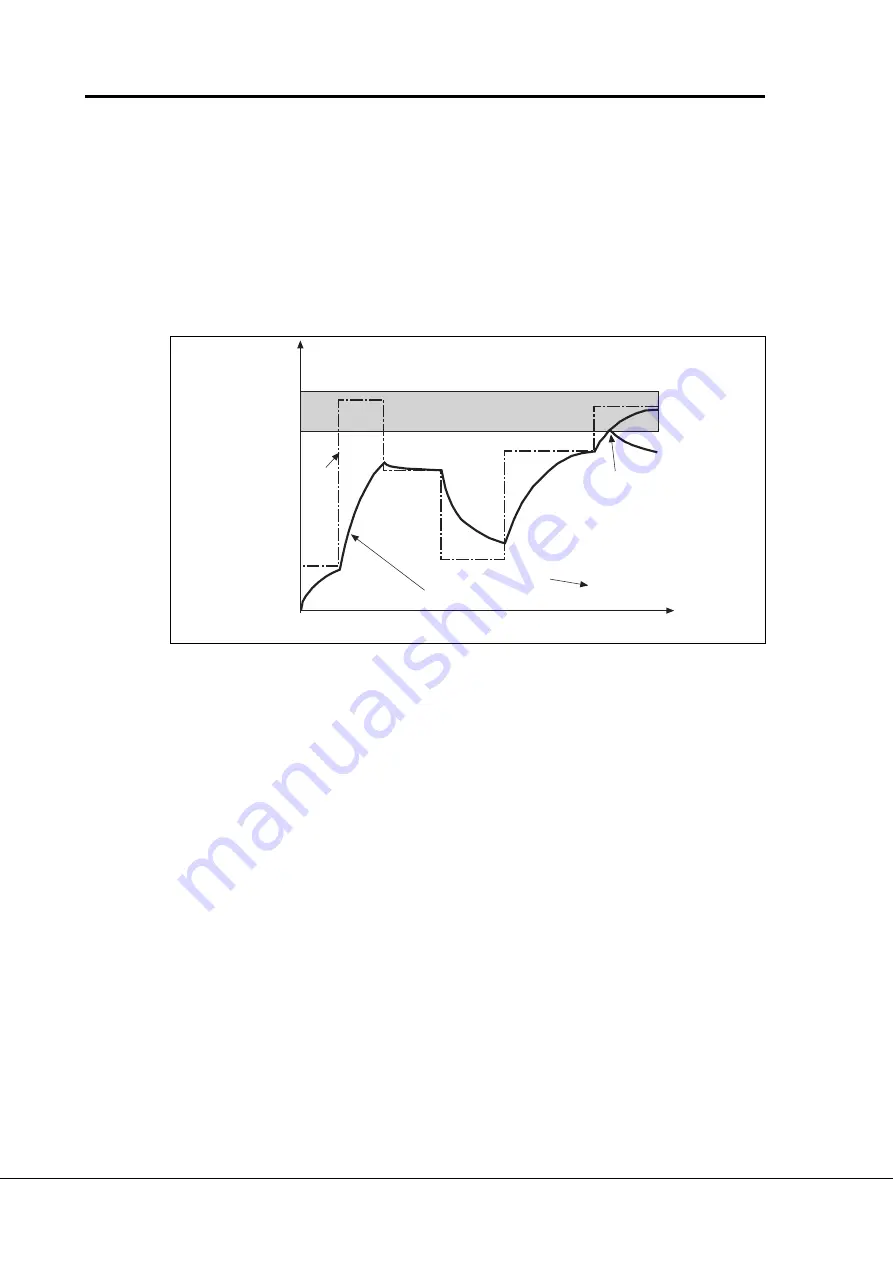
Vacon Plc
Phone: +358-201 2121
Fax:+358-201 212 205
Service: +358-40-8371 150
E-mail: [email protected]
Page 40
Vacon
Pump and fan control with autochange
7. 9
Motor thermal protection, break point frequency
The frequency can be set between 10—500 Hz.
T h i s
is the break point of thermal current curve. With frequencies above this point the
thermal capacity of the motor is assumed to be constant. Refer to the figure 6-19.
The default value is based on the motor's name plate data, parameter 1
.
11. It is 35
Hz for a 50 Hz motor and 42 Hz for a 60 Hz motor. More generally, it is 70% of the
frequency at field weakening point (parameter 6
.
3). Changing either parameter 1
.
11 or 6
.
3 will restore this parameter to its default value.
Figure 6-20 Calculating motor temperature
105%
par. 7
.
5
Θ
= (I/I
T
)
2
x (1-e
-t/T
)
I/I
T
UMCH7_92
Trip area
Motor temperature
Time
Motor temperature
Time constant T
*)
*)
Changed with motor size and
adjusted with parameter 7
.
8
Trip/warning
Motor
current
7. 10
Stall protection
Operation:
0 = Not in use
1 = Warning
2 = Trip function
Tripping and warning will display the same message code. If the tripping is set on,
the drive will stop and activate the fault stage.
Setting the parameter to 0 will deactivate the protection and will reset the stall time
counter to zero.
Parameters 7. 10— 7. 13, Stall protection
General
Motor stall protection protects the motor from short time overload situations caused by e.g. a
stalled shaft. The reaction time of stall protection can be set shorter than that of motor thermal
protection. The stall state is defined with two parameters, 7.11. Stall Current and 7.13. Stall
Frequency. If the current is higher than the set limit and output frequency is lower than the set
limit the stall state is true. There is actually no real indication of the shaft rotation. Stall protection
is a type of overcurrent protection.